Nitrogen+Syngas 396 Jul-Aug 2025
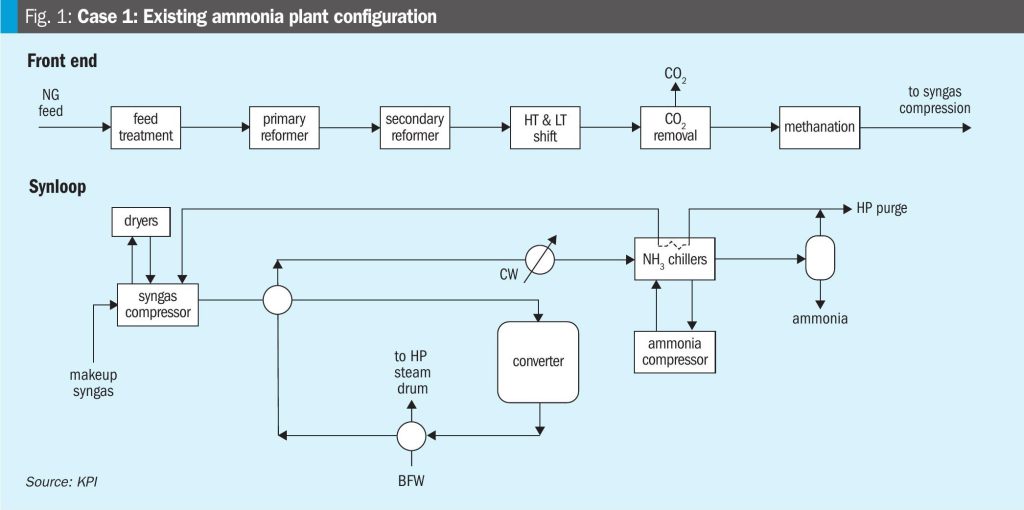
9 July 2025
Challenges in the conversion to clean ammonia
CLEAN AMMONIA
Challenges in the conversion to clean ammonia
VK Arora of KPI examines the technical and operational challenges of decarbonising legacy and new ammonia plants, drawing on a European case study of full-scale conversion supported by robust process and integration design. The article also presents three US case studies exploring partial strategies, such as green hydrogen blending and oxygen enrichment, to reduce CO2 emissions and improve throughput. Together, these examples highlight a phased, cost-effective approach to decarbonisation, with blue hydrogen serving as a near-term transitional feedstock.
The decarbonisation of legacy ammonia plants presents notable technical and economic challenges. However, with robust conceptual and process design, coupled with strategic integration planning, the extent of required modifications, and associated capital costs, can be significantly reduced. While these facilities were originally designed for hydrogen sourced via unabated steam methane reforming (SMR), many core systems, such as synthesis loops, compression trains, and heat recovery units, can be adapted to accommodate low-carbon feedstocks, including green and blue hydrogen. This enables a phased decarbonisation pathway, where blue ammonia serves as a transitional step toward fully renewable production. By leveraging existing infrastructure and applying targeted retrofits, operators can pursue a cost-effective and minimally disruptive transition that aligns with evolving regulatory expectations and long-term emissions reduction goals.
Overview of study cases
This article presents four techno-economic evaluations conducted by Kinetics Process Improvements, Inc. (KPI), each offering a distinct perspective on clean ammonia transition strategies. The case studies span full-scale conversions and partial integrations, reflecting a range of plant configurations, regional drivers, and decarbonisation approaches:
Case 1 – Full conversion from grey to clean ammonia
A comprehensive redesign of an existing ammonia synthesis loop for a legacy plant in Europe was undertaken to enable operation exclusively on clean hydrogen, sourced primarily from the European Hydrogen Backbone (EHB) pipeline and supplemented by over-the-fence (OTF) hydrogen from urban solid waste (USW) gasification. The study evaluated major retrofits, including the installation of a new feed purification system to remove trace impurities and the complete phase-out of conventional reforming and CO2 capture systems. Key regulatory and infrastructure drivers for this full-scale transition are discussed in detail later.
Case 2 – Debottlenecking a new ammonia facility via green hydrogen and oxygen integration
At a newly built US ammonia plant equipped with cryogenic purification technology, KPI investigated the injection of green hydrogen and moderate oxygen enrichment to also alleviate specific bottlenecks. These included overloaded arch burners, elevated tube metal temperatures in the steam methane reformer (SMR), and limitations in the cryogenic purifier. The integration strategy aimed to reduce carbon intensity, improve reliability, and achieve a modest increase in ammonia production.
Case 3 – Hydrogen and oxygen integration in a legacy ammonia plant
A legacy ammonia facility explored the integration of green hydrogen and moderate oxygen enrichment using a 20 MW electrolyser system. While the oxygen enrichment pathway was ultimately deemed uneconomical due to the requirement for a dedicated compressor, the plant successfully implemented green hydrogen injection. As an early adopter, the facility capitalised on Inflation Reduction Act (IRA) incentives, achieving a viable business case despite high capital expenditure.
Case 4 – Green hydrogen integration to increase plant capacity
A smaller U.S.-based ammonia plant evaluated the injection of green hydrogen to increase production by approximately 20% while reducing carbon intensity. The plant had already installed a new converter rated at 120% capacity, but was constrained by limited syngas supply from the front end. Key drivers included the high cost of trucked-in ammonia (~20% of total output) and the availability of competitively priced green hydrogen. Multiple nitrogen sourcing options were assessed, with over-thefence supply emerging as the most cost-effective solution.
Case 1 drivers for full-scale conversion at European location
Europe’s clean ammonia transition is driven by tightening carbon policy and expanding hydrogen infrastructure. The inclusion of hydrogen under the EU ETS, with carbon prices at €80 to €90/tCO2, and the upcoming CBAM mechanism are raising the cost of unabated production and imports.
While initiatives such as REPowerEU and the European Hydrogen Backbone are advancing the deployment of electrolysers and pipeline connectivity, high gas prices and funding delays have slowed progress. Still, a phased conversion strategy, anchored in robust conceptual and process design, can minimise facility modifications and reduce capital intensity. For producers, this approach provides a pragmatic path to lower carbon exposure, aligns with regulatory trends, and enables access to emerging low-carbon markets.
Case 1 – Full conversion from grey to clean ammonia
Existing ammonia plant
The facility under study is a legacy ammonia plant constructed in the 1980s, currently operating at approximately 1,765 short tons per day using natural gas as the primary feedstock. The plant follows a conventional process flow scheme, as illustrated in Fig. 1.
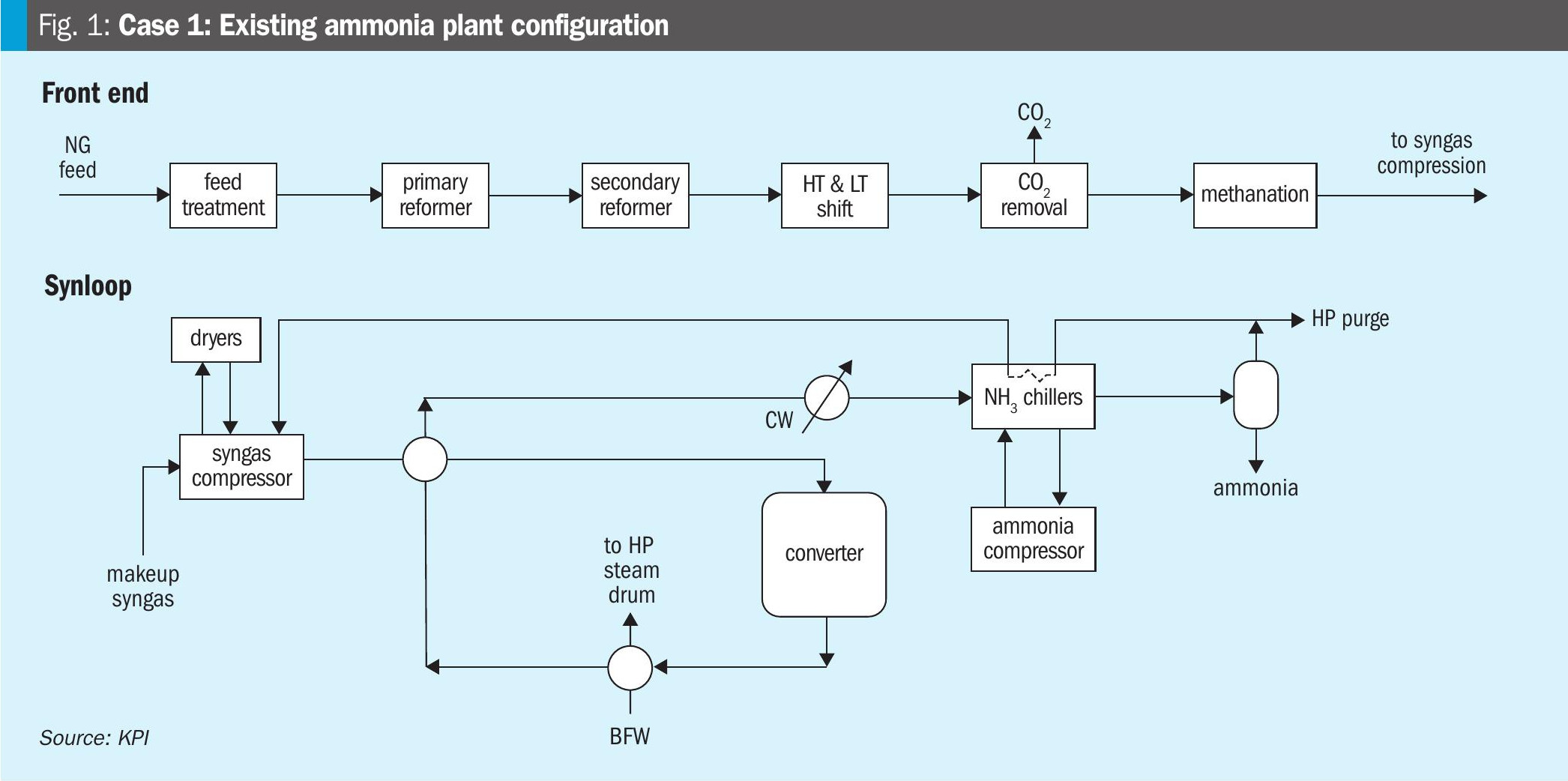
The existing steam system is also traditional in design. The syngas compressor turbine is driven by high-pressure (HP) steam, supplied from a header operating at approximately 1,800 psi. Meanwhile, the process air compressor turbine and the ammonia refrigeration compressor turbine are both connected to a medium-pressure (MP) steam header, operating at around 600 psi.
This baseline configuration served as the foundation for evaluating the technical and economic feasibility of a complete conversion to clean ammonia production using low-carbon hydrogen feedstocks.
Hydrogen and nitrogen sourcing
The clean ammonia facility will utilise two distinct hydrogen feed sources:
- OTF hydrogen produced via USW gasification, available from an adjacent third-party supplier;
- pipeline-supplied hydrogen delivered through the EHB network, expected to come online in alignment with the pipeline’s phased commissioning schedule.
The USW-derived hydrogen will be available in limited quantities, sufficient to support approximately 35 to 40% of the plant’s total ammonia production capacity. The EHB pipeline will meet the remaining hydrogen requirement as infrastructure becomes operational.
Nitrogen feed will be supplied over-the-fence via a dedicated pipeline from a nearby air separation unit (ASU), ensuring consistent purity and pressure for integration into the synthesis loop.
Feedstock quality
The hydrogen supplied via pipeline originates from diversified production sources and contains trace levels of several contaminants that must be addressed before synthesis. Key impurities identified in the feed include: chlorides, sulphur-inorganic compounds, CO, CO2, O2, formic acid and formaldehyde.
These impurities pose a risk to both catalyst performance and the integrity of downstream equipment. In particular, sulphur compounds and CO are known catalyst poisons, while chlorides can also contribute to corrosion and fouling. Effective purification strategies are crucial for reducing these contaminants to levels compatible with the specifications of ammonia synthesis catalysts and ensuring long-term plant reliability.
Key challenges and mitigation
The listed impurities in the hydrogen are poisonous to the synthesis catalyst and need to be removed well below the acceptable limits. The following challenges were posed for the design of the new hydrogen purification system:
- A viable and cost-effective method for removing formic acid and formaldehyde was not available. Additionally, leading catalyst vendors lacked prior experience with these compounds, and the industry’s understanding of their behaviour within the ammonia production process remains limited. A layer of special adsorbent was suggested to be added to the existing dryers to partially mitigate traces of formic acid and formaldehyde.
- Limited degree of H2 feed preheat (<500°F) due to the unavailability of HP steam. This means that the conventional catalysts used in ammonia plant feed purification cannot be used to remove the impurities. Alternative lower-temperature catalysts were reviewed and carefully configured, incorporating numerous feedback points from different catalyst suppliers.
- To minimise the cost, the existing desulphurisers and methanation vessels were intended to be used.
A limited availability of feed hydrogen for an extended period also posed a challenge for the proper selection of the syngas compressor configuration.
Considering the low turndown requirements for the syngas compressor over an extended period and the cost of additional power consumption in the recycle mode of operation, the cost-benefit analysis suggested using two 50% compressors. Furthermore, it was also determined that the amount of MP superheated steam production within the synloop will permit the operation of one 50% syngas compressor on the steam driver. This combination also provides an added flexibility in the operation with improved reliability.
Challenges of synloop re-rating and re-configuration
The transition of the ammonia synthesis loop from conventional methane-based syngas, typically containing substantial levels of inert components such as argon and methane, to a stoichiometric blend of high-purity hydrogen and nitrogen introduces a suite of complex process and engineering challenges. The virtual elimination of inert materials has a significant impact on both the catalyst bed’s thermodynamic equilibrium and kinetics, as well as the overall hydraulic assessment of the synloop. Change in the circulation rate coupled with changes in the temperature profile impacts heat exchanger duties, system pressure drops, and the turndown capability of syngas compressors.
Elevated reactant partial pressures in the feed stream shift the equilibrium conversion, enhancing ammonia yield per pass. However, this gain also requires recalibration of the reactor temperature, pressure profile and rerating to mitigate risks such as catalyst sintering or localised hotspots. A thorough evaluation of equilibrium and kinetics performance, hydraulics of the synloop, and the mechanical integrity of existing equipment, originally engineered for higher inert dilution and different gas compositions, is essential.
KPI undertook a comprehensive re-rating of the entire synthesis loop across all projected operating scenarios, including a detailed kinetics assessment of the converter beds. This resulted in the optimisation of critical operating parameters, including inert concentration, pressure, circulation rate, bed temperature profiles, pressure drop behaviour, heat exchanger loads, and compressor performance (for both syngas and ammonia services). Catalyst bed profiles were further validated through collaboration with all major catalyst suppliers to ensure the desired temperature profiles and ammonia production rates were achievable.
Key variables, including inert levels, circulation rate, ammonia conversion, and operating/pressure drop characteristics, were mapped across both normal and turndown modes for clean ammonia production and benchmarked against baseline grey ammonia operations as shown in Fig. 2.
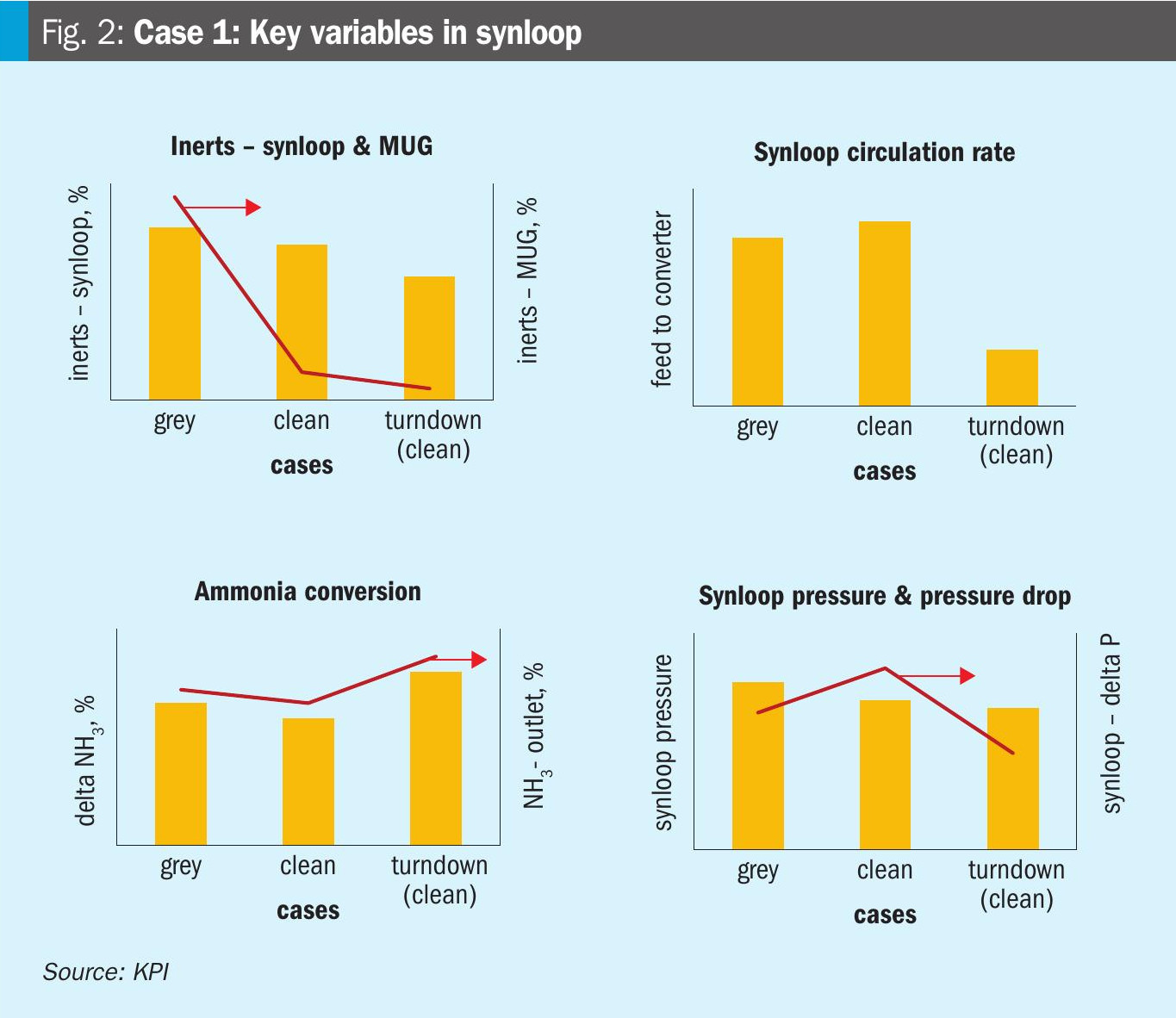
In addition to process refinements, the configuration was adapted to accommodate superheated steam generation for the compressor drivers. This involved replacing the existing high-pressure boiler feedwater exchanger with a new medium-pressure steam generator coupled with a superheater.
New plant configuration
In the revamped configuration, the majority of the front-end equipment from the legacy ammonia plant is decommissioned. However, several components, including the existing desulphurisers, methanation vessels, and selected heat exchangers, were successfully repurposed within the new feed purification unit designed for blended hydrogen and nitrogen streams. Major modifications to the synthesis loop (synloop), illustrated in Fig. 3, include:
- reconfiguration of the syngas compression system with two new 50% capacity compressors, one steam-driven and the other motor-driven, for operational flexibility and improved turndown performance;
- installation of a medium-pressure (MP) steam generator and superheater by replacing the high-pressure boiler feed-water (HP BFW) exchanger within the synloop;
- addition of a new feed preheater in the purification section, utilising steam to optimise the feed temperature before synthesis.
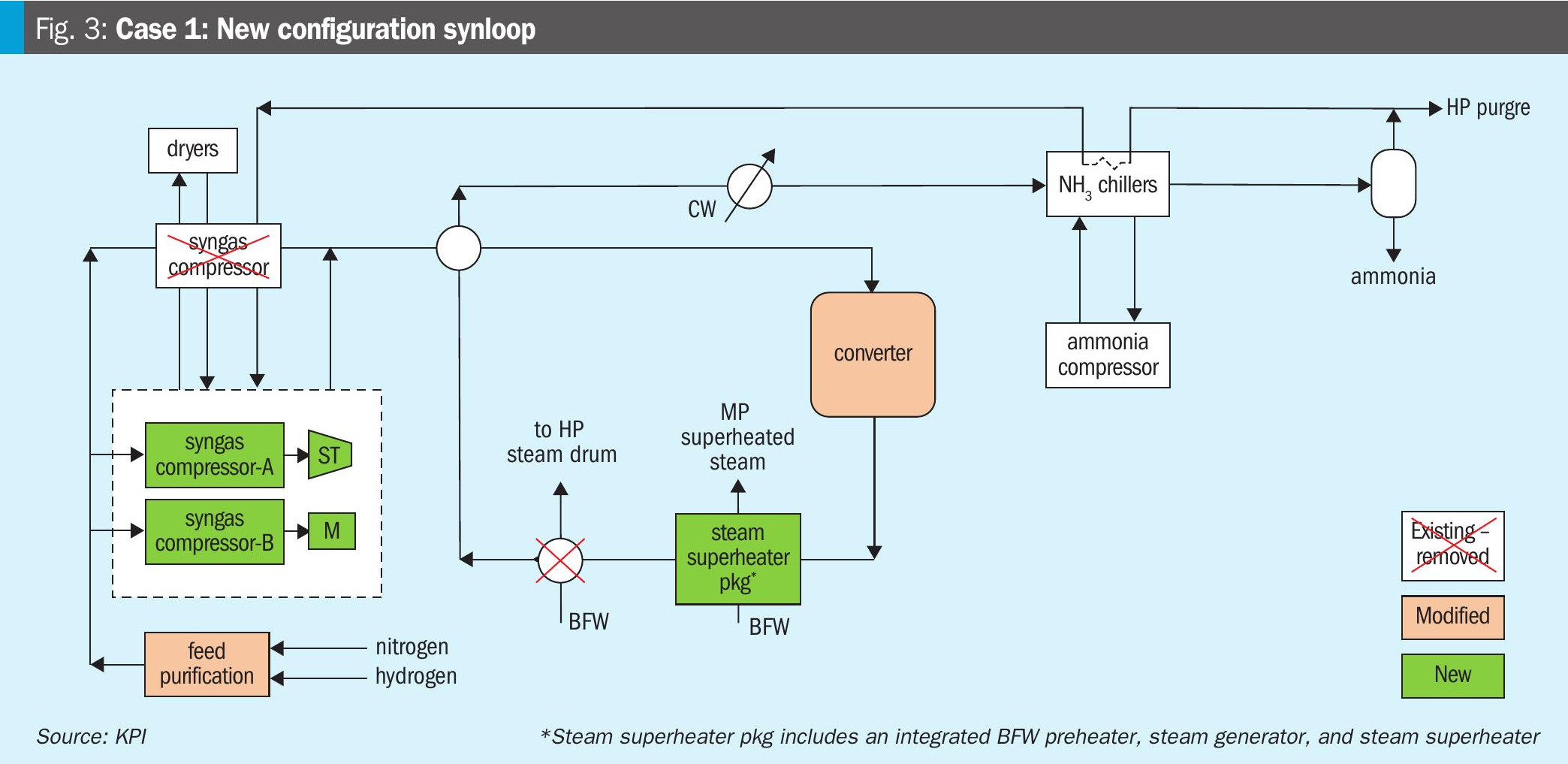
Steam system
The redesigned steam system is thermally balanced to minimise external steam import. MP superheated steam is generated within the synloop and used to drive one of the new syngas compressors.
The ammonia refrigeration compressor turbine is also powered by MP steam, ensuring efficient energy utilisation across the cycle. A minimal amount of steam is imported for a well heat-integrated purification section.
Specific energy consumption
The specific energy consumption for clean ammonia production is estimated to be approximately 16% lower than that of the existing plant (on a higher heating value basis). This figure accounts for the energy content of the hydrogen feed, power required for nitrogen production, steam import/export credits, and auxiliary power consumption (e.g, compressors and pumps).
Carbon emissions
Scope 1 carbon emissions for the clean ammonia configuration are projected to be less than 0.2% of those from the existing plant. For reference, the current facility emits approximately 1.8 tonnes of CO2 per tonne of ammonia produced. This dramatic reduction underscores the decarbonisation potential of complete hydrogen substitution and process electrification.
Economic justification
The economic rationale for complete conversion to clean ammonia production is reinforced by a convergence of regulatory, financial, and infrastructure developments across Europe. Stringent environmental policies, notably the tightening of the EU Emissions Trading System (ETS) and the phased implementation of the Carbon Border Adjustment Mechanism (CBAM), are driving up the cost of carbon-intensive production. With carbon prices exceeding €80 to 90 per tonne of CO2 and free allowances set to diminish, legacy ammonia plants face mounting compliance costs.
Simultaneously, the expansion of hydrogen infrastructure, including the European Hydrogen Backbone, is improving access to low-carbon hydrogen at scale. These developments, combined with funding mechanisms such as the EU Innovation Fund and national-level incentives, significantly enhance the financial viability of clean ammonia projects.
In this context, the studied facility’s transition to clean hydrogen feedstock, sourced from both over-the-fence gasification and the EHB pipeline, offers a compelling long-term business case. The project has already advanced into the detailed engineering phase, supported by favourable policy alignment, infrastructure readiness, and a clear pathway to mitigate carbon risk and achieve market differentiation.
Case 2 – Debottlenecking a new ammonia facility via green hydrogen and oxygen integration
This US-based ammonia plant, operating at approximately 2,800 short t/d (~115% of nameplate capacity), features a modern configuration that includes a cryogenic purifier for removing inert gases and excess nitrogen from the syngas stream. During the initial evaluation, KPI identified several systems operating beyond their design limits, most notably the cryogenic purifier and the arch burners. Overfiring of the arch burners posed a reliability risk to the radiant tubes. At the same time, the overloaded cryogenic purifier resulted in increased purge gas losses to the fuel system, thereby reducing overall energy efficiency.
As part of a broader decarbonisation initiative, the facility proposed installing a 20 MW electrolyser to integrate green hydrogen into the process. The primary objective was to reduce carbon emissions and leverage the IRA incentives to establish a viable economic case. Given the limitations of the arch burners and cryogenic purifier, KPI recommended a combined strategy: injecting green hydrogen downstream of the purifier, along with moderate oxygen enrichment.
Key findings from the study:
- Arch burner firing could be reduced by ~9%, bringing operation well within design limits.
- Radiant tube outlet temperatures decreased by ~34°F, with even greater reductions in tube metal temperatures, enhancing reliability and extending tube life.
- Cryogenic purifier loading was reduced, resulting in lower inert gas content in the make-up gas and a corresponding decrease in purge rate.
- Post-combustion CO2 emissions were reduced by ~9%. Additional CO2 emissions from the auxiliary boiler (used to offset a minor MP steam shortfall) were fully accounted for in the net emissions balance.
- Feed and fuel consumption decreased by ~0.3 million Btu/ST compared to the base case.
- Oxygen injection was deemed feasible without a dedicated compressor based on commercial precedent. However, if a separate compressor were required, the economic viability of oxygen enrichment would be compromised.
Current status
The electrolyser project is currently on hold due to uncertainty surrounding the long-term availability of IRA incentives.
Case 3 – Hydrogen and oxygen integration in a legacy ammonia plant
This legacy U.S.-based ammonia facility, operating at 1,800 short t/d, evaluated the partial integration of green hydrogen and oxygen from a 20 MW electrolyser system to reduce carbon intensity and modestly increase production. The study, conducted by KPI, shared similar objectives with Case 2, though without the added benefits of cryogenic purification. The project drivers were:
- Initiate decarbonisation through partial integration of green hydrogen.
- Gain operational experience with green ammonia production technologies.
- Leverage federal and state incentives under the IRA to establish a viable business case.
Integration strategy
The plant investigated injecting green hydrogen downstream of the methanator, along with moderate oxygen enrichment. However, the requirement for a dedicated oxygen compressor significantly increased capital and operating costs, rendering the oxygen enrichment pathway economically unfeasible.
Implementation and outcomes
Despite shelving the oxygen integration, the facility successfully implemented green hydrogen integration using the 20 MW electrolyser system. As an early mover, the plant was well-positioned to capitalise on IRA and state-level incentives, enabling a commercially viable transition. The project also yielded valuable operational insights into the handling and integration of green hydrogen within a legacy ammonia framework.
Case 4 – Green hydrogen integration to increase plant capacity
This US-based ammonia facility, currently operating at 550 short t/d, features a high-pressure synthesis loop (>4,000 psi) and reciprocating compressors. The plant recently installed a new, high-efficiency converter rated for approximately 120% of its nameplate capacity. However, the front-end reforming section remains unmodified. To capitalise on the converter’s latent capacity, the plant pursued a third-party offtake agreement for green hydrogen, aiming to expand production without major front-end upgrades.
The project drivers were:
- Replace ~100 short t/d of trucked-in ammonia with on-site production to reduce logistics costs.
- Leverage IRA incentives to lower carbon intensity and improve project economics.
- Utilise existing downstream capacity to minimise capital investment and operational disruption.
Integration study
KPI conducted a detailed evaluation of green hydrogen integration strategies to support an additional 100 short t/d of ammonia production. The study also assessed nitrogen supply options, including front-end upgrades and on-site generation via PSA and cryogenic systems.
Key findings
Over-the-fence nitrogen supply emerged as the most cost-effective solution, offering the lowest capital expenditure, minimal production loss, and the shortest turnaround time.
The integration strategy avoids overloading the existing reformer and compression systems, enabling a streamlined capacity increase.
Current status
While technically viable and economically attractive under current policy frameworks, the project is under review due to uncertainty surrounding the long-term availability of IRA incentives. Alternative pathways are being explored to maintain project momentum.
Conclusions
- The complete conversion of legacy ammonia facilities, particularly across Europe, offers significant potential, driven by stringent environmental regulations, rising carbon costs, and the development of emerging hydrogen pipeline infrastructure.
- For the complete conversion of Case 1, a careful and comprehensive assessment of the synloop, particularly of the converter, must be conducted to determine new optimum operating parameters for different scenarios, ensuring compliance with the maximum permissible temperature limits of the catalyst and materials and minimising the purge.
- For the complete conversion of Case 1, the syngas compressor configuration and the type of driver selection should be based on a lifecycle cost-benefit analysis, considering the frequency and duration at turndown rates, and accordingly, the steam system should be balanced to minimise the import.
- Moderate, targeted oxygen enrichment represents a technically and economically feasible retrofit. It preserves mechanical integrity and does not require additional compression systems, as commercially demonstrated. However, if the plant insists on adding a dedicated compressor, then the oxygen enrichment option is not economically viable.
- Applied selectively, oxygen enrichment mitigates primary reformer constraints by lowering radiant tube metal temperatures and reducing arch firing loads. This results in improved operational reliability, modest gains in ammonia yield, and lower post-combustion CO2 emissions.
- The strategic injection of green or blue hydrogen downstream of cryogenic purification units provides critical relief for bottlenecked systems. This improves overall ammonia plant efficiency and enhances reliability by reducing excess purge gas losses to the fuel system.
- Although technically viable, integrating electrolyser-based green ammonia into existing plants remains commercially infeasible without robust support mechanisms such as tax credits, carbon pricing, or premium pricing for clean ammonia.