Nitrogen+Syngas 396 Jul-Aug 2025
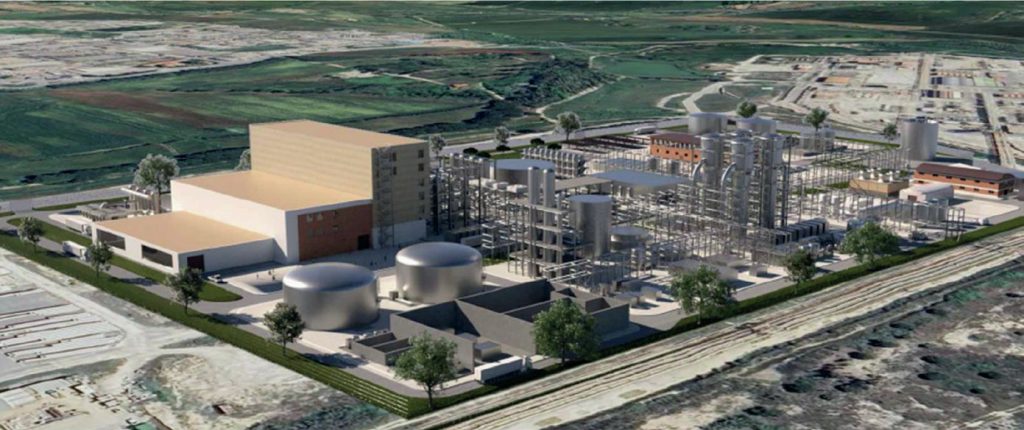
8 July 2025
Waste to methanol to maritime fuel
DECARBONISATION
Waste to methanol to maritime fuel
The production of methanol from waste offers a groundbreaking solution for sustainable urban waste management as well as producing an alternative renewable fuel for maritime transport. Giacomo Rispoli, Andrea Angeletti and Alessia Borgogna of Nextchem provide an overview of the waste conversion process and its application.
Using fossil fuels to power the world economy has become unsustainable as the speed of human activity outpaces the natural processes needed to renew the Earth’s resources. Moreover, fossil fuels create emissions and waste that harm the planet and impact economic growth. Adopting a circular economy is one way of reducing the production cycle by emphasising waste reduction, reuse, recycling, and energy recovery.
Circular economy processes also include the thermochemical conversion of waste into new chemical products, a sustainable solution that provides an alternative to conventional disposal methods. When applied to non-recyclable waste, the chemical conversion reintegrates these materials into the production cycle.
Unrecyclable plastic residue is the main example: about 40% of the total differentiated plastic becomes non-recyclable waste. Another example is unsorted municipal solid waste, that can be processed to be biologically stabilised and to reduce its volume. Through mechanical and biological treatments, the waste becomes drier and has a lower calorific value, ranging between 14 and 18 MJ/kg (approximately one third of gasoil LVH). Lastly, wood demolition waste, which despite its frequent contamination by halogenated compounds and heavy metals which makes it difficult to treat in traditional waste to energy plants, remains a valuable source of biogenic carbon for the production of fuels and chemicals.
Chemical recycle of waste can clearly play an important role in making the transportation sector more sustainable by creating clean fuels. This article discusses how waste-to-methanol can be used in the maritime industry, which is reducing its emissions to comply with new EU rules that took effect January 1, 2025 calling for an 80% reduction in maritime emissions by 2050.
Global waste production trends
Although the focus on recycling is continuously increasing, waste production itself is also on the rise (Fig. 1). By 2050, the global population is expected to reach about 10 billion, accompanied by an increase in the GDP of many developing countries. Consequently, both global and per capita waste production is set to increase, as higher GDP in the past has been dramatically linked to the growth of a “take-make-dispose” economy.

Waste-to-energy is responsible for emissions of significant amounts of GHG gases (mainly CO2 and NOx). European incinerators that produce energy generate a significant amount of direct CO2 emissions (580g CO2eq/kWh), which is twice the current average amount generated by the EU28 electricity grid (298g CO2eq per kWh) and significantly greater than energy produced through conventional fossil fuel sources such as gas.
In Europe, the waste management sector is a significant contributor to methane emissions, ranking as the second largest emitter, with approximately 97 million tonnes of carbon dioxide equivalents (CO2eq) emitted in 2022, according to the EEA.
The NX Circular™ gasification technology commercialised by MyRechemical, Nextchem’s subsidiary dedicated to wasteto-chemical solutions, sinks its roots in a very robust industrial track record with more than 20 years of industrial experience and more than 2 million hours of total operation. The pure oxygen gasification and inert melting process was specifically designed for difficult waste disposal at the end of the 1990s and largely applied to produce high value syngas. MyRechemical, leveraging MAIRE group’s experience in gas processing and Nextchem’s technology portfolio, combined this process with syngas conversion to valuable fuels and chemicals (hydrogen, methanol, ethanol, sustainable aviation fuels, fertilizers, olefins).
This integrated approach from waste to fuels and chemicals is a game-changer for the energy transition path, seamlessly blending proven technologies with groundbreaking environmental innovations.
The primary innovation introduced by MyRechemical is the integration of waste management and chemical synthesis sections. Producing valuable molecules from waste offers a sustainable solution for urban waste management. The waste-to-chemical technology commercialised and licensed by MyRechemical is nearing final implementation following the agreement between Nextchem and Eni for the first industrial waste-to-methanol plant in an existing refinery assuring its transition to sustainable sources.
Using waste as a feedstock is beneficial not only for the environment and the community but also brings economic advantages. Instead of being a cost, the feedstock becomes a revenue source, with its value ranging from EUR 50 to EUR 250 per ton, depending on the kind of waste and geography.
Waste conversion to methanol process
The process of converting waste to methanol consists of four main sections:
• Waste gasification
• Syngas cleaning and purification
• Syngas conditioning
• Methanol synthesis from conditioned syngas
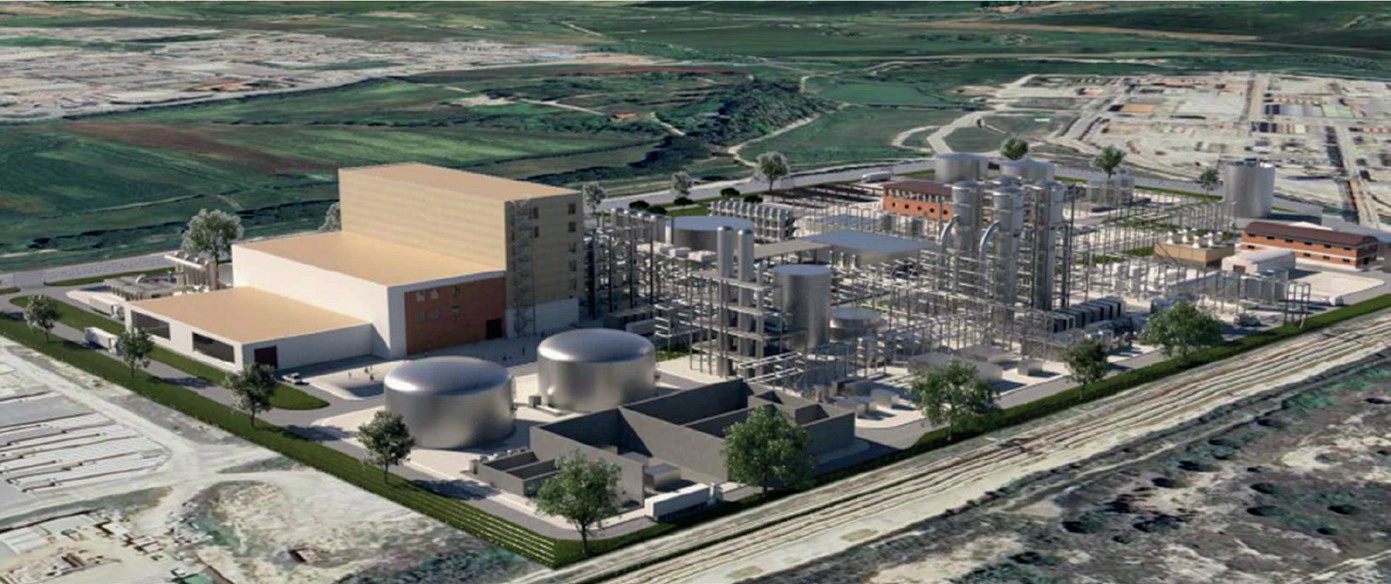
High-temperature conversion (gasification) and cleaning and purification
The core section of the waste-to-methanol process is the NX Circular™ gasification unit. The high-temperature gasifier is capable of simultaneously converting the combustible fraction of the waste into syngas and melting the inert fraction, producing an inert vitrified solid once the molten slag is cooled. This system uses pure oxygen as the gasifying agent. The temperatures reached at the melting section in the bottom of the reactor are very high, between 1,600 and 2,000°C, ensuring the melting of the slag and the total conversion of the waste. In the intermediate section, the gasification section, near the solid inlet, the temperature drops to around 700°C, then rises again in the upper section of the reactor, the stabilisation section, to at least 1,100°C, thanks to the introduction of additional oxygen. A minimum temperature of 1,100°C is necessary to ensure the breakdown of longer-chain compounds (tar) and complexes such as dioxins, which are particularly harmful. To prevent the reformation of dioxins, which become stable again at 800°C, the produced syngas is rapidly cooled through an evaporative quench to about 90°C. This abrupt cooling preserves the syngas composition at its optimal quality. The cooled syngas needs to be cleaned through two washing columns, one alkaline and one acidic. The main components of the cleaning section are two washing columns, a wet electrostatic filter, and an additional sub-cooled column for the removal of metals.
Downstream of these two sections, a clean syngas is obtained with a composition within the following ranges: H2 = 37.5 to 41%; CO = 36 to 46%; CO2 = 15.5 to 5%; H2O = ~5%. The composition of the produced syngas is obviously dependent on the composition of the waste, which, by its nature, is variable. The criticality of the process lies precisely in the heterogeneity of the waste, which results in the production of a syngas that varies both in terms of composition and flow rate. The conditioning and synthesis sections, however, need to operate under stable flow conditions. Therefore, the washing and conditioning sections are connected by a gasometer, i.e., a syngas tank, which allows the damping of flow rate fluctuations.
Once compressed, syngas is routed to the purification section involving the following steps: removal of residual dust and metals, removal of HCl, hydrolysis of the COS and HCN, H2S removal through an oxy-reduction system and a final polishing step based on zinc oxide absorbents in order to reduce sulphur content down to ppb as required by catalyst adopted for downstream synthesis.
Conditioning section and methanol production
The conditioning section has the task of modifying the composition of the syngas produced by gasification, as within the range in which it varies, it is not suitable for methanol production. The requirements for methanol synthesis are: methanol module, MM = (H2 – CO)/(CO + CO2) equal to 2.1; CO2 /(CO + CO2) greater than 0.2 but less than 0.5; CO2 content less than 12%; H2O content less than 0.05%.
The syngas stream is separated, and only the minimum amount necessary undergoes conditioning treatment. This separation involves the need for more severe operations for the line being conditioned but ensures a reduction in the volumes of the necessary equipment. To increase the hydrogen content in the syngas, the first step of the conditioning section is a reactor where the shift reaction occurs. The added steam, 1.5 times the volume of dry syngas, is transformed into hydrogen, while CO is converted into CO2. CO2 is subsequently separated in a removal system with amines. At this point, the two separated syngas streams are reunited. To these two streams, a stream is added of almost pure hydrogen derived from the separation, through pressure swing adsorption (PSA), operated on the purge fraction necessary for the recirculation of the unreacted fraction to the synthesis reactor (see Fig. 2). The syngas now has a methanol module of 2.1 and meets the other requirements, except for the water content, which can be easily reduced to the desired value through condensation. The conditioned syngas is compressed to 80 bar and introduced into the synthesis reactor where it is converted into methanol. The unconverted fraction of the reacting gas, once separated, is recirculated into the synthesis reactor to increase the overall conversion. Due to the inerts that can accumulate, a purge fraction, mentioned above, must still be considered. Methanol is then purified to required grade and stored.
Application of methanol in the maritime sector
Methanol is increasingly being recognised as a viable alternative fuel for the maritime sector due to its environmental and economic benefits. As a clean-burning fuel, methanol significantly reduces emissions of sulfur oxides (SOx), nitrogen oxides (NOx), and particulate matter compared to conventional marine fuels. This makes it an attractive option for meeting the stringent emission regulations set by the International Maritime Organization (IMO). Additionally, methanol can be produced from renewable sources such as biomass, municipal waste, and carbon dioxide, further enhancing its sustainability profile. The use of methanol as a marine fuel also offers operational advantages, including ease of handling, storage, and transportation, as it is a liquid at ambient temperature and pressure. Several shipping companies have already begun to adopt methanol-powered vessels, demonstrating its feasibility and potential for widespread use in the industry. As the maritime sector continues to seek ways to reduce its environmental impact, methanol stands out as a promising solution for achieving cleaner and more sustainable shipping operations.
Methanol is a versatile and clean fuel that can be used in existing marine engines with some modifications, replacing bunker oil and fossil origin diesel. Additionally, methanol can also be used with fuel cells, offering an efficient alternative for maritime transport. This significantly reduces emissions of atmospheric pollutants. Indeed, maritime transport is a significant source of greenhouse gas emissions, contributing to air pollution and climate change. To address this challenge, the European Union introduced the Refuel Maritime directive, which came into force on January 1, 2025, setting ambitious decarbonisation targets for the maritime sector. The directive aims to reduce emissions by 6% by 2030 and 80% by 2050 compared to 2020 levels. It also mandates the use of advanced technologies and alternative fuels to achieve these goals (see Fig. 3).
Methanol is also safer to handle and transport compared to other alternative fuels. Methanol is liquid at room temperature and can be stored and transported with minimal modifications to existing liquid fuel infrastructures. This makes methanol a practical and convenient choice for the maritime sector, which can adopt this technology without having to invest in new costly infrastructures (e.g., the use of LNG, ammonia, or hydrogen).
Conclusions
The production of methanol from waste offers a groundbreaking solution for sustainable urban waste management. This innovative process not only reduces the amount of waste sent to landfills but also minimises environmental impact and greenhouse gas emissions. The methanol produced can serve as an alternative fuel for maritime transport, aiding in the sector’s decarbonisation efforts. Remarkably, converting urban waste into methanol can cut CO2 emissions by over 70% compared to traditional fossil fuels. This process breathes new life into the carbon and hydrogen found in waste, preventing them from contributing to landfill pollution. Economically, the feedstock becomes a revenue source rather than a cost, ensuring a high margin between production costs and the price of methanol from renewable sources. This guarantees a swift return on investment.
References