Sulphur 418 May-Jun 2025
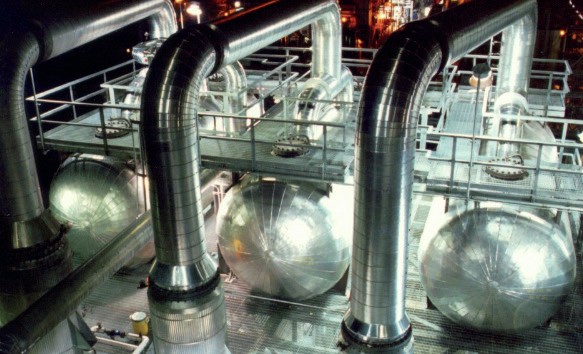
1 May 2025
The pros and cons of SRU extended downtime
SRU OPERATIONS
The pros and cons of SRU extended downtime
Reduction of sulphur loads in refineries with multiple sulphur train complexes often allows for one train to be put into an idle state for a prolonged period of time. Baylee Thompson of Wood presents the pros and cons of leaving a unit on hot-standby versus long-term idle taking into consideration reliability, safety, and operations responsibilities during extended downtime.
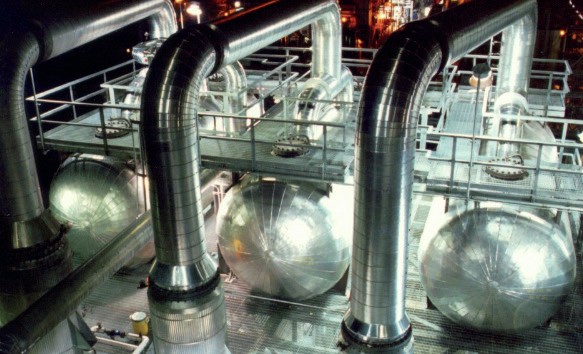
Many refineries throughout the world are experiencing changes in overall sulphur loads due to changes in crude slates and various economic and environmental considerations, creating instability in plant operation. For those sites, especially those with multiple sulphur recovery unit (SRU) trains, a lack of sulphur available to be processed by their units can be equally as difficult to manage as too much sulphur. In a low refinery sulphur case, there are three main options for managing the units: 1) co-firing at reduced acid gas rates across multiple trains, 2) hot-standby or firing exclusively on a utility gas stream, and 3) a long-term idle state. Understanding the pros and cons of each option is critical to making a decision on which run state is best when sulphur rates are below SRU turndown capability.
A co-fire or even hot-standby condition of the unit allows the plant to maintain a more typical run state. Fewer procedural changes are needed to maintain, and there is less overall deviation from the normal unit conditions. Hot-standby does, however, present a concern of waste of fuel gas, electricity, steam, and overall utility cost associated with keeping the units warm. There is also a potential risk of safety when operating the units in co-fire and hot-standby states for long periods of time, frequently operations is much more familiar with shorter time frames for both.
A long-term idle state refers to a planned outage of the unit for longer than that of a typical refinery turnaround. A long-term idle can eliminate the costly utility concerns associated with hot-standby or co-firing, as well as help stabilise online units that are still operational in a multiple SRU facility. Long-term idle still does, however, present its own unique challenges. If there are any plans to reuse the equipment in the future, including restarting the unit, these challenges are increased. Long-term idle with plans for equipment re-use will be the focus of the discussion in the following sections, highlighting considerations that need to be taken to safely and reliably plan for, execute and maintain, and restart the unit.
Even if refiners do not foresee the unit needing to be brought online, preserving the assets for use as spares or in other applications throughout the plant allows for a more integrated and sustainable path forward in response to the ever-changing economic demands and refinery processing priorities.
Prior to shutdown
Planning for a long-term idle of a unit should begin as soon as possible to allow for adequate preparations to be made. Facility planning should first determine if the remaining sulphur complex capacity is sufficient to sustainably run the expected sulphur rates produced by the refinery for the foreseeable future. The restart of an SRU after long-term idle should not be planned to be performed at a moment’s notice, or quick fashion. Once available capacity is confirmed the process of long-term idle can proceed.
Process evaluation
The process engineer should be the driver of long-term idle of the unit and oversee all aspects of the change including facilitating a management of change (MOC) procedure for any unit change. The MOC procedure is used to document and organise actions that will be taken on the idle SRU and is critical for plant safety.
First, the process engineer should begin by evaluating any unit pinch points and determining any work that should be performed while the unit is down or out of service. Where is the unit experiencing corrosion? Is there any routine maintenance coming up that should be performed? What work is planned for the next turnaround and how far away is the next turnaround? The initiation of a long-term idle will take a unit out of its conventional turnaround cycle and these factors should all be considered. It is recommended that any maintenance needed be performed upon shutdown of the unit. This allows for a quicker start-up in the event the unit is needed for refinery operational demands, while still allowing the mechanical integrity of the unit to be maintained.
In addition to mechanical turnaround considerations made for the long-term idle, catalyst should also be evaluated. The age and activity/performance of the catalyst should be evaluated using all available data to determine its health and speed of aging. What is the estimated run length between present day and required catalyst changeout date? Is the plant comfortable taking another shutdown of the unit after that duration or should the catalyst be changed upon shutting down? If the catalyst is changed upon shutdown, it should be communicated and coordinated with the catalyst vendor.
Lastly, the process engineer should compare the unit operating data to the heat and material balances or unit models as closely as possible, considering various unit monitoring points including an overall unit pressure survey. This can facilitate in identifying any “go do” or opportunistic changes that should be pursued during the shutdown.
Procedures and safety
New procedures for start-up, shutdown, and idle state must be created due to the differing needs of the plant during long-term idle.
Shutdown procedures should be written in conjunction with the SRU operators and allow for extended time to “drop out” or remove as much sulphur as possible from the unit and cool down at a very slow rate. Because this unit will not be in use after the shutdown, the motivations for speed are reduced and the additional time should be taken as available. Once this extended shutdown time is taken this is when the above detailed process evaluation should be referenced. Does the unit need to be prepped for entry or catalyst removal? If so, proceed accordingly based on site confined space entry and catalyst changeout procedures.
Once the unit maintenance and or catalyst changeout has been performed, the long-term unit idle shutdown procedure should continue. All liquids need to be thoroughly drained and dried out of the unit including amine, quench water, and all steam generating pieces of equipment. Passivation of the steam generating side of equipment should be strongly considered to maintain reliability. This prevents degradation of the metals and often a liquid level of passivation chemical is maintained inside of the vessel for the duration of the idle period. Recommended passivation chemical levels should be noted in the shutdown procedure and monitored by the board operator while prepping the unit for the idle period. The passivation chemicals themselves should be included in the safety data sheets of the unit as part of the MOC.
Refractory vendors should be consulted to understand if any special refractory considerations and/or procedures are needed for dry-out or for idling the unit for a long-term period.
If the existing tail gas catalyst is left in the unit, it is critical to ensure that no oxygen reaches the catalyst to prevent a exothermic reaction from occurring. In addition, overall oxygen in the unit should be minimised as much as possible to reduce potential for corrosion due to a humid, oxygen, and sulphur rich environment. As a mitigation step, it is recommended that the entirety of the process side of the unit, aside from the incinerator, be maintained under a nitrogen blanket for the duration of the idle period. The nitrogen blanket should be implemented at the acid gas battery limits and include a pressure regulator and pressure safety valve and continue throughout the unit. Once the unit is initially inventoried with nitrogen, it should require little makeup to maintain pressure and therefore is a minor expense to the site in utility cost. Proper signage must be installed in the unit and verification included as a step in the procedure to notify plant personnel of the presence of a nitrogen blanket in the unit.
An additional section to be added to the procedure should be the de-inventory of the unit steam tracing. All steam tracing should be isolated from the overall plant steam system and disconnected and drained at all available low points. Where the tracing has been disconnected should be recorded in the procedure documentation for reference at a later date when it is reassembled and when the unit is to be restarted. Depending on integrity and design pressure of overall tracing system, the site should consider “blowing down” or “sweeping” the tracing system with nitrogen to ensure any remaining water is removed. This is all in an effort to minimise potential for corrosion while the unit is down and also helps reduce steam leaks upon unit restart.
The sulphur pit, or sulphur storage system must also be taken into consideration in the long-term idle procedure and should warrant its own section. How high is the water table in the facility’s region? Is the storage system above or below grade? Is it water/air-tight? Will there be carbon steel exposed to air during the idle duration? These are all questions that should be asked and accounted for in how to safely idle the sulphur storage system of the unit.
In addition to these special considerations for shutdown, main tenants of the site’s typical shutdown procedure should still be followed. Proper isolation and blinding of lines, locking and tagging out any necessary equipment in the unit, proper barriers and notification to overall plant personnel that a shutdown is ongoing.
Operations
Training to inform operations to all updated and new procedures for the shutdown, long-term idle, and startup states of the unit must occur prior to shutting down the unit. It is critical to the safety and effectiveness of the idle that all operations personnel are properly trained on this abnormal unit state.
This training should include not only a deep understanding of procedural changes but also the changes necessary for the dayto-day roles of operations while the unit is on long-term idle. What monitoring points will need to change from current operator rounds? What will stay the same? Do new/ temporary alarms need to be associated with this change to be monitored by board operators? How many operators need to be in the unit and does this differ from current staffing needs?
Any changes to operator requirements or databases, alarms, or even control room/distributed control system (DCS) board visuals and graphics should be included in the MOC to allow them to be reverted to their original state on restart of the unit.
Analyser vendors should be consulted to determine whether all analysers should be pulled out of service and stored for the duration of the downtime.
During shutdown
While the unit is shut down or during long-term idle, the SRU should not be treated as an “offline” piece of equipment. It is critical to the longevity of the equipment and the ability to re-use the equipment either as spare parts or restarted as a full unit, that the system is continually monitored.
Once the unit is down, it is critical to double-check all DCS or control room screens and alarm points to ensure nuisance alarms are not clouding board operator judgement. This will enable the board operators to better monitor the unit to ensure it stays under nitrogen blanketing, free of air in the process section, and passivation chemical levels maintained during this idle period.
Equipment, piping, and steam tracing inspection frequency should be maintained to verify no degradation of mechanical integrity is occurring during the downtime.
One approach to managing the unit downtime is a temporary MOC to implement and document all changes. Upon start-up the temporary MOC can then be reverted to its prior state and will allow for the undoing of all of the changes in the MOC in a stepwise approach.
Restarting the unit
Restart procedures should be defined prior to the unit ever being put into an idle state as additional care should be taken to ensure the unit is in a safe state to restart properly. Has all of the maintenance that needed to be performed completed? Is everything returned to a normal state? Check with the safety group, are all MOCs that were opened during the downtime now complete?
Starting with the MOC as a guide you should methodically return the unit back to a normal state after inspections have been performed to determine if this is feasible. Before ever removing any process blinds from the unit, all passivation chemicals from steam generating equipment should be drained, steam tracing should be reassembled and verified as working for each circuit throughout the unit.
Does the catalyst in the tail gas reactor need to be activated or sulphided? Do operators need to be retrained? Are all car seals still in place as needed? Is the sulphur pit or tank free of water? Have PSVs been checked and tested as needed, is the temporary PSV removed? Have any parts been taken from the idle unit while down? Has a thorough walkdown and pre-start-up safety review (PSSR) been performed?
Once all changes to the unit for the long-term idle have been addressed and returned to “normal” or pre-idle state the site can then proceed with a more typical restart procedure. This includes but is not limited to pressure testing the unit, catalyst dust blow, verifying bolt tightness throughout the unit, and evacuating all non-essential personnel from the unit prior to re-light.
It is crucial that this restart is not completed in haste. As the unit has likely been down for an extended period of time a thorough inspection should be performed to verify everything is as intended for the internals of all vessels. Normal pipe inspections for corrosion should be performed. A slow heat-up should be pursued to prevent the risk of thermal shock.
Conclusion
Ultimately the choice for long-term idle is not right for every facility or every situation. The pros and cons should be evaluated with great care to understand the impacts to the site and its personnel. This includes weighing the feasibility of a hot-standby or co-fire state and comparing to the long-term idle option. Outside guidance from a technical expert and the benefit of a new set of eyes is always recommended when undertaking a change such as this. The safety of the facility hinges on the detail and care taken when making this decision and that should always be at the forefront.