Nitrogen+Syngas 366 Jul-Aug 2020
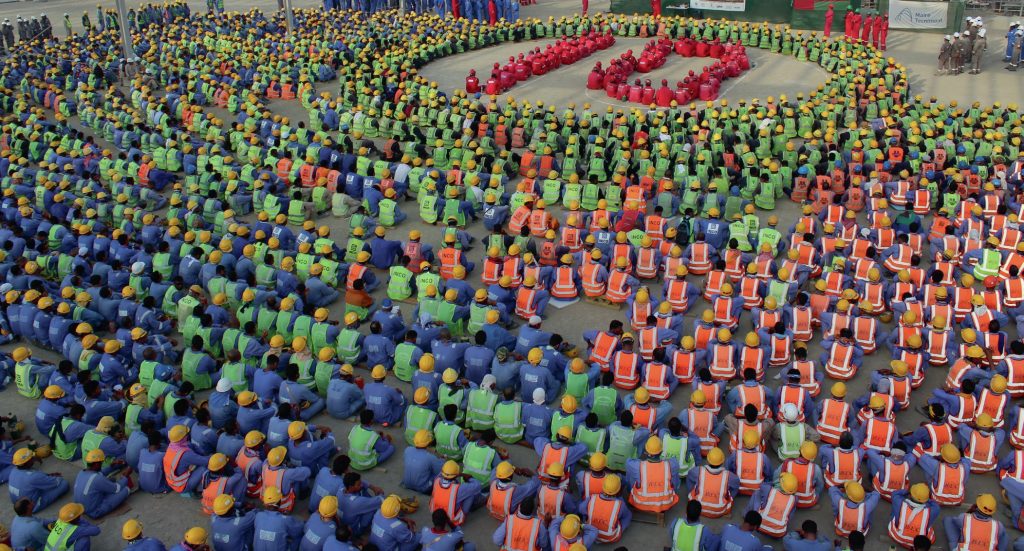
31 July 2020
Making construction sites safer
HEALTH AND SAFETY
Making construction sites safer
Nitrogen+Syngas asked some of the industry’s leading EPC companies what they are doing to make construction sites safer around the world in pursuit of the goal for zero incident safety performance. Read on to find out what approaches have been taken by Maire Tecnimont Group, thyssenkrupp, Toyo Engineering Corporation and Saipem.
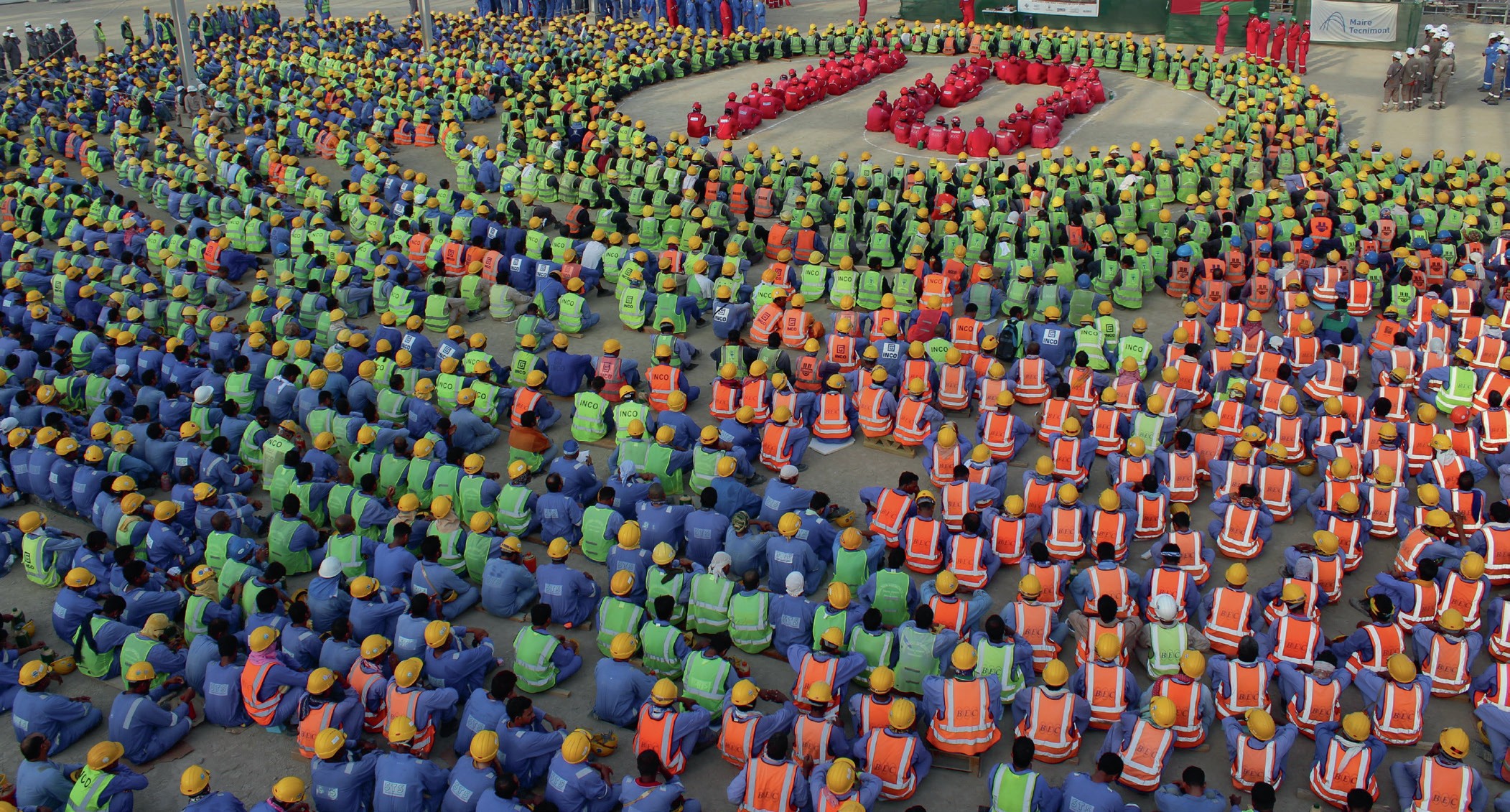
MAIRE TECNIMONT GROUP
An HSE driven culture
Safety, a fundamental corporate value for those working with Maire Tecnimont Group, pursues a precise objective: to prevent accidents and mitigate the impacts on the ecosystem, with the commitment to provide workplaces, services and industrial plants in compliance with legal requirements and at the highest standards of Health Safety and Environment (HSE) protection. The Group model promotes working in safety, the protection of the environment and the well-being of people, for each operating area of the company and during all phases of project execution, both in the offices and out on the 30 construction sites currently active globally.
The monitoring and improvement of the HSE Management System along with a preventative approach allows Maire Tecnimont to confirm its commitment in excellence of injuries prevention. The five-year rolling average (2013-2019) of the Lost Time Injury Frequency (LTIF) index, according to the International Association of Oil & Gas Producers
(IOGP), shows that the Group’s performance indicator was consistently lower than the IOGP benchmarks. Maire Tecnimont Group also develops employees’ professional competences and skills as well as incident prevention training as a core strategic activity. In this regard, in 2019 alone approximately 2.6 million training hours on HSE topics were provided to employees as well as to the sub-contractors involved in the execution of projects.
Over the last three years (2017-2019), a total of more than 349 million man-hours were worked at the Group home offices and on its construction sites worldwide, out of which approximately 326 million man-hours were on sites. A record peak was registered in 2018, with more than 140 million hours worked counting both home office and sites. The fluctuation of man-hours over the years is due to the fact that many projects in the construction peak phase in 2018 were followed by the closing phase in 2019. As for records, Maire Tecnimont can boost a significant achievement on a single megaproject: 100 million safe man-hours worked were successfully reached at ADNOC’s Habshan 5 gas treatment plant site in Abu Dhabi, UAE. A record-breaking achievement with no precedents at that moment in the hydrocarbons plant engineering EPC industry.
As one of the major results of the commitment to further improving an already well rooted HSE culture, Maire Tecnimont Group recently acquired the multi-site certification according to the OHSAS 18001: 2007 and ISO 14001: 2015 standards, from Bureau Veritas Italia. This important certification enhances the synergies between companies, standardising procedures and methods, optimising audit times, thus increasing the competitiveness on the market of both individual entities and the entire Group. In a nutshell, it is a new approach to certifications, resulting in an important lever to integrate companies operating in different territories and social areas. This important milestone was reached for the Group’s main companies working across very different areas, from Italy’s offices to those in Russia and India, and for all of its construction sites around the world. It was a three-year challenging project, for a network of companies and construction sites spread across 45 countries, and eight time zones.
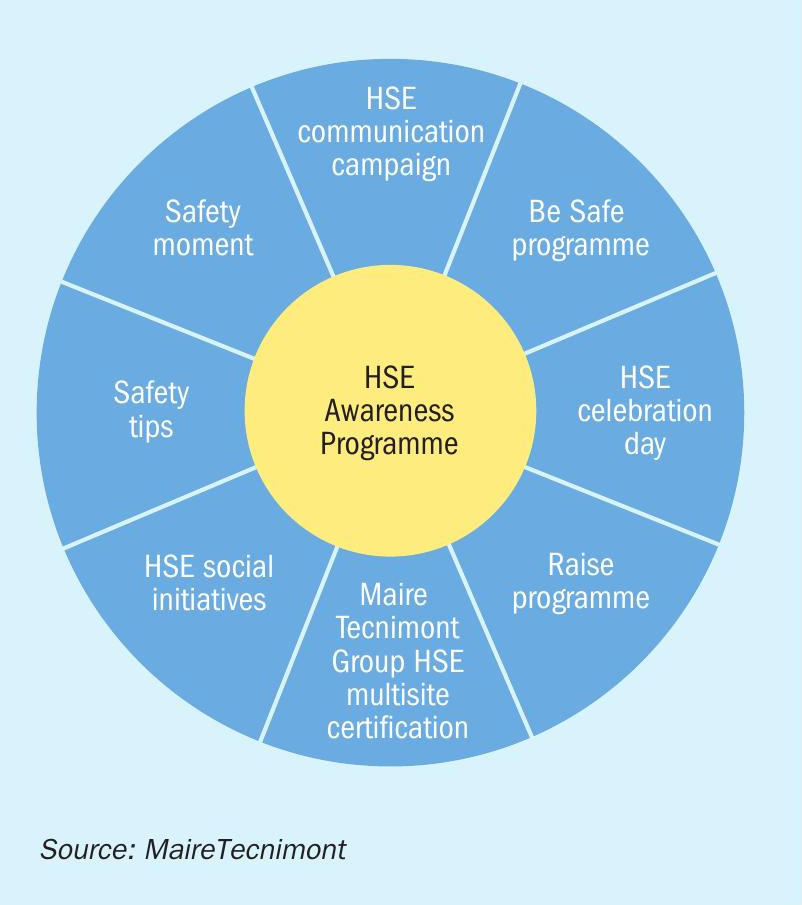
The Safethink campaign
The Group’s zero incident target approach was recently developed in a four-step communication campaign: Safethink. A brand-new proprietary logo was born, together with a wide set of communication tools in order to both make everyone increasingly aware of “actively thinking about safety” before acting, and to maximise Maire Tecnimont’s HSE culture. The actions required involvement from both home offices and sites, as the campaign was developed on four different areas, each focusing on its own workshop and training sessions on different aspects of safety embedded in everyday working life: tools, behaviour, and the rest still to be unveiled.
With Safethink the aim is to express in a concept the basis for every single action taken, to actively think about safety and reinforcing the shared HSE identity: the safety and protection of people is not only a priority but a fundamental value in every activity and step we take on a daily basis. These messages were highlighted and further developed in Maire Tecnimont’s corporate magazine Evolve, an ideal dissemination tool to further spread the importance of maximising each and everyone’s HSE attitude within the Group. Involvement and participation were already visibly present during the launch event of the “first leg” of Safethink, held in July 2019 at the Milan headquarters, which was enriched by several testimonies and best practices registered both in home offices and on sites.
Furthermore, a dedicated Safethink digital platform was established to keep tight focus on these topics. In this way, the HSE team is capable of disseminating all campaign material to all of the different company sites and, above all, directly to the construction sites: offline tools, branded site equipment combined with digital ones, such as “Safety tips”(above, right) on how to make each daily activity safer and the most updated communications on the new initiative helped to boost awareness among task forces, and at the same time provided a strong common identity driver, shared with everyone. Every worker who chooses to use these tools becomes a spokesperson for the wellness and safety of the Maire Tecnimont Group, while also being a distinctive element showing customers that the “HSE branding” operation has already proven extraordinary results.
As part of the campaign, training has played an essential role to create stakeholder value, develop employees’ professional skills, prevent accidents and improve health, safety and environmental awareness. This resulted in devoting several million hours to courses, spread throughout all the value chain, including subcontractors. In addition to the classroom training for all workers, the Training Lab was also conceived as a best practice hub, performing theoretical and practical training dedicated to special hazards (e.g. work at height) carried out by subcontractors. The adoption of these practices is aimed at increasing all workers’ risk perception.
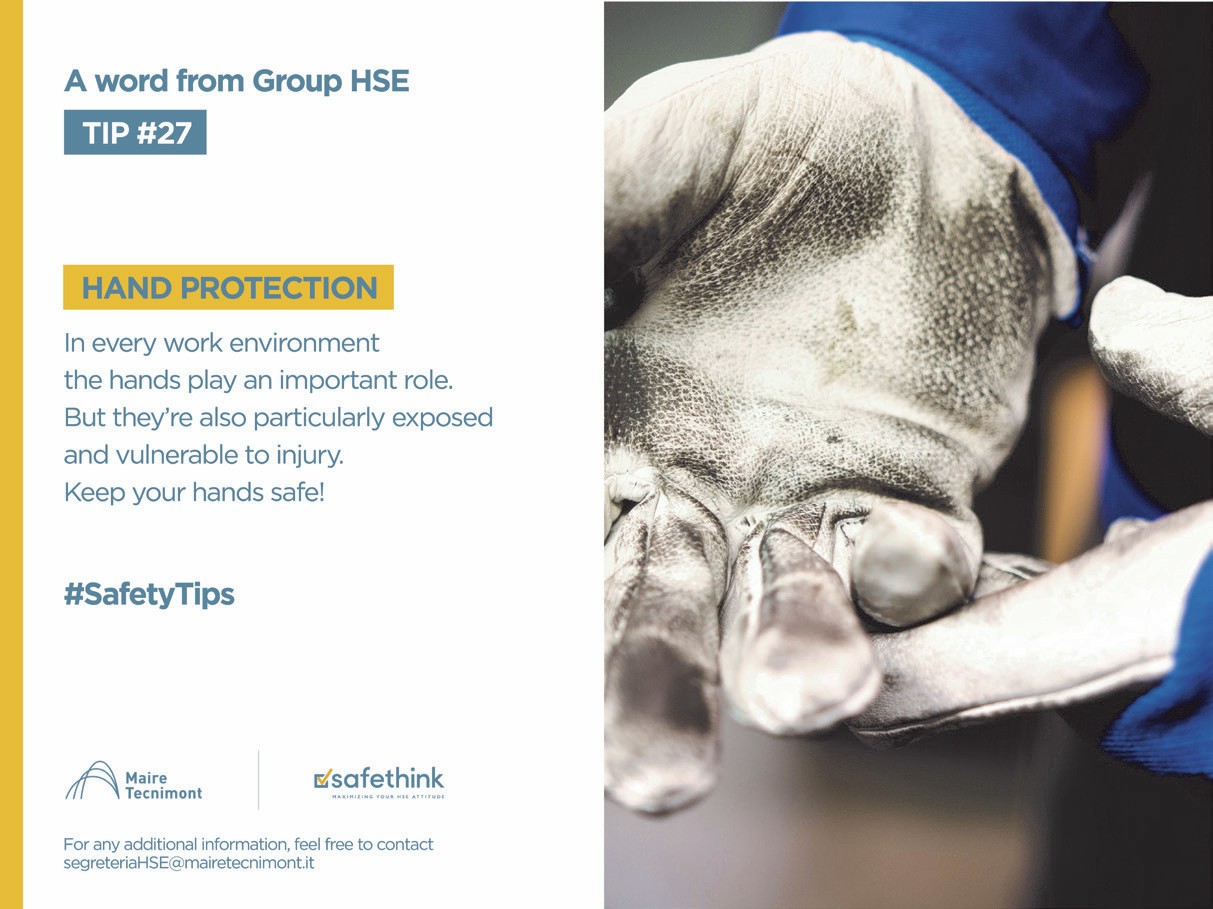
During the second HSE communication campaign focused on behaviour, the “Safethink Rules for Life” project was launched in all operating sites. The campaign consists of a selection of ten safety rules that the Group considers of primary importance for the prevention of accidents. The rules were not just taken from those defined by IOGP, they have been customised to reflect Maire Tecnimont’s context and ad hoc pictograms have been created to emphasise the distinctiveness of the Group safety culture.
Safethinkcovid-19
In response to the spread of coronavirus Covid-19, Maire Tecnimont immediately committed itself to ensuring that all work activities in offices and on sites are carried out in compliance with the maximum health and safety standards. The clear priority was to ensure the health and safety of its employees and collaborators and their families, while guaranteeing the continuity of the business in the countries where it operates.
Maire tecnimont’s teams on construction sites immediately demonstrated a proactive approach and the ability to manage all aspects right from the initial phase of the crisis, taking, when necessary, autonomous initiatives applied and tailored according to the latest advice coming from the WHO and other medical organisations. They have been managing the situation while also educating the subcontractors in coordination with clients for the adoption of protocols to protect workers and personnel involved in the projects.
Furthermore, a HSE Crisis Coordination Team was set up in order to coordinate the actions to be taken in the countries where the Group is present and to issue guidelines defining the behaviour to be followed by all of the workforce. Starting in February, for example, a set of Covid-related safety and remote-working policies was defined and implemented, to keep staff and workers safe. Maire Tecnimont was able to rapidly virtualise several processes and working activities, thanks to significant investments made in smart working technologies and training in the last four years.
Transport and shared spaces have been swiftly reorganised, meeting the new dynamics of smart working in sites (where activities allowed this to happen) and offices. That said, introducing and implementing all the steps in such a challenging atmosphere where people from many countries and nationalities are working together was not an easy job, particularly as this action needs to be carried out on each operating site.
In the context of a global health emergency, correct information is essential to manage the risks and to face an ever changing situation effectively. Therefore, a structured communication campaign covering all aspects of the pandemic emergency and the correct measures to be taken to conduct daily activities both in the home office and on site was promptly implemented. On an operating level, the main procedures implemented were temperature control, provision of face masks, hand sanitisers and gloves in work environments, social distancing, and ensuring exceptional attention to the health and safety of local communities. At the same time, the spin-off of the Safethink brand, “Safethinkcovid-19” was rapidly conceived and used as the new HSE brand to apply the already well-known safety campaign to the urgent situation. This clearly helped boosting involvement of all colleagues and provided sound evidence of the Management’s commitment to tackling the pandemic proactively.
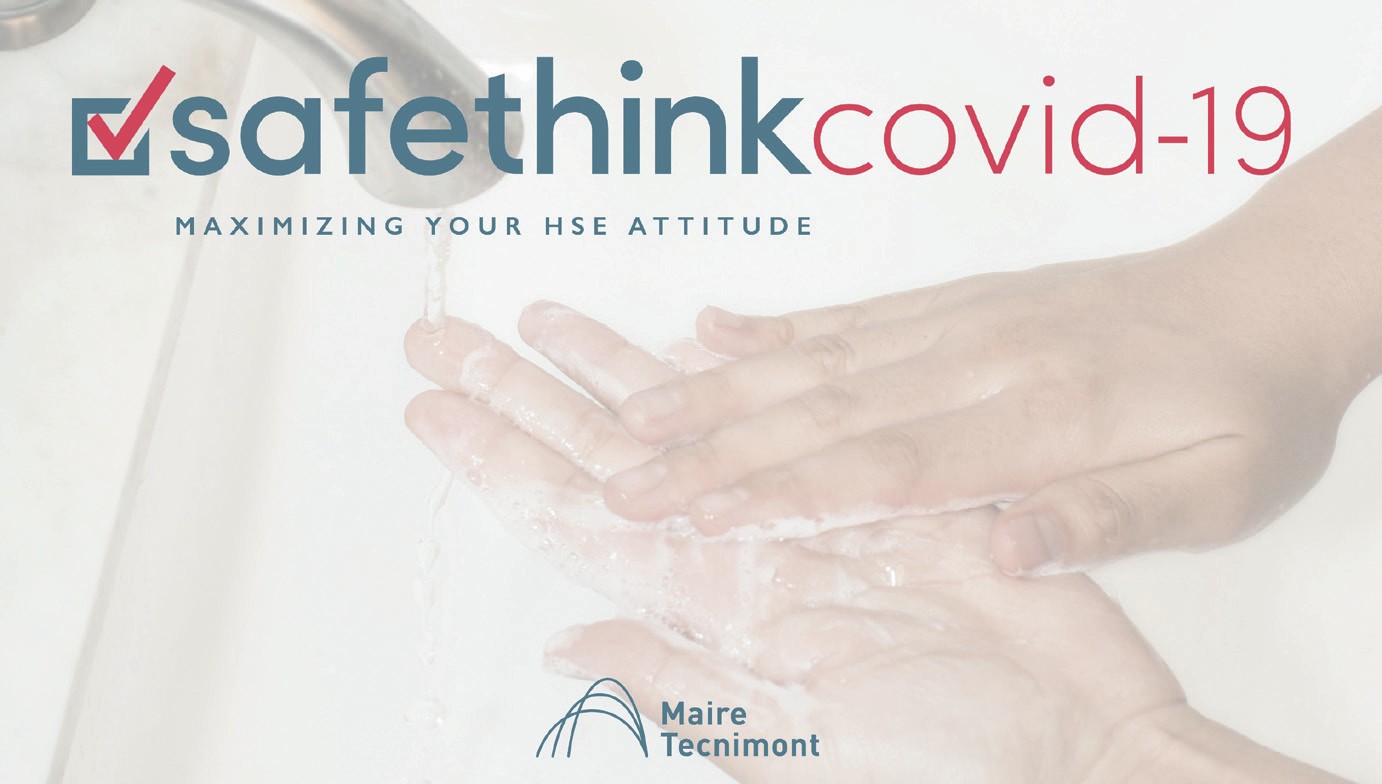
A dedicated digital channel was created to provide daily communication and useful information relating to the Covid-19 emergency, where every colleague can find all the communication from the relevant focal points, a complete list of documents about policies and proper behaviour to be adopted by all of the workforce, together with the latest heath information documents provided by the competent authorities. Finally, insights on how to make each daily activity safer are continuously spread to all offices and sites through the well-known channel of “Safety tips”. In this way, colleagues working in remote regions were able to feel closer to their base, by remotely getting the most up to date support. This central hub is constantly monitoring the information concerning Covid-19, taking preventative measures and all necessary actions.
Specific rules and guidelines were set to provide instruction and define preventative and control measures to be implemented in all Maire Tecnimont Group Construction working sites, including joint ventures, in order to minimise and reduce the risk of exposure to Covid-19 and to update site emergency procedures. This is reinforced by identifying a Maire Tecnimont Site Focal Point, tasked with issuing a recurrent detailed update on the site’s workforce. After completing a training course provided by the Group’s Headquarters, each focal point is required to swiftly align with all subcontractor project managers and HSE managers to jointly implement the MT Group Action plan. Subcontractors are also required to appoint a company focal point, to ensure that measures were observed throughout the entire project execution chain.
On April 29th Maire Tecnimont held a two-day workshop bringing together 20 construction sites totaling about 33,500 people, including Maire Tecnimont’s construction team and direct and indirect workers, across eight time zones from North America, Europe, Africa, Middle East and Russia to South East Asia. The Group decided to organise this sharing event to mark the World Day for Safety and Health at Work 2020, sponsored by the International Labour Organisation, and at the same time to remind every construction team of the great challenge of the Covid-19 emergency – to maintain production and operational efficiency, in full compliance with the Health, Safety and Environment regulations.
During the two-day workshop, Maire Tecnimont’s top management connected with HSE site managers as well as the teams involved in the daily operations for project implementation, in order to share best practices on how staff at each site, despite the distinct circumstances of its often very remote location, were carrying out its normal daily activities, facing the current global emergency proactively and with a strong spirit of adaptation. Colleagues traded thoughts about their experience, after construction teams demonstrated the ability to absorb shocks and respond not only promptly to a constantly evolving situation, but to actively contribute with real solutions.
Closing the workshop, Maire Tecnimont CEO Pierroberto Folgiero commented: “For us the priority is to ensure the health and safety of all colleagues and their families, while we maintain full operational continuity in the four continents in which we operate, from the United States to Malaysia. In recent years, our Group has made the HSE component a clear factor of competitiveness, and today we are further demonstrating that this is not rhetoric, but a tangible value helping us face the challenges that await us in the future – together with the passion that has always distinguished us.”
Successful project delivery during the pandemic
In such a time of extreme life conditions, people’s value of collaboration, discipline and engagement have been clearly more evident than in other circumstances. Not only that, but really encouraging signs of resilience have been witnessed, coming from different project teams and parts of the world, all under the same flag: keeping up the good work, notwithstanding the challenging times we are living in. Here are some examples:
When Covid-19 broke out in Egypt, at the beginning of March, the team at the Kima Fertilizer Complex in the remote area of Aswan was preparing for a nine-day performance test ahead of a May start for ammonia production. KIMA is a joint project of two sister companies within the Maire Tecnimont Group: Tecnimont as EPC contractor and Stamicarbon as urea technology licensor.
The team faced a really hard choice, whether to complete the test in a very limited amount of time, pushing forward, working in difficult conditions as the emergency was on the verge of spiking in the country, not knowing when they would have been able to come back to their families. Meanwhile, the International airport was shut down. But leaving would have resulted in the postponement of a long-awaited performance test, placing the plant and its assets at risk.
The first order of business was to brainstorm to provide a detailed risk analysis and to identify working solutions over and above the standard safety recommendation. Once identified, they were immediately implemented. The team decided to stay on-site to achieve the long-targeted goal, which was successfully completed with the performance test on March 22, demonstrating performance better than the guaranteed, as the plant ran fully operational far above its nameplate capacity.
The real commitment and great resilience, put in place by people during the Covid-19 pandemic, resulted in outstanding achievements in terms of safety milestones reached in different countries in lockdown. Among the main milestones was the Liwa Plastics Complex–EPC2 Project in Oman, the first producer of polyethylene in the country, reached 40 million safe man-hours thanks to the effort of all relevant parties involved in the project.
Different nationalities, different languages but with a common Safethink target.
THYSSENKRUPP INDUSTRIAL SOLUTIONS
Safety starts in the mind
In recent years, there has been a growing awareness of the importance of Occupational Safety and Health (OSH) around the world. If a construction project is completed safely, not only is it good for a company’s reputation and reflects positively on their concern for their employees, but it’s also good for their bottom line: the fewer lost time incidents (LTIs) there are, the quicker a construction project will be finished.
Safety is always a top priority for thyssenkrupp Industrial Solutions, not only for its employees but for all sub-contractors working with them too. With ongoing construction mega projects in different regions, there are many people on site everyday who come from different regions, with different cultures and safety backgrounds. They are coming into contact with moving machinery, working at height or in confined spaces, lifting heavy materials and handling electrical tools, all whilst wearing personal protective equipment.
Zero accidents goal
thyssenkrupp Industrial Solutions is coming closer to the goal of zero accidents at work by focusing on three pillars of OSH: internal safety management systems, monitoring of activities, and measures to heighten safety awareness levels amongst its own employees and contracted personnel. State-of-the-art OSH management systems help to minimise the risk of accidents at work.
Strict, regular monitoring of procedures and systems helps thyssenkrupp Industrial Solutions to evaluate how well they are working. Yet all that would be ineffective if people did not behave correctly. So a key focus of the OSH teams’ work is on behaviour: enhancing safety awareness levels; changing perceptions of safety for the better; promoting relevant soft skills; and ensuring everybody speaks the same safety language.
Focus on behaviour
No matter how strong OSH management is, there is always one unpredictabl e component: human behaviour. In real life, around 90% of accidents are triggered by unsafe behaviour. That is why thyssenkrupp Industrial Solutions has developed a Behavioural Based Safety (BBS) program to positively influence safety-related behaviour. The BBS program focuses on four main pillars: pinpointing desired behaviour through means such as management staff leading by example, and pinpointing undesired behaviour by means of mandatory procedures and regulations; measuring progress using predetermined criteria that record behaviour, detect gains and recommend room for improvement; feedback involving everyone acting responsibly towards coworkers, intervening to stop unsafe actions, and discussing the potential risks; heightening awareness of the consequences to avoid negative ones and encourage positive ones.
OSH e-learning module
One of the challenges for a company that operates globally like thyssenkrupp Industrial Solutions is communicating key OSH messages to the entire workforce in a wide variety of industries worldwide. An e-learning module developed collaboratively by teams from OSH and Construction went online at the end of May 2017 and uses state-of-the-art learning techniques to solve this problem. Within an hour, all employees who visit or work at construction sites – everyone from new recruits to top management – can learn all about their roles and responsibilities in OSH, what procedures and tools exist, how incidents should be reported, where the main hazards lie, and how BBS works in practice. And they can do that at any time and in any place worldwide. One highlight of the module is a new assessment tool that makes use of cartoon pictures to help the e-learner spot unsafe behaviour at a construction site.
The BBS program and OSH module are helping to raise safety awareness and achieving the zero accident goal – with all the associated benefits for both the company and its customers, as well as the families and friends who look forward to their loved ones coming home from work safe and sound.
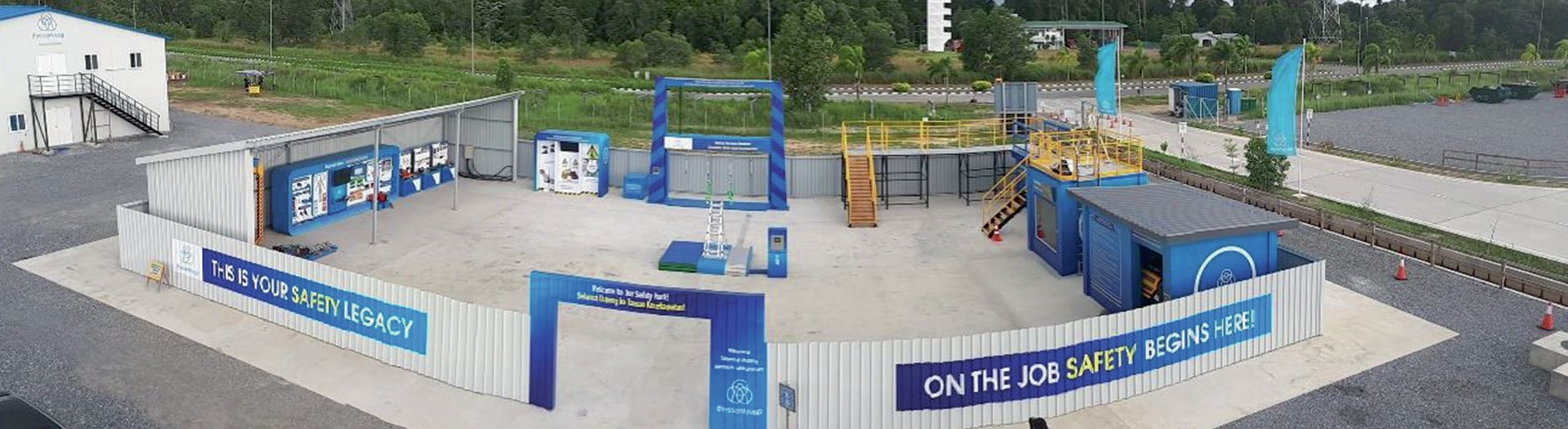
Safety Park
In order to train and educate all workers properly how to work safely, thyssenkrupp Industrial Solutions decided to invest more in training by adopting the Safety Park training concept as part of their site safety induction training programme. The induction programme includes both theoretical and practical elements that take place at the Safety Park.
thyssenkrupp Industrial Solutions started with implementation of the concept in two mega plants located in Brunei and Hungary.
All personnel related to a project are required to go through full safety training (induction training) before they start work on site. The Safety Park takes a unique format in that all personnel engage in simulations reflecting real life hazardous situations and conditions, where they can experience the risk and feel the consequences. In this way, they learn how to avoid these circumstances in an interactive, hands-on way, removing language barriers in the process. Feedback from workers and staff has been really positive; everyone is enjoying the experience and the safety message is remembered and understood.
The Safety Park at construction site covers many modules, each focusing on a different construction safety aspect: crushed by machinery safety simulator, confined space training, handrail and scaffolding collapse simulator, safety harness simulator, safety helmet/boots impact simulator, electrical safety simulator, hoist crane experience, A-type ladder experience and other modules. All simulations are conducted with the utmost care and are carried out under the watchful eye of fully trained health and safety personnel.
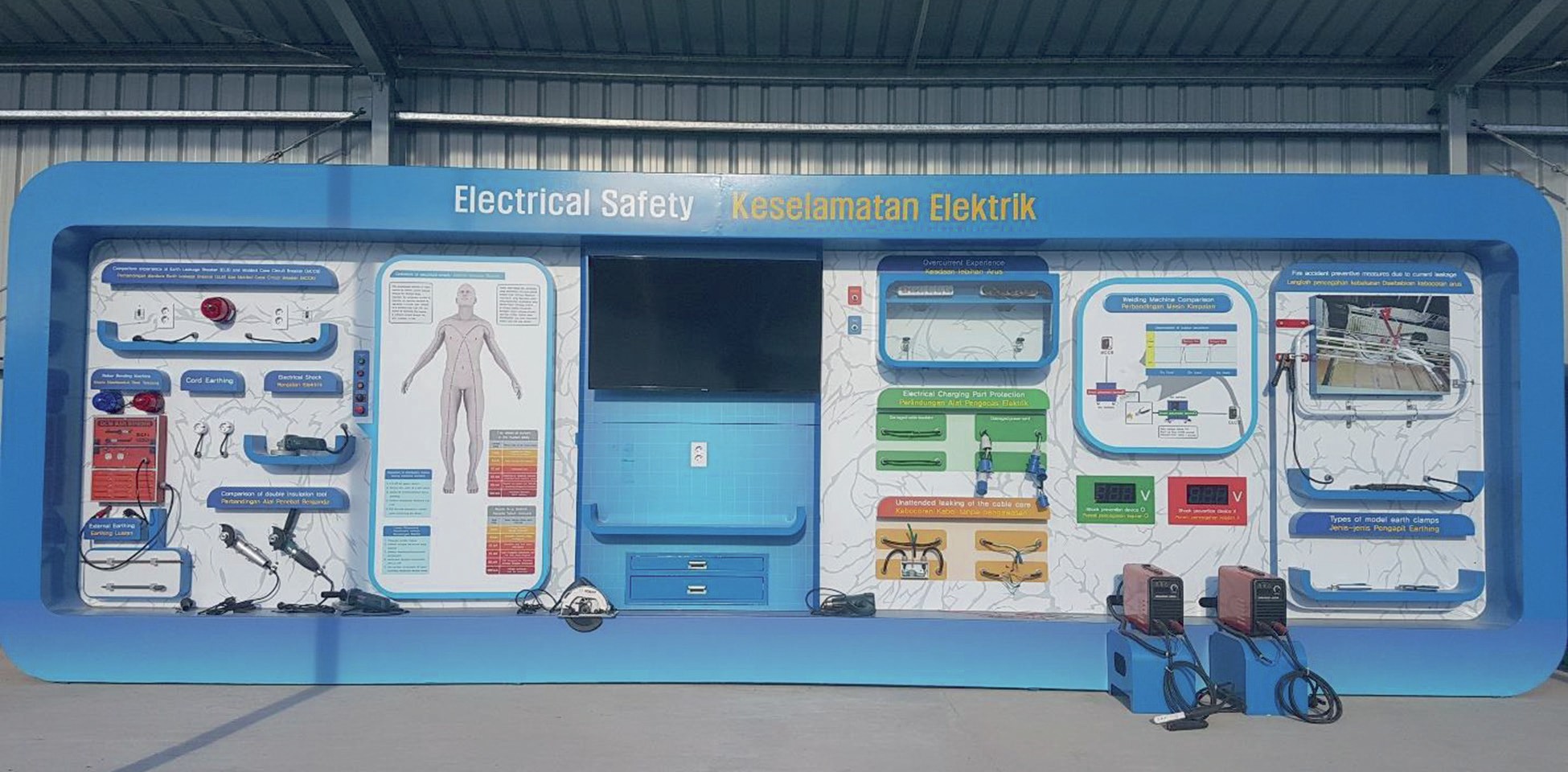
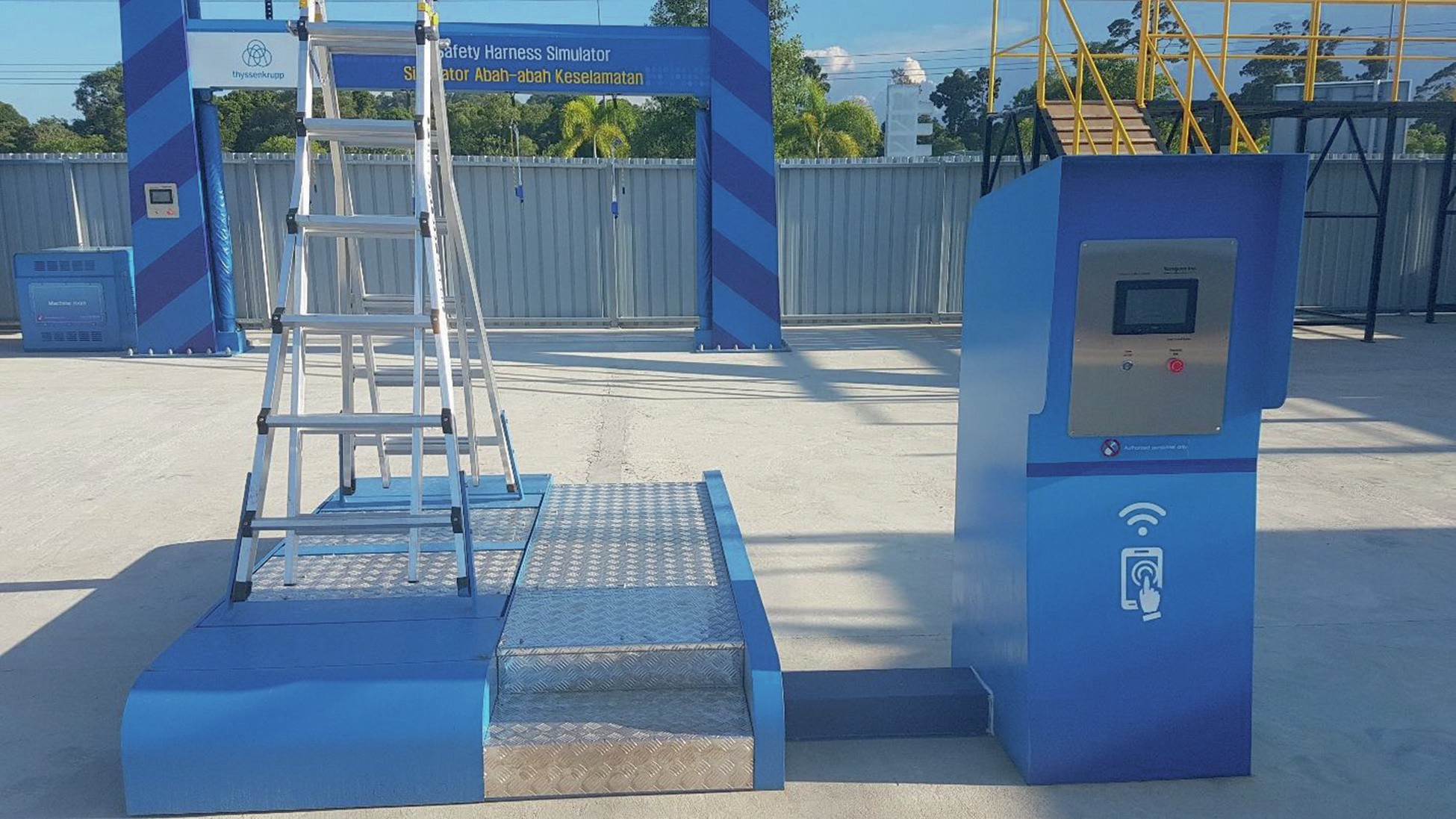
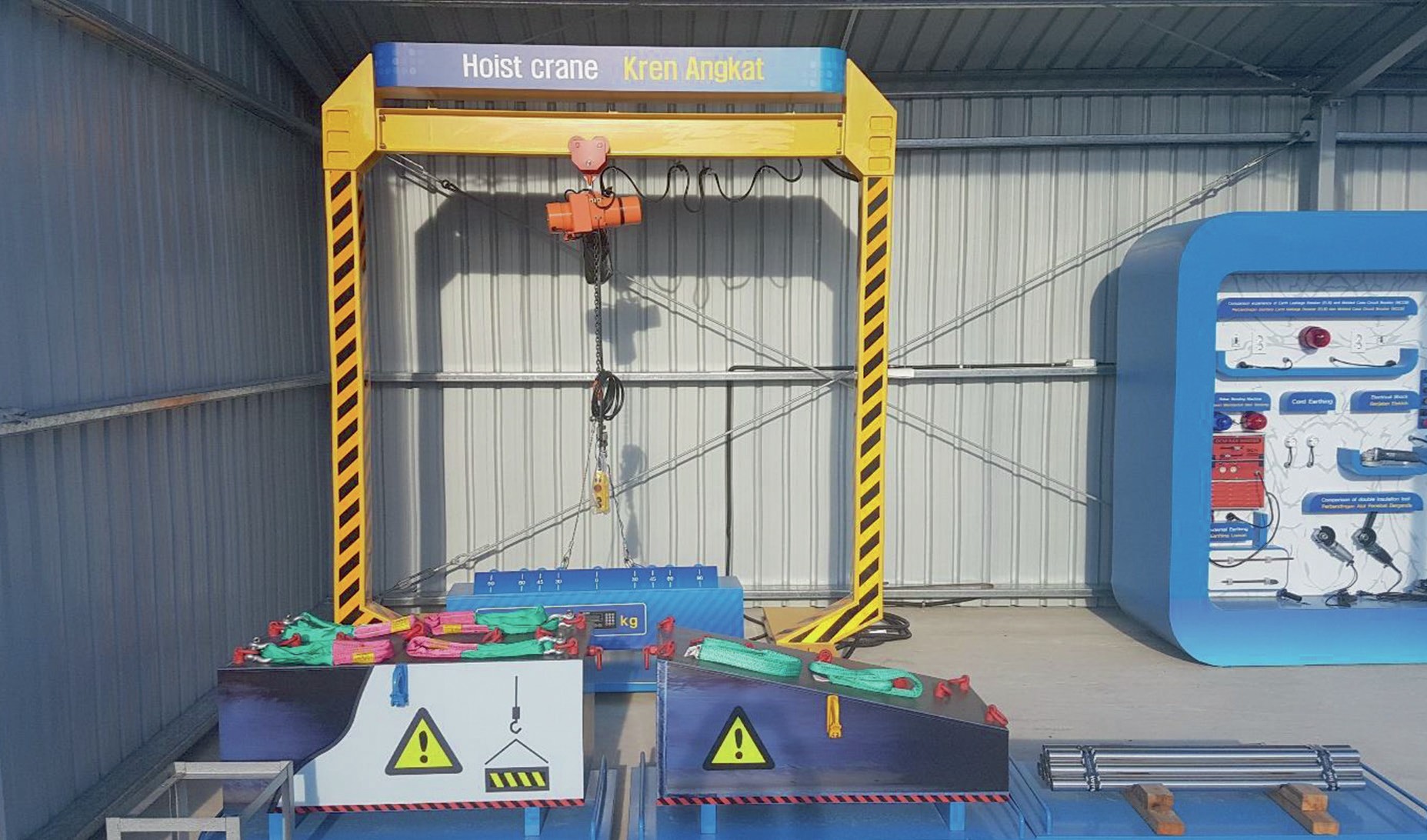
SAIPEM
Building a strong HSE management system
Making a construction site safer is not a matter of a single solution, but rather, like a very good cocktail, it is made by an effective and scientifically tested mix of various ingredients. With this view, to achieve the zero incident goal it is necessary to build a strong HSE management system commencing from planning and continuing through to the review phase, to properly assess all risks, eliminate those that are avoidable, implement the necessary control and prevention measures and to openly check if they have been effective or identify if further actions are necessary.
All of these concepts have been deeply embedded in the reference international ISO Standards for many years, so why are they not enough to reduce accidents to zero? In Saipem’s experience there are some factors that are particularly important. The competencies and training efficacy, the capability of the organisation to collect and analyse data, a strong management system, preparedness in case of foreseen and unforeseen situations and, the safety culture of both the organisation and of the clients and subcontractors in the country in which the activity is performed appear to have the greatest impact on the ability to achieve the zero accidents goal.
Digging deeper into the aspect of training and competency, it is well known that due to communication and technical issues, providing effective training is not an easy task. However, past experience has demonstrated that offering trainers a dedicated ‘train the trainer’ (TTT) pathway and the provision of comprehensible and standardised materials in multiple languages that use a modern graphical approach has been effective.
Closing the gap related to competencies presents a greater challenge. This is attributed to the fact that technical, HSE and soft skills are different within different roles. It is only through a strong Competence Assessment and Assurance Program that begins at the hiring phase and continues through the entire working life of an individual that it can be assured that the right person has been assigned for each job and in doing so increase the level of safety of worksites.
While the issue of data collection and analysis could appear to be a trivial issue, Saipem has made significant investment in resources to strengthen its systems. Borrowing from a motto that is familiar in the world of finance – ‘cash is king’, Saipem recognises that ‘data is king’ and must be effectively collected, managed and analysed to identify any opportunities or weaknesses in the business. Through the examination of past data, incidents investigations, audits, inspection hazard observation cards, training trends and completeness, competency assessment results etc. Saipem is able to quickly and efficiently identify where the company must address its efforts and anticipate undesired events.
It is important to embrace the digital transformation to enhance systems and explore all innovative solutions that are already available in the industry as well as others, e.g. RFID, anti-collision systems, smart cameras, tags etc. These systems can of course present a substantial financial investment so it is imperative that contractors have strong, supportive, and sharing relationships with their clients as it is they who can be the real driver to effect this change.
HSE management systems, relevant procedures, definition of roles and responsibility etc. is perceived within many organisations as being unnecessarily bureaucratic. However, if these elements are properly structured and written they form the foundations of effective safety management in any activity. It is of paramount importance to set out what must be done and who is responsible so that these systems can be continuously optimised through application of the system itself.
The current Covid-19 pandemic presents an excellent example of the need to be prepared for both foreseen and unforeseen events. Saipem has a complete and robust set of procedures that allow it to effectively manage a crisis such as this one, yet which is also flexible enough to enable it to respond to other types of crisis without affecting its ability to act and react. Undertaking drills and exercises that test the efficacy of these systems is vital to ensure that to ensure that Saipem is ready and able to respond efficiently to these situations.
Industry has and continues to make numerous steps forward to ensure safety at work, drastically reducing the number of accidents that occur. However, due to the human factor, studies show a constant value – a “safety plateau”, that seems impossible to reduce. It is therefore the culture, the behaviour and habits that are consolidated in the workplace that must be changed if the goal of zero accidents is to be achieved. It is unlikely that the systems and controls mentioned here will be implemented effectively unless they are supported by a clear vision, shared and adopted by every employee to achieve the ultimate goal of zero accidents.
But how do we arrive at a strong culture where the number one priority of everybody within an organisation is aligned with the same values and ethics in relation to safety? Robust safety cultures do not just emerge by accident! They require strong, visible leadership from those in positions of influence who demonstrate a relentless dedication to shaping the ideas, behaviours and actions of the people who operate within an organisation.
Sadly, sometimes business leaders lead with the success of their business as their primary and indeed their only focus, possibly to the detriment of safety, even though the two concepts are not mutually exclusive. Companies that possess a strong culture of safety are not only safer, they also perform financially more effectively. Businesses that understand, adopt, and internalise these ideals recognise that there really is no conflict between safety and efficiency. This concept has been fundamental for Saipem and it is embedded in the organisational health and safety vision. A “leadership in health & safety” strategy is highly recommended to be implemented in any organisation willing to shape a stronger safety culture and reach a zero accidents target. For this reason, in 2010 Saipem created the LHS (Leadership in Health & Safety) Foundation, a not-for-profit organisation, with the mission to help both industry and society in the attempt to raise the levels of safety culture, through leadership and unconventional communication media.
In conclusion, returning to the opening comment, to create a good cocktail requires quality ingredients, knowledge of the quantities that need to be mixed and how to incorporate them together, a dash of creativity and, in the case of achieving zero accidents, a lot of love for safety!
TOYO ENGINEERING CORPORATION (TOYO)
Improving safety with digital technology
The big wave of digital transformation that is spreading rapidly worldwide is also affecting construction sites in the EPC contracting industry and a digital technology approach to safety is also expected. Some of the ways in which TOYO is embracing this new approach are highlighted below:
- smartphone;
- digital signage;
- AI speaker.
Smartphone
TOYO has been working continuously to apply Health Safety Security and Environment (HSSE) efficiently for TOYO’s workers at construction sites. The standard HSSE procedure was developed based on past knowledge and experiences, but the procedure was based on a traditional paper based route. A new paperless procedure was needed for the future.
TOYO’s first response was to use Microsoft Power Apps, a standard tool for creating new applications that could be used easily without any special skills to develop a paperless solution. This can facilitate TOYO’s dynamic culture change, switching to paperless work flow at construction sites.
As a first step, TOYO has recently developed a new application named BBO (Behaviour Based Observation) Report Application as shown in Fig. 1.
This application has been developed to completely eliminate the paperwork associated with reporting near miss accident reports at construction sites. Previously, BBO reports were submitted in a paper format by workers, supervisors and site personnel, and consolidated in Microsoft Excel spreadsheets by a data entry clerk. The task took a long time to complete and on occasions there were unexpected input errors.
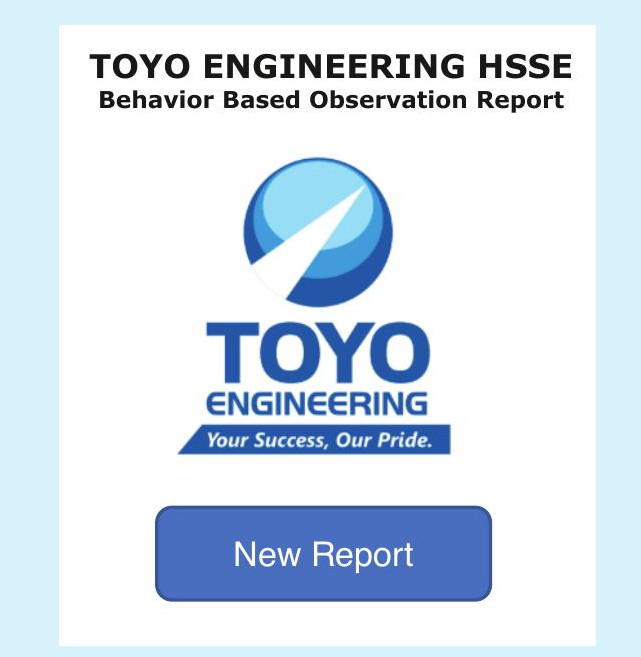
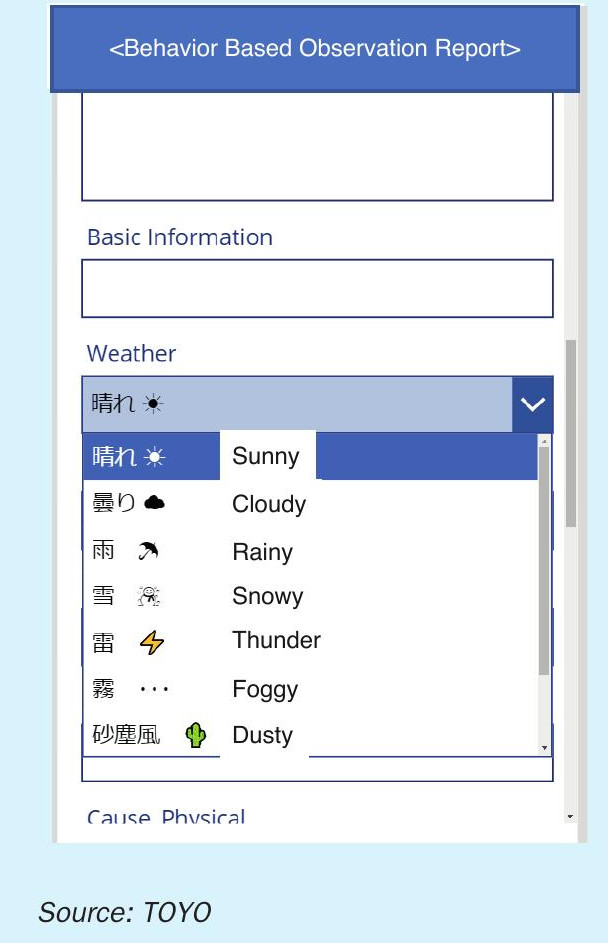
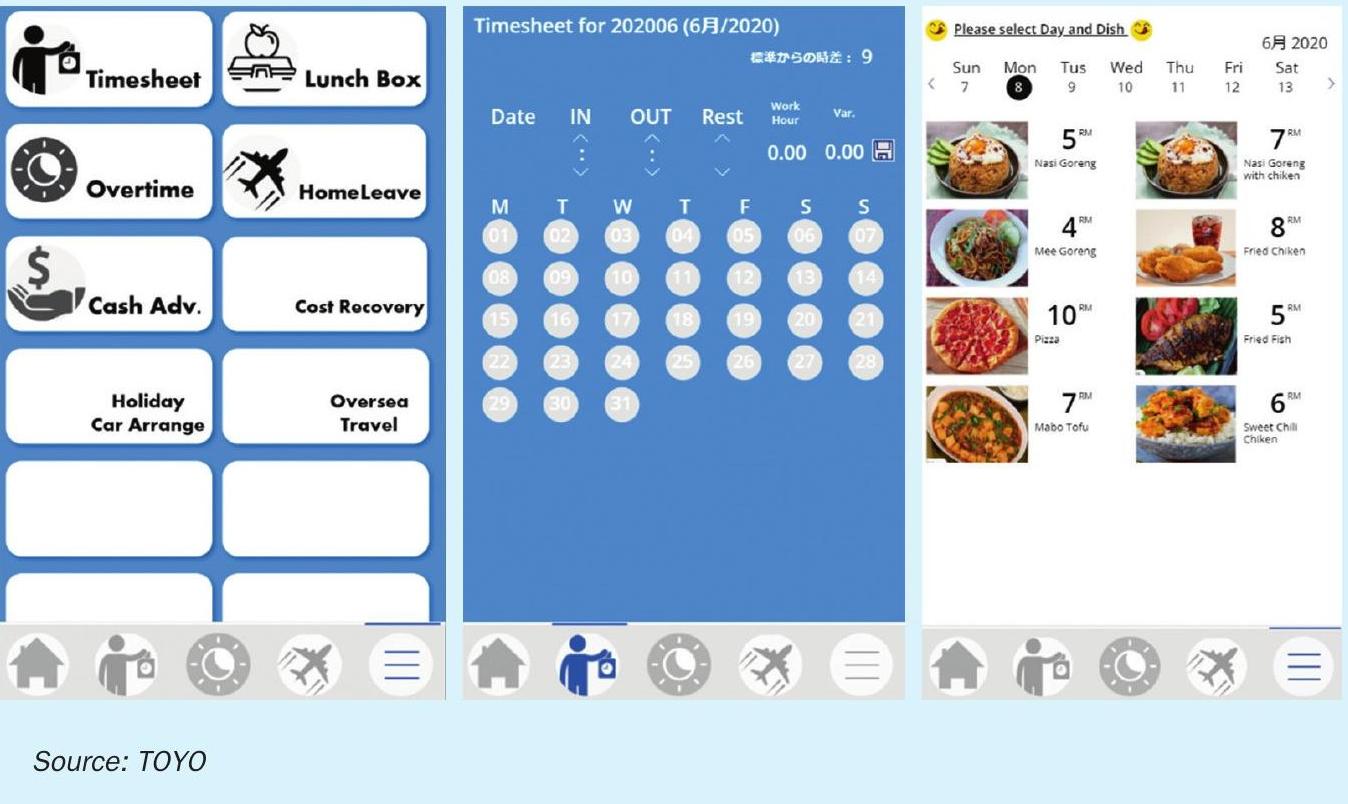
The new app has features which allows users to take photos and input information from a dropdown list using a smartphone, tablet and/or laptop etc. The information is then submitted directly to a database. The information stored in the database is analysed by Microsoft Power BI, which is a business analytic service by Microsoft, so that anyone at the site can check event trends and also utilise them for HSE flash reports, weekly reports, safety awareness posters, and so on.
TOYO is also making use of several other apps at sites e.g. to request personal protective equipment (PPE), for transportation, and to input timesheets, amongst others. There is even an app for lunch boxes/midnight snacks, which allows construction site staff to make their requests from anywhere, making life more comfortable for everyone on the construction site, which has a positive effect on human health and good performance of daily tasks (see Fig. 2).
This application targets 500+ TOYO directly employed members of staff and has resulted in three unexpected positive results:
- an accurate log from users (staff) during working hours automatically
- time savings for both the applicant and administration
- prevents submissions and actions from being overlooked.
Switching from a paper based system to the new paperless app based system has provided an easy and timely method of collecting the data of field activities and behaviour which can be utilised for preventative measure for HSE. TOYO is now recommending the paperless system for all construction sites.
Digital signage
Throughout its EPC projects TOYO has always recognised the truth and importance of the proverbs “seeing is believing” and “one picture is worth a thousand words”. Learning from these proverbs is highly effective, however, recently more optical tools, such as movies or videos, are being used in place of still images.
This trend is evident not only in construction sites but also in several situations where people need to deliver and visualise their message more clearly. Utilising better visual tools also has an important and positive impact in terms of Health, Safety, Security and Environment (HSSE) management for all of involved staff and workers at EPC construction sites.
Recently, to meet HSSE requirements, TOYO launched using an electrical display, so-called digital signage, at a construction site in Japan. This digital signage showed the important HSSE information that needed to be announced to all members in a daily morning toolbox meeting. At times it displayed construction progress with drone aerial video; it alerted staff and workers to prevent personnel from entering restricted areas by showing a map; and it announced major activities or site events such as heavy lifting, power receiving, steam blowing, or VIP visits (see photo, left).
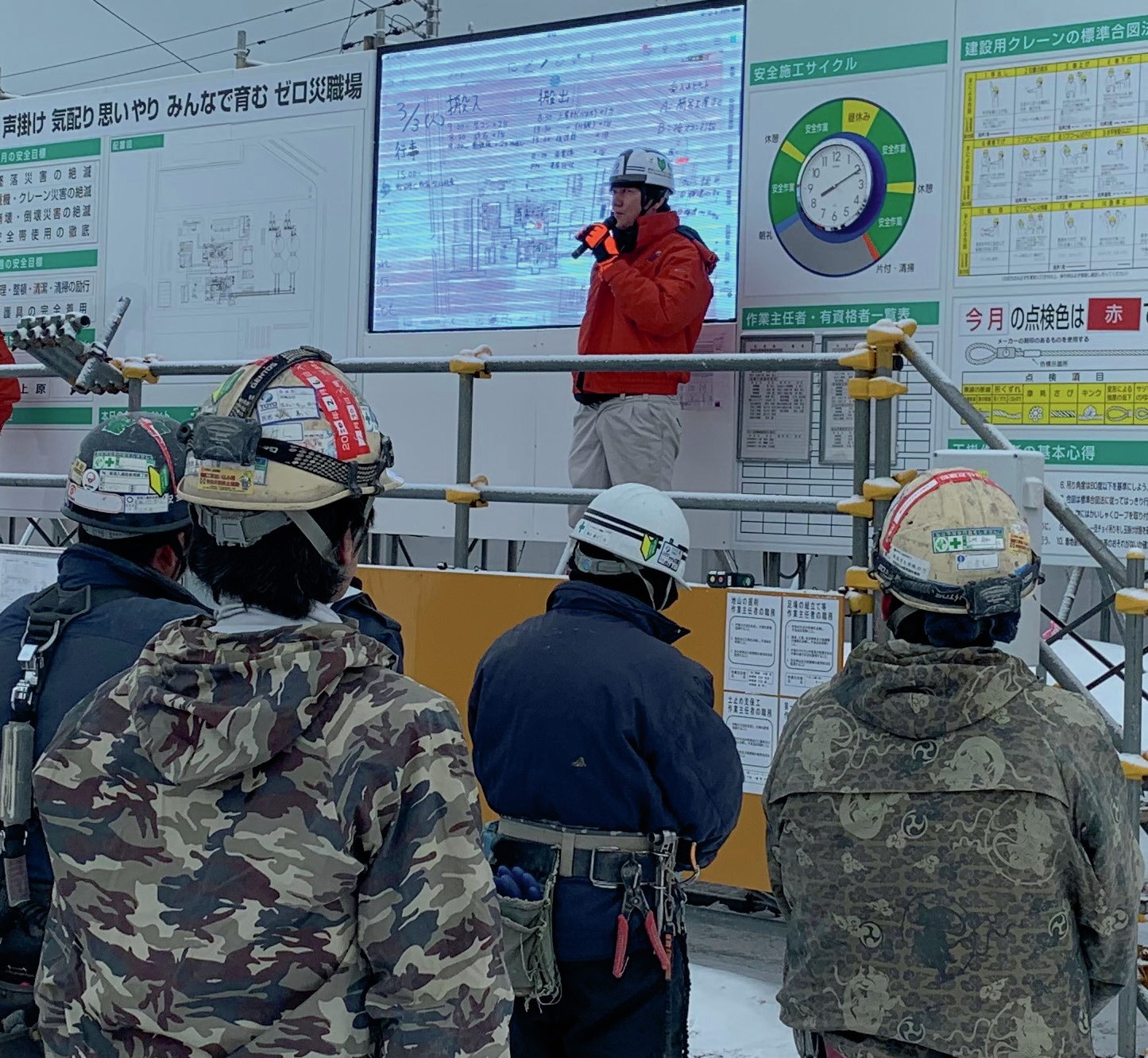
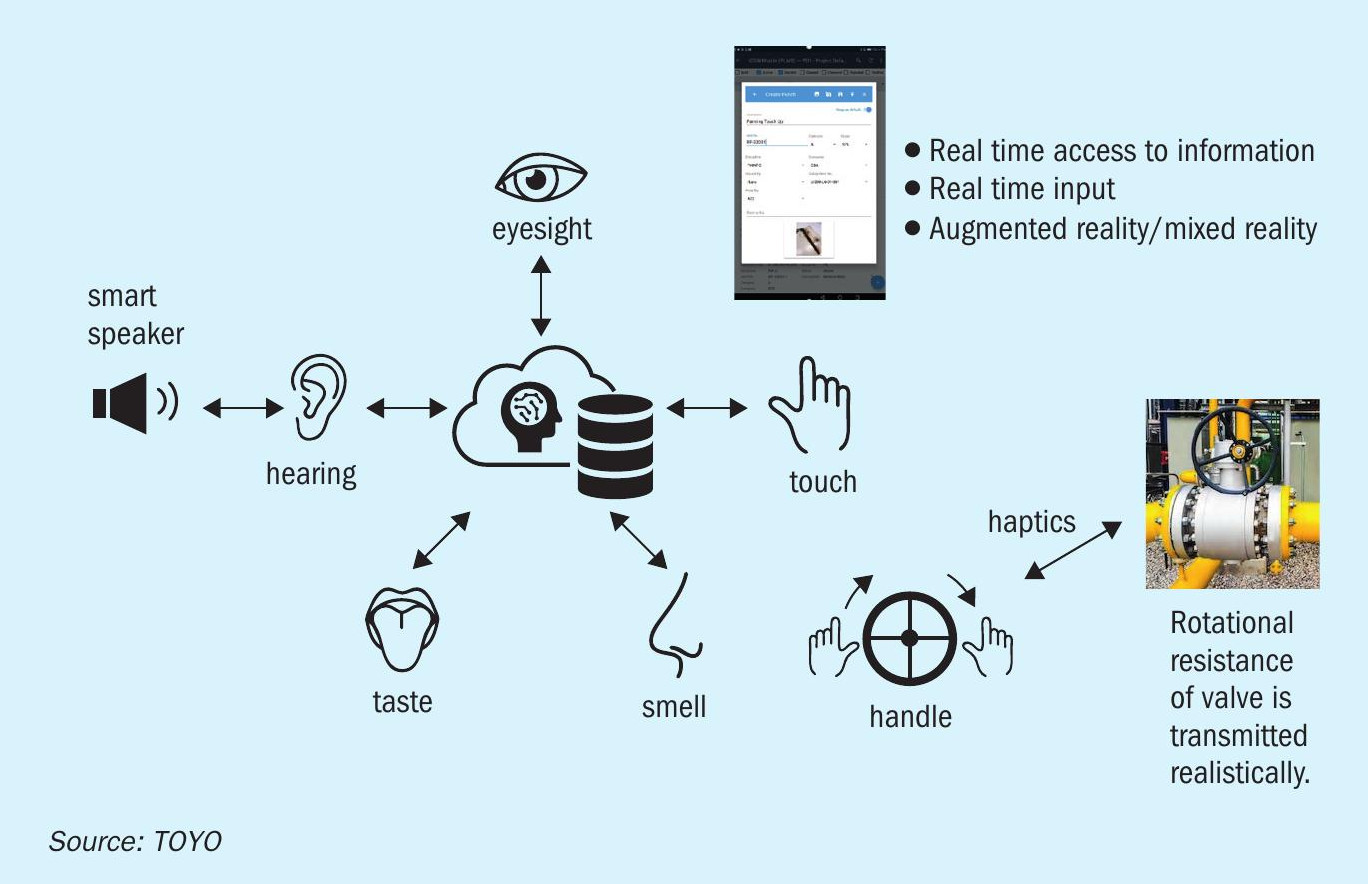
The digital signage allows all information to be shown effectively in a visible digital manner. In the conventional style of toolbox meeting, messages were delivered via a voice message only. Considering the translation issue into various languages for all involved persons, e.g. Japanese, English, Bangladeshi, Malaysian, Singaporean or Chinese, it was quite difficult to provide a clear message in some cases. Visualisation using digital signage can address some of these concerns and is a more effective way to provide information to members. In the near future, TOYO also plans to use projection mapping to make messages even more powerful and to keep all members at the site safe using good communication.
AI speaker (Safety Smart Speaker)
Due to the evolution of the Internet of Things (IoT) and artificial intelligence (AI), various ICT solutions that handle the five senses of human beings have been introduced in the industry. Especially at construction sites, speaking to a smart speaker is considered an effective way to enable hands-free operation. It is important for safety that construction crew can receive information without picking up paper, documents, or mobile phones. In addition, voice recognition is easy to achieve for construction crew. The concept of using smart speakers at sites is shown in Fig. 3.
In 2020, TOYO built a prototype Safety Smart Speaker. When users say some keywords into the speaker, the speaker gives alerts/reminders to users by showing past incident cases with appropriate safety measures that are highly relevant to the keywords. The Safety Smart Speaker not only displays the information but also provides a voice reading of incident cases. The smart speaker technology was introduced by NSE (Nippon Steel Engineering), which has a comprehensive collaboration agreement with TOYO. Currently, the screen for past incident cases is being improved further and the search result will be listed with a risk ranking (See Fig. 4).
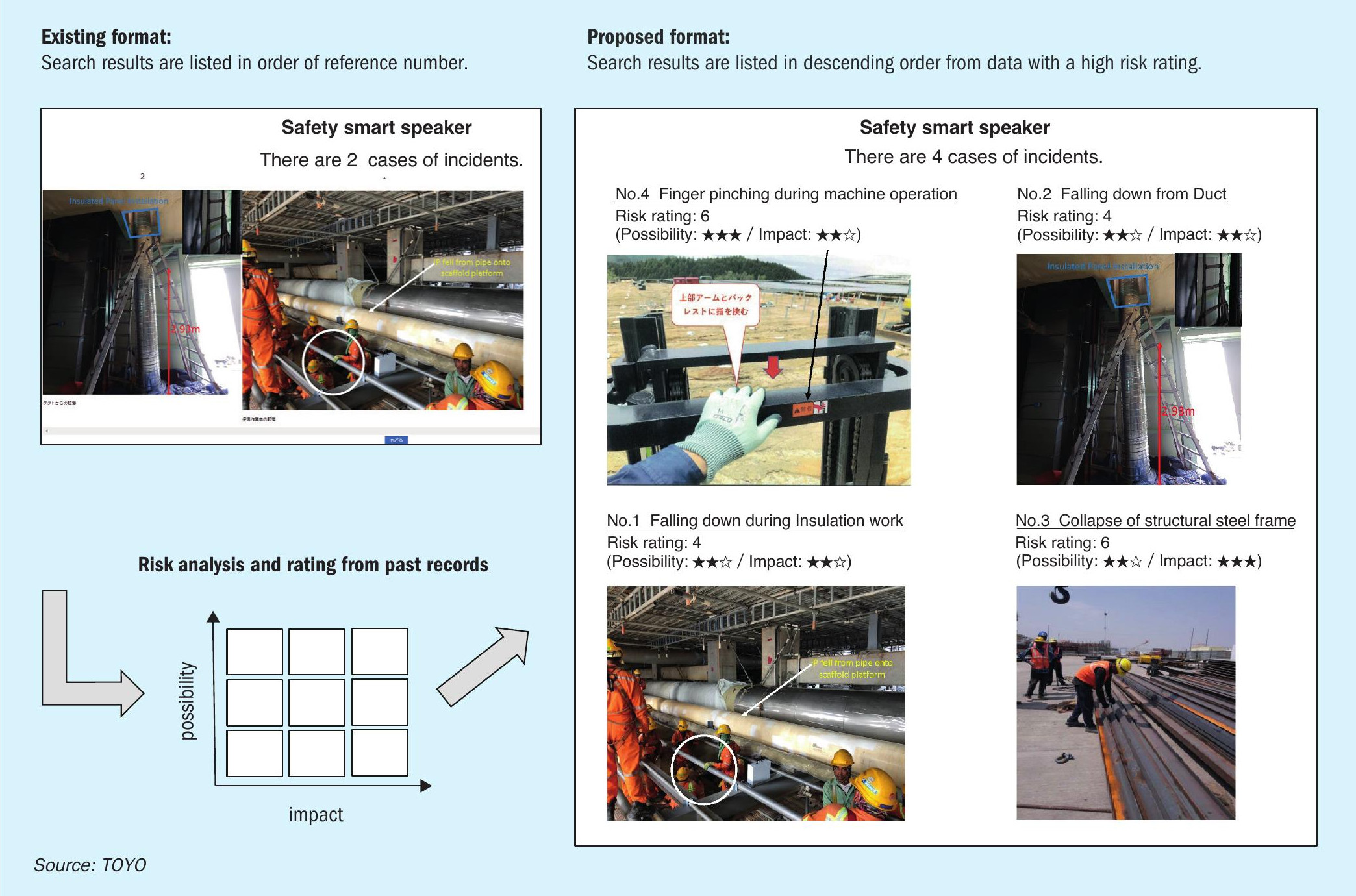
- At the safety training centre: Instead of reading a tough paper bulletin, workers can easily increase safety awareness by talking to a Safety Smart Speaker and getting a reply.
- For regular inspection: Not only for safety, the Safety Smart Speaker can also be utilised for regular inspection.
- The inspectors hold inspection tools in their hands. Where paper checklists are used, the inspectors need to stop working and hold the paper checklist. The Safety Smart Speaker provides a voice checklist which is hands free.
- Receiving feedback from site: To activate site safety awareness, not only giving workers past incident information, feedback input from workers is effective.
TOYO will soon introduce Safety Smart Speakers as standard in the settings mentioned above. Furthermore, TOYO will develop ICT solutions that fosters safety culture by appealing to the five senses of human beings.