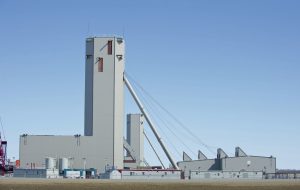
Fertilizer Industry News Roundup
BHP has finally given the go ahead for stage one of its Jansen potash mine project in Saskatchewan, Canada.
BHP has finally given the go ahead for stage one of its Jansen potash mine project in Saskatchewan, Canada.
OCI subsidiary Fertiglobe says that it has partnered with the Abu Dhabi National Oil Company (ADNOC), to enable the sale by ADNOC of the first cargo of blue ammonia to Itochu in Japan, for use in fertilizer production. Fertiglobe, a 58% − 42% partnership between OCI and ADNOC respectively, will produce the blue ammonia at its Fertil plant at Ruwais in Abu Dhabi for delivery to ADNOC’s customers in Japan. This represent the first production milestone of a planned scale-up of blue ammonia production capabilities in Abu Dhabi, which is expected to include a low-cost debottlenecking program at Fertil. In addition, it was announced in June that Fertiglobe will join ADNOC and sovereign wealth fund ADQ as a partner in a new world-scale 1.0 million t/a blue ammonia project at Ta’Ziz in Ruwais, subject to regulatory approvals. The design contract for this project has been awarded, with a final investment decision expected in 2022 and start-up targeted for 2025. A feasibility study was also agreed in July betweenh the state-owned Japan Oil, Gas and Metals National Corp. (Jogmec), Inpex and JERA as well as ADNOC to explore the possibility of producing 1.0 million t/a of blue ammonia in Abu Dhabi and transporting it to Japan.
By utilising state-of-the-art technologies, nitric acid and ammonium nitrate producers are able to reduce the environmental impact of their production plants and make a key contribution to climate protection.
INEOS Enterprises has announced the completion of the sale of its Sulphur Chemicals business to International Chemical Investors Group, for an undisclosed sum. INEOS Sulphur Chemicals business is Spain’s largest dedicated manufacturer of sulphuric acid and oleum, serving clients in both agriculture and chemical intermediates via its 400,000 t/a plant in Bilbao. The business will become part of WeylChem’s advanced intermediates and reagents portfolio, which includes an existing sulphuric acid and oleum plant located in Lamotte, northern France. WeylChem is wholly owned by the International Chemical Investors Group (ICIG).
We highlight the large-scale nitrogen projects that are currently under development across the globe – with a focus on ammonia and urea technology licensors and engineering contractors.
The European Union is seeking to create a climate-neutral and circular economy through its flagship Green Deal policy. The fertilizer industry can support these objectives by adopting inhibitor treatment technology (ITT) and controlled-release fertilizers (CRFs) based on biodegradable polymers. These two innovations have a vital role to play in improving nitrogen use efficiency and the shift towards more sustainable resource use, says Dr Matthias Potthoff of thyssenkrupp Fertilizer Technology.
A consortium has unveiled plans to build one of the largest green hydrogen plants in the world in a bid to make Oman a leader in renewable energy technology. The $30 billion project is being developed by Oman’s state-owned oil firm OQ, green fuels developer InterContinental Energy and Kuwait government-backed renewables investor EnerTech. Construction is scheduled to start in 2028 in Al Wusta governorate on the Arabian Sea. It will be built in stages, with the aim to be at full capacity by 2038, powered by 25 GW of wind and solar energy. Two years has already been spent on solar and wind monitoring analysis for the development. According to the consortium, the site chosen has the optimal diurnal profile of strong wind at night and reliable sun during the day, and is also located near the coast for seawater intake and electrolysis.
Developments in sulphuric acid technology and engineering know-how are highlighted by recent project case studies from DuPont Clean Technologies, Metso Outotec and thyssenkrupp Uhde.
As recently as five years ago, decarbonising fertilizer production was little more than an aspiration.
CF Industries has signed an agreement with thyssenkrupp to develop a commercial-scale green ammonia project at its Donaldsonville production complex in Louisiana.