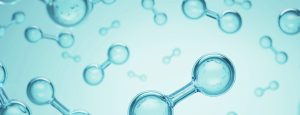
Blue hydrogen at scale
Blue hydrogen has emerged as a crucial technology for decarbonisation as nations around the world work towards net-zero carbon targets. By decarbonising hydrogen production and exploring clean hydrogen sources we can fully harness the potential of hydrogen in the global energy transition. Johnson Matthey, Topsoe and Casale report on their strategies and advanced technical solutions for large scale blue hydrogen production.