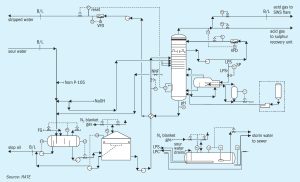
Sour water stripping gas processing options
M. Rameshni and S. Santo of RATE discuss different sour water stripping gas processing options, depending on contaminants in the sour water streams and site-specific requirements.
M. Rameshni and S. Santo of RATE discuss different sour water stripping gas processing options, depending on contaminants in the sour water streams and site-specific requirements.
The UK has published its Hydrogen Strategy, setting out the government’s ambition to create a low carbon hydrogen sector, with up to one third of the UK’s energy consumption being hydrogen-based by 2050. The commitments set out in the strategy unlocks £4 billion of government investment by 2030. The government plans 5GW of low carbon hydrogen production capacity and the establishment of carbon capture, use and storage (CCUS) in four industrial clusters by 2030, as well as blending of hydrogen into the existing gas network and a ‘twin-track’ approach to hydrogen production, using both electrolytic and CCUS-enabled low carbon hydrogen production in order to scale up production in time to meet the UK’s 2030 and 2050 carbon emissions targets.
Johnson Matthey’s latest methanol synthesis catalyst, KATALCO™ 51-102, was introduced in 2018 to offer improved catalyst stability and therefore higher end-of-life activity and extended lifetimes than conventional methanol synthesis catalysts. Since launch, KATALCO 51-102 has been successfully installed in two methanol plants and a third is planned for later in the year. In this article Johnson Matthey provides an update on the proven performance of KATALCO 51-102 during lab and pilot scale testing as well as in customer plants. The application of catalysts made using the KATALCO 51-102 technology for methanol synthesis via new ‘green’ routes, such as using captured and purified CO2 in conjunction with ‘green’ hydrogen, is also discussed.
By utilising state-of-the-art technologies, nitric acid and ammonium nitrate producers are able to reduce the environmental impact of their production plants and make a key contribution to climate protection.
MegaZonE™ is a newly introduced layered loading technology for boiling water-cooled reactors used for methanol synthesis. This new concept is one of the latest results of the long-standing collaboration between Air Liquide Engineering & Construction and Clariant Catalysts to improve the methanol process flowsheet and optimise catalyst performance in the complete reactor system.
Chemetics describes a variety of ways to extend the life of sulphuric acid plants. Debottlenecking, emissions reduction and/or energy recovery projects require a systematic, phased approach to maximise the potential of economic and operational benefits to the owner.
Tightening regulations and growing global competition are increasing the pressure felt by sulphuric acid plant operators to reduce emissions and improve energy output. Conservation of energy is a continuous focus for operators, and environmental communities have grown more vocal in their desire for greater emissions oversight. In this article, DuPont Clean Technologies examines simple, tried, and true tactics, as well as new products and designs that can be incorporated into existing plants to address operating efficiency and emissions and to help to prolong the life of the plant.
INEOS Enterprises has announced the completion of the sale of its Sulphur Chemicals business to International Chemical Investors Group, for an undisclosed sum. INEOS Sulphur Chemicals business is Spain’s largest dedicated manufacturer of sulphuric acid and oleum, serving clients in both agriculture and chemical intermediates via its 400,000 t/a plant in Bilbao. The business will become part of WeylChem’s advanced intermediates and reagents portfolio, which includes an existing sulphuric acid and oleum plant located in Lamotte, northern France. WeylChem is wholly owned by the International Chemical Investors Group (ICIG).
Comprimo has recently launched two new solutions to make the most of existing data and to improve customer’s operations and customer knowhow: Comprimo Insight – an intelligent sulphur plant dashboard, and Comprimo Immerse – a dynamic sulphur plant simulator. In this article, Comprimo goes into the details of how Comprimo Insight and Comprimo Immerse are being implemented for its customers.
The internals of ammonia synthesis converters are generally made of austenitic stainless steel to withstand the harsh operating conditions (high temperature, high pressure and synthesis gas containing hydrogen and ammonia). Since nitriding is the most critical material degradation for the converter internals, Casale has set up a large nitriding analysis campaign. In the last decade, samples of materials operated under different pressures and temperatures and for different time spans have been tested and analysed. The data obtained has been used to increase nitriding knowledge and to establish a correlation to predict nitriding rate to allow the most suitable material and relevant thickness to be selected. L. Redaelli and G. Deodato of Casale report on how this correlation was established and provide valuable insight on this phenomenon and how to predict and control it.