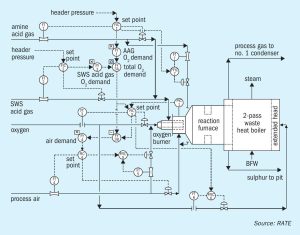
SRU revamping for emissions compliance and capacity increase
With the sulphur content of crude oil and natural gas on the increase and with the ever-tightening sulphur content in fuels, refiners and gas processors will require additional sulphur recovery capacity. At the same time, environmental regulatory agencies of many countries continue to promulgate more stringent standards for sulphur emissions from oil, gas and chemical processing facilities. Rameshni & Associates Technology and Engineering discusses options for compliance with new regulations on emissions regarding IMO 2020 compliance and report on the results and evaluation of three case studies. Worley Comprimo reports on the revamp of a sulphur complex built in the late 1980s at a refinery in East Asia with the aim to increase the capacity, improve the availability and reliability and make the unit environmental compliant.