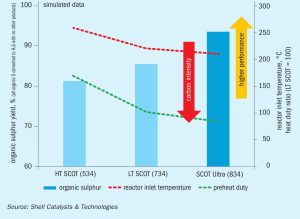
Decreasing tail gas treating carbon intensity through solvent and catalyst swaps
Decreasing the carbon intensity of sulphur recovery is one of the many actions that operators can take to help meet their climate ambitions. It is also becoming increasingly rewarding financially because of the rising cost of carbon emissions. In this article, G. Kidambi of Shell Projects & Technology demonstrates the potential to cut the carbon intensity of tail gas treating units by more than 50% through swapping to the latest SCOT ULTRA amine solvent and catalyst technologies.