Nitrogen+Syngas 396 Jul-Aug 2025
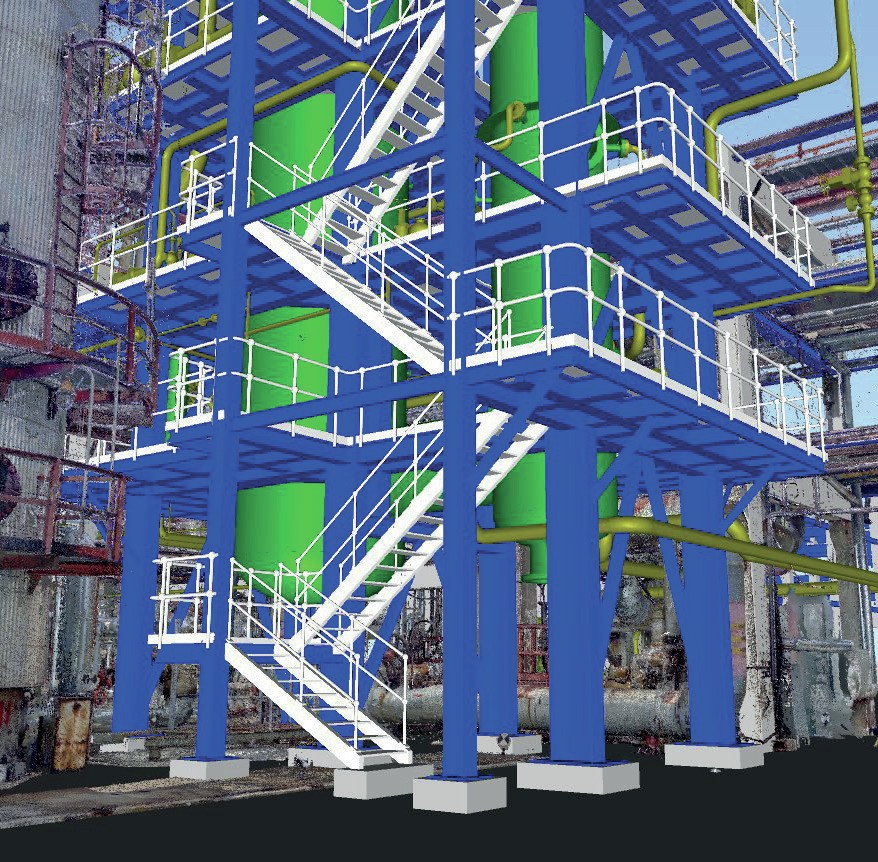
9 July 2025
Revamping methanol plants for sustainable decarbonisation
Casale is specialised in revamping natural gas-based methanol plants. Decarbonisation of methanol plants is a goal for many producers achievable with a proper revamping strategy. Pietro Moreo of Casale discusses how Casale’s innovative technologies and extensive experience ensure reliable efficient capacity and performance enhancements together with CO2 emissions reduction tailored to meet revamping project targets.
Significant carbon emissions are attributed to the methanol Industry (about 200 million tonnes/annum). In many countries direct carbon pricing or compliance instruments like carbon taxes have been implemented or will be put in place in the near future. It is a matter of fact that this trend will have an important impact on methanol plants in view of the associated costs.
Most of the lifecycle emissions associated to methanol molecule resides in the end-of-life stage, for instance when the methanol is combusted in a ship or other transport vehicle. These emissions are stoichiometric and cannot be avoided. They are the same for any methanol. In methanol from natural gas (NG), the end of life is, on average, about 60% of the overall emissions. Without considering end of life, about half of the emissions are associated to production in the plant while the remaining are for NG production and transport and for methanol product transport.
Therefore, plant design can have direct impact only on this portion of the methanol carbon footprint and, indirectly, on other NG production and transport.
The price of carbon in the world has been increasing significantly, from $20 up to values higher than $80, and this trend is going to identify a further not negligible difference in the production cost as a consequence of the plant efficiency and carbon intensity.
Plants equipped with syngas generation via oxygen (SMR+ATR, pure ATR, Exchange Reformer + ATR, etc.) achieve very low carbon intensity and energy consumption (approx. 0.3 tonne CO2/tonne CH3OH); modern pure steam reforming (SMR) based units have higher emissions (about 0.5-0.6 tonne CO2/tonne CH3OH) while vintage plants have emissions up to 1 tonne CO2/tonne CH3OH. In view of the trend of carbon prices, the gap in production cost is going to depend not only on NG cost and relevant consumption but also on CO2 emissions and relevant price or compliance instruments.
CO2 emissions reduction and energy saving for existing vintage SMR based units mean significant methanol production cost reduction; CCS (carbon capture and sequestration) is an option but with significant associated costs (30-120 $/t CO2). CCS needs several associated infrastructures (pipelines, ships, storage, etc) almost always not linked to methanol producers’ core business; plant NG consumption is increased by CCS (generally carbon capture requires additional steam and/or power).
On the contrary plant revamping affects efficiency in NG conversion to methanol, intrinsically leading to decarbonisation; it is important to underline that typically the emissions reduction target does not exclude combination with capacity increase; revamping is the real sustainable route to improve margins reducing the cost associated to carbon compliance.
The target of the revamping is the key parameter to select the right philosophy of intervention: Casale is in the position to customise its own technologies to suit clients’ specific needs.
Gained through 30 years of experience, Casale has acquired an unrivalled track record in revamping (retrofitting) existing plants of any type to improve their performance and, with it, a deep knowledge of the workings of fertilizer and methanol plants.
If a revamping option is already available from previous experience, it is included in the revamping experience concept that provides a detailed definition of the most appropriate solution for customer’s unit.
The integration of process and engineering know-how and project implementation capabilities has enabled Casale to be a world leader in plants revamping. Casale’s wide technology portfolio includes items suitable for revamping any plant type and section.
Revamping of the syngas generation section is usually only considered for plant capacity increase but it is also the most important section for energy saving and emissions reduction. Revamping of the reforming section for capacity increase, energy saving and CO2 emission reduction can be carried out according to different strategies which can be alternative or complementary. The technologies suitable for this purpose are:
- pre-reforming;
- partial oxidation reactor (POx);
- autothermal reactor (ATR);
- heat exchange reformer.
To maximise methanol production and, at the same time, to minimise energy consumption, it is imperative to have the highest possible carbon efficiency in the synthesis section. To achieve this goal, Casale has the unique advantage to retrofit the old adiabatic converters with its plate-cooled IMC internals. When revamping of the main reactor is not convenient, a different way of processing a higher flow of make-up gas is to install an additional converter with its own methanol condensing section downstream. This reactor is isothermal due to the superior efficiency and flexibility.
Revamping options for the distillation section should be evaluated to comply with the increased methanol production from the reaction section and/or with the energy saving targets.
Casale advises installing a pre-reformer reactor when the aim of the revamp is to increase the plant capacity. It allows the primary reformer to process additional natural gas without any alteration. So, it is particularly useful when no modifications can be made to the primary reformer. Alternatively, if the plant loading is not increased, the pre-reformer reactor allows the heat duty to the primary reformer radiant box to be reduced. The pre-reformer unit is an adiabatic reactor containing an optimised steam reforming catalyst. The catalyst is more active because it has a much higher nickel content than primary reformer catalyst. As its name suggests, the pre-reformer reactor is installed upstream of the primary reformer (Fig. 1).

All higher hydrocarbons are completely converted to methane, and equilibrium is established for the methane reforming and shift reactions. The product gas from the pre reformer contains only methane, carbon monoxide, carbon dioxide, hydrogen and steam – the ideal feed gas for the primary reformer. The Casale pre-reformer reactor design is based on axial-radial catalyst bed technology.
Because the gas from the pre-reformer is already partially reformed, it is possible to raise the throughput of the unmodified primary reformer by up to 10% without increasing the firing duty and thus without jeopardising the life of the catalyst tubes.
Several pre-reformers supplied by Casale are in operation in revamped ammonia and methanol plants (Fig. 2).
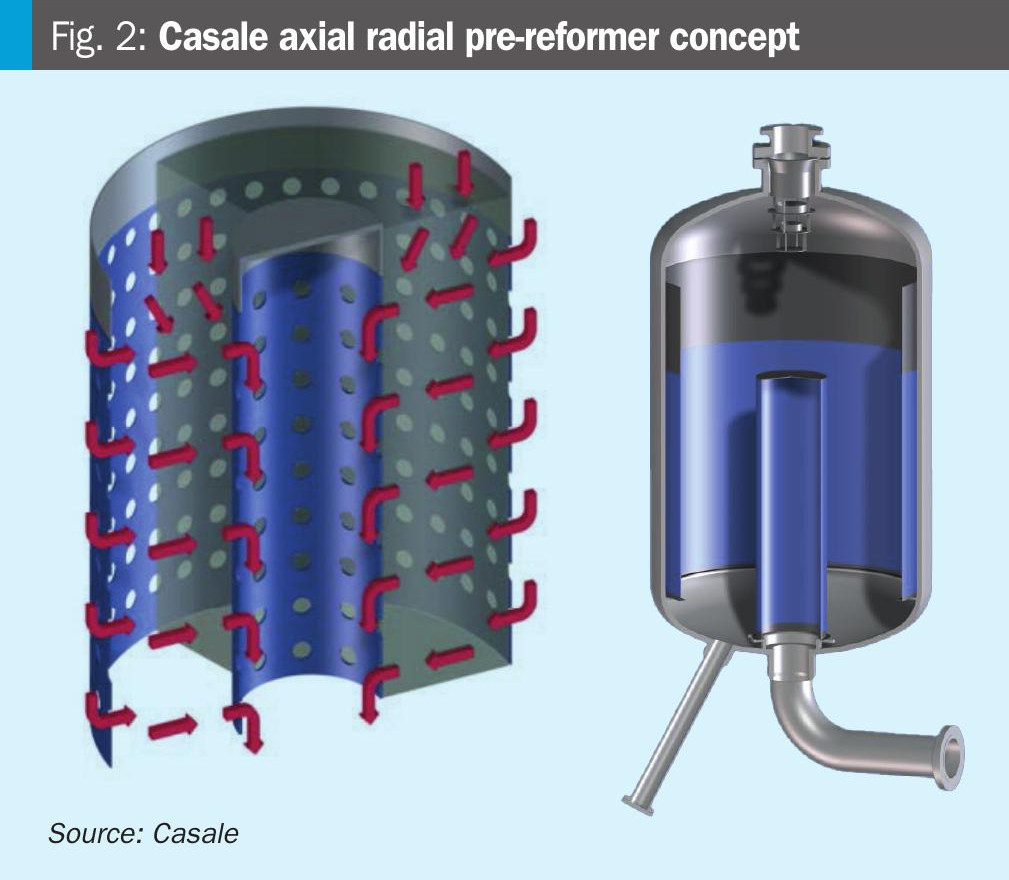
One of the most interesting ways to revamp the reforming section, if the target is to increase the plant capacity significantly and/or to reduce the energy consumption and CO2 emissions, is the installation of a high-temperature heat-exchange reactor that uses the residual heat in the effluent from the primary reformer to produce syngas from methane (steam reforming). In conventional plants, this high-grade heat (usually at a temperature of about 900°C) is used in the waste heat boiler to produce HP steam. Casale relies on the supply of the high-temperature heat-exchange reactor developed by Technip Energies, named TPR® (Technip Parallel Reformer®).
In the process scheme of a reforming section revamped with the TPR, the preheated mixed feed consisting of natural gas and process steam flows in parallel to the primary reformer radiant box (about 70-85% of the gas) and to the TPR exchanger reformer (about 15-30% of the gas). The outlet of the primary reformer is fed to the TPR shell side as heating medium for the steam reforming reaction of the tube side.
The TPR is a compact heat exchanger reactor for steam reforming. Other than in the fired reformer, the heat for the TPR is supplied by hot process gas rather than by hot flue gas. Up to 30% additional feed can be reformed using the TPR in parallel to the fired reformer.
Since the steam reformer effluent is used to meet the heat duty of the TPR, the steam production in the downstream process gas boiler is reduced significantly. The design is optimised considering both syngas and steam requirements. TPR minimises export steam, especially when steam revenues are not favourable. The technology further allows zero export steam enabling stand-alone plants that do not need to be connected to an external steam network.
TPR has provided cost-effective solutions to customers for more than 50 years and has been successfully employed in several hydrogen plants for capacity revamps (Fig. 3).
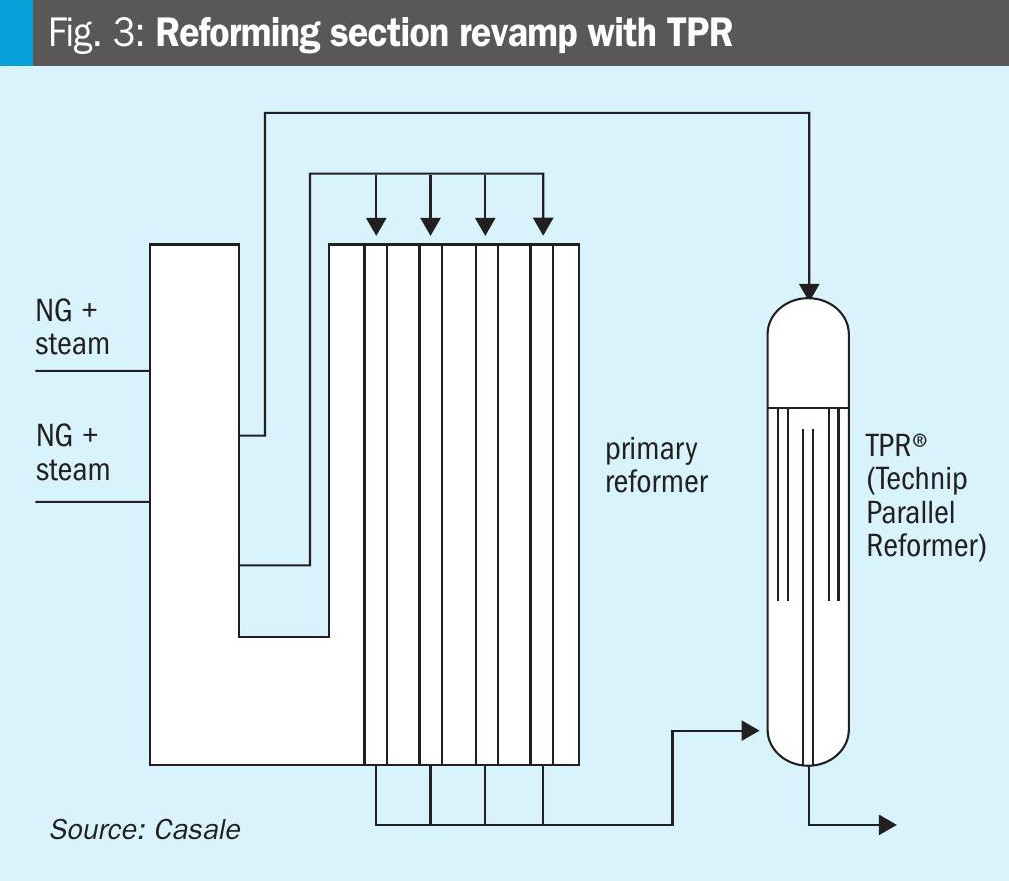
Autothermal reforming is an alternative technology to produce syngas for capacity increase purpose and/or energy saving and CO2 emission reduction.
The auto-thermal reformer (ATR) can be installed downstream of the primary reformer or in parallel to the reformer itself. Installation downstream of the reformer involves the modification of the front-end train and the replacement of the reformer waste heat boiler. This kind of solution can decrease the syngas stoichiometric number (SN = (H2-CO2)/(CO+CO2)) significantly and it is recommended when a large capacity increase is requested. The installation in parallel to the steam reformer requires a dedicated fired heater, waste heat boiler and it is generally combined with the installation of an upstream pre reformer reactor (Fig. 4).
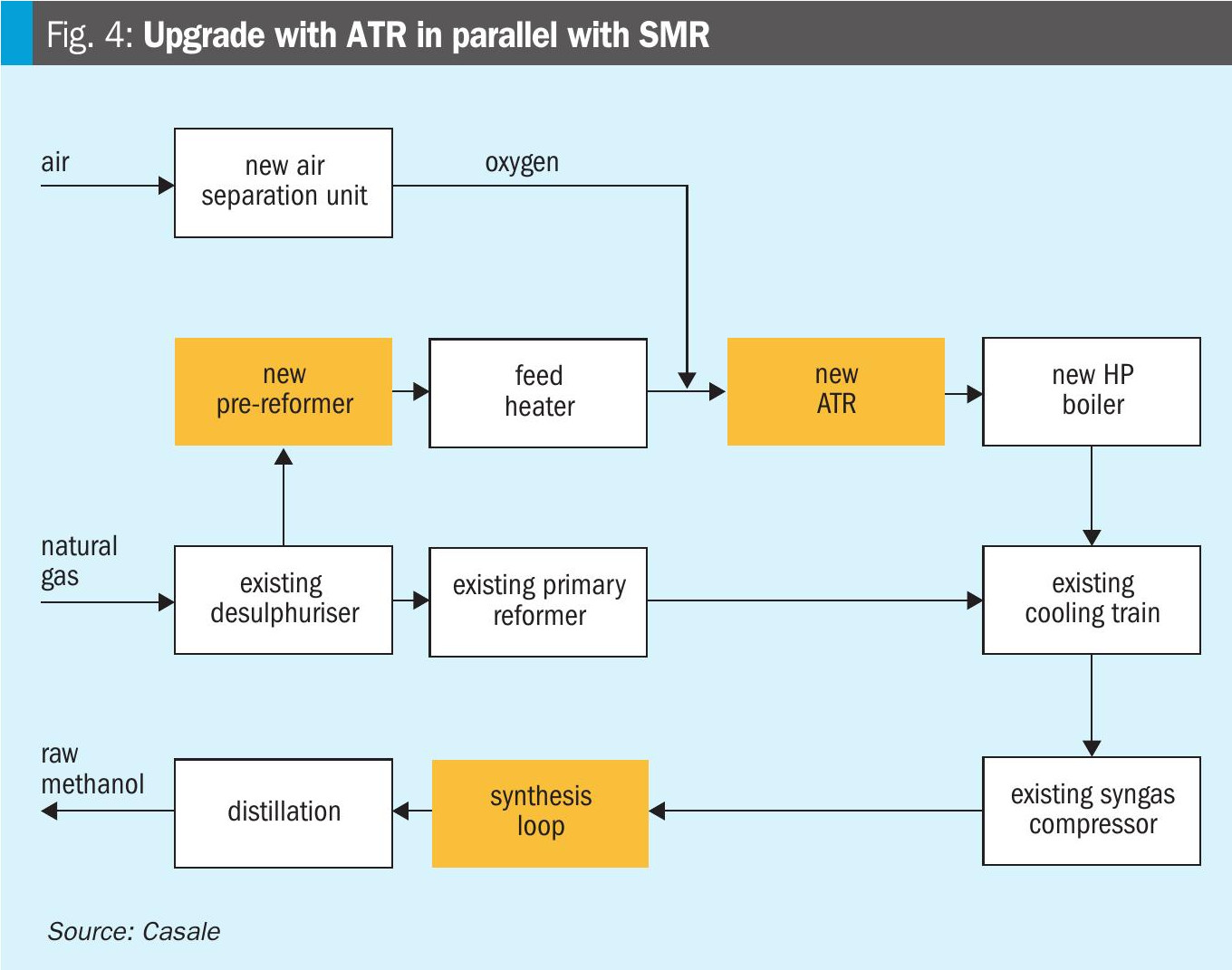
In autothermal reforming, the feed gas partially burns with oxygen from an air separation unit, providing the heat for the endothermic reformer reaction, that takes place on the catalyst bed. For this challenging service, the burner design is crucial for smooth operation and Casale provides a water-cooled design to improve reliability.
Casale has acquired sound experience in the design of ATR reactors for both ammonia and methanol production and for both two-step reforming and pure autothermal reforming (with natural gas or coke oven gas) configurations in revamping projects and in new plants. Casale has several referenced ATR reactors for methanol production in operation or scheduled for start-up, with capacities ranging from 350 to 7,000 t/d. At present there are more than ten units in operation equipped with a Casale ATR (Fig. 5), including two 5,000 and a 7,000 t/d methanol plant.
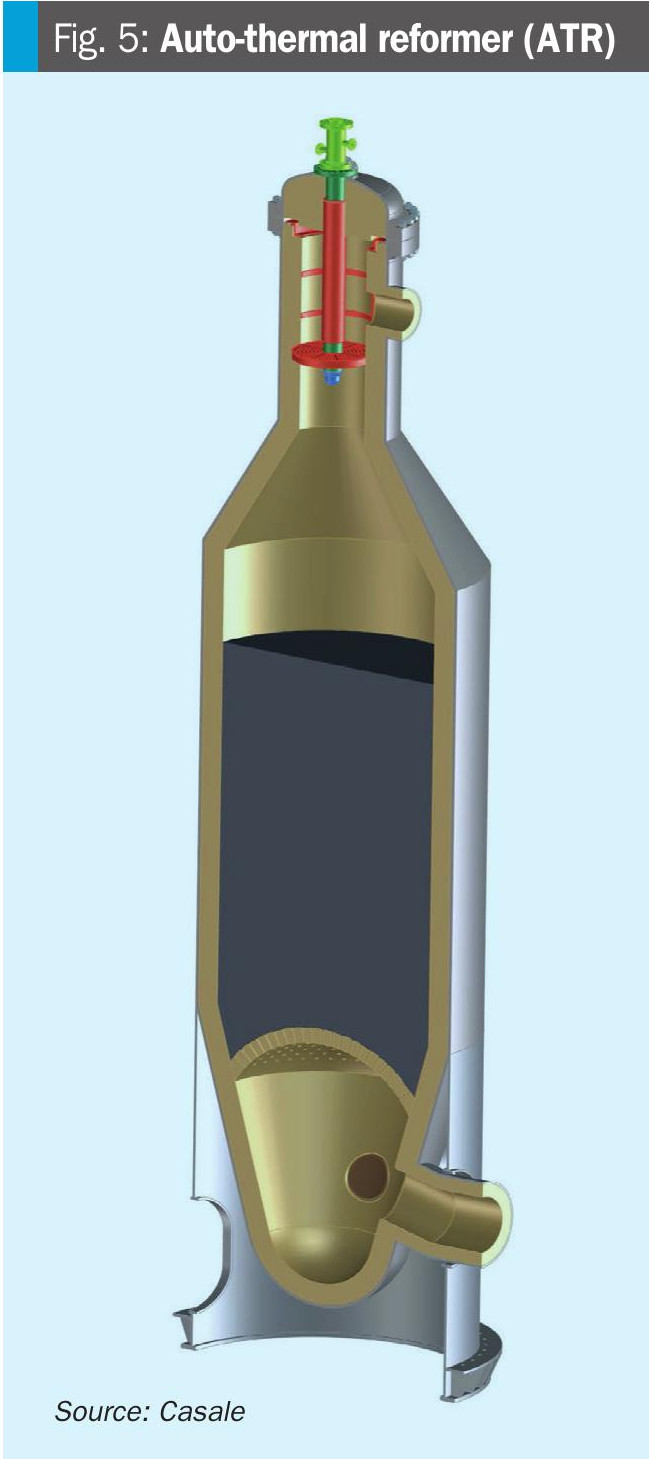
A different option for the plant revamping could be a new syngas generation section based on a pre reformer followed by an ATR fed with pure oxygen combined with a process heated reformer (TPR) in series/parallel to the ATR. This section is sized to generate the necessary additional syngas flowrate and it is equipped with Casale proprietary auto-thermal reforming unit, patented axial-radial pre-reformer reactor and with the Technip proprietary Parallel Reformer (TPR).
Thanks to these distinctive technologies, comparing this design with a standard pure ATR section, the natural gas consumption for the new syngas generation unit, with the TPR addition (Fig. 6), is expected to be reduced by up to 5% and the oxygen demand is reduced by more than 15%.
Furthermore, the size of the ATR fired heater and the size of the waste heat boiler are significantly reduced. Therefore, the proposed syngas generation process offers the following advantages:
- minimisation of the oxygen import and related electrical power consumption in the air separation unit;
- minimisation of fired duty for process purpose which leads to lower natural gas consumption and CO2 emissions;
- minimisation of fatal steam production with a lower investment cost linked to the lower size of the related steam system, including the waste heat boiler, steam drum, steam superheater, deaerator, HP BFW pumps.
Partial oxidation (POx) is an advanced technology that allows the production of syngas to be enhanced, creating a tangible value for the client. The new section is based on a POx reactor where natural gas reacts in the presence of oxygen without catalyst. Pure oxygen is generally supplied by an air separation unit.
With the installation of a POx reactor in parallel to an existing traditional primary reformer (Fig. 7), it is possible to increase methanol production by up to 30% with a single POx unit or to switch the production from the reformer to the POx reactor resulting in a decrease in the natural gas consumption in the range -5% to -15%. In addition, it should be underlined that the specific polished water consumption decreases thanks to the switch from steam reforming to O2 blown reforming.
The core of this advanced technology is the patented burner, developed using Casale’s deep knowledge of combustion and fluid dynamic phenomena to achieve very high combustion efficiency with low energy consumption and negligible soot formation. POx burners are subjected to the harshest conditions and are protected by cooling with a continuous circulation of boiler feed water: accurate design of the water-cooling system is essential to ensure a long and safe operating life when operating in such harsh conditions.
Revamping with POx technology (Fig. 8) has been implemented by Casale with a capacity increase of about 13%, a decrease in specific CO2 emissions of about 20% and decrease in specific natural gas consumption of about 6% compared to the former plant performances.
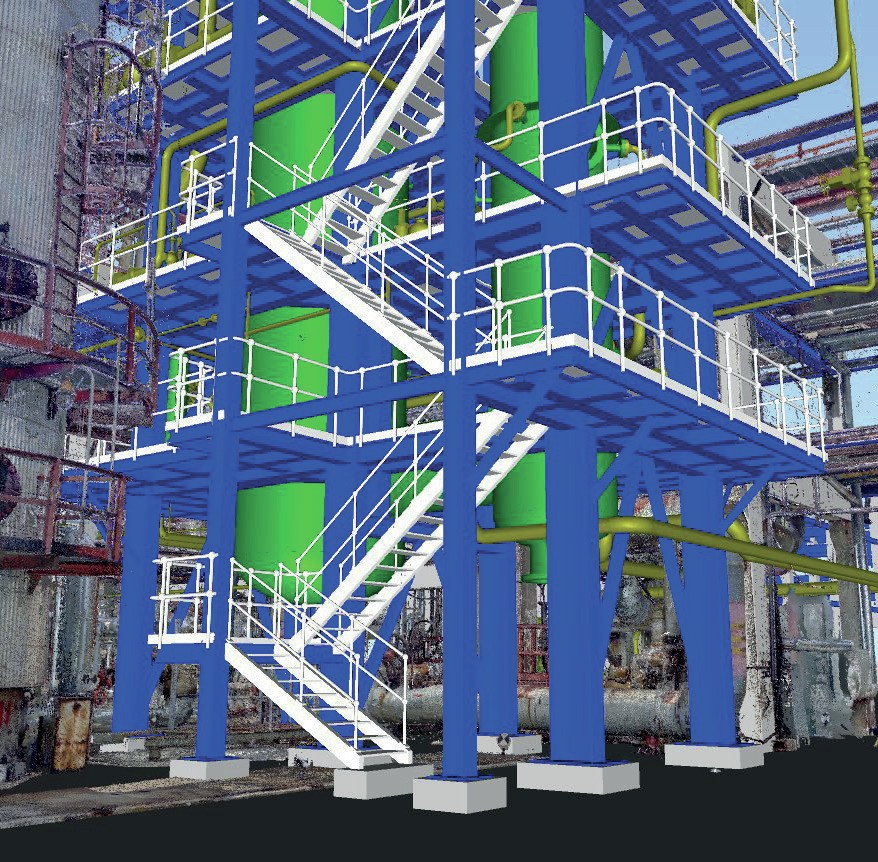
To maximise methanol production and, at the same time, to minimise energy consumption, it is imperative to have the highest possible carbon efficiency in the synthesis section. To achieve this goal, Casale has the unique advantage to retrofit the old adiabatic converters with its plate-cooled IMC internals. Casale is, in fact, the only company that can offer an “in situ” retrofit of the synthesis reactor with an isothermal design. Casale is also in the position to revamp and upgrade internal isothermal converter designed by its competitors with its plate cooled technology for capacity increase and energy savings. The modified synthesis section is also made ready to accept the additional and/or more reactive synthesis gas that is generated by POx or ATR. At present, several Casale Isothermal Plate Cooled Methanol Converters, installed though “in situ” retrofit, are on stream with capacities ranging from 400 t/d to 3,400 t/d. Synloop methanol production can be increased by up to 20% while the carbon efficiency can be increased by up to 10%.
A converter “in situ” retrofit has been successfully implemented in the QAFAC revamping project with the following associated benefits:
- higher plant output with lower specific energy and syngas consumption in the synthesis loop (higher carbon efficiency);
- longer catalyst life;
- higher operational stability and easier control of the reactor.
On its own, revamping with IMC™ (Fig. 9) has been ideal for achieving an immediate increase in capacity from an unchanged make-up gas flow, or the same capacity with a reduced makeup gas flow thanks to its higher carbon efficiency. Furthermore, the additional CO2 feedstock provided through the new CDR of SMR flue gas has allowed the plant to boost the capacity by an additional 150 t/d: the benefits of IMC™ retrofits are even more impressive if the front end is revamped at the same time for a substantial capacity increase.
When revamping the main reactor is not convenient, a different way of processing a higher flow of make-up gas is to install a downstream additional converter with its own methanol condensing section. If it is installed in the make-up gas line, it is called “once-through reactor” (OTR) because there is no mass recycle (Fig. 10).
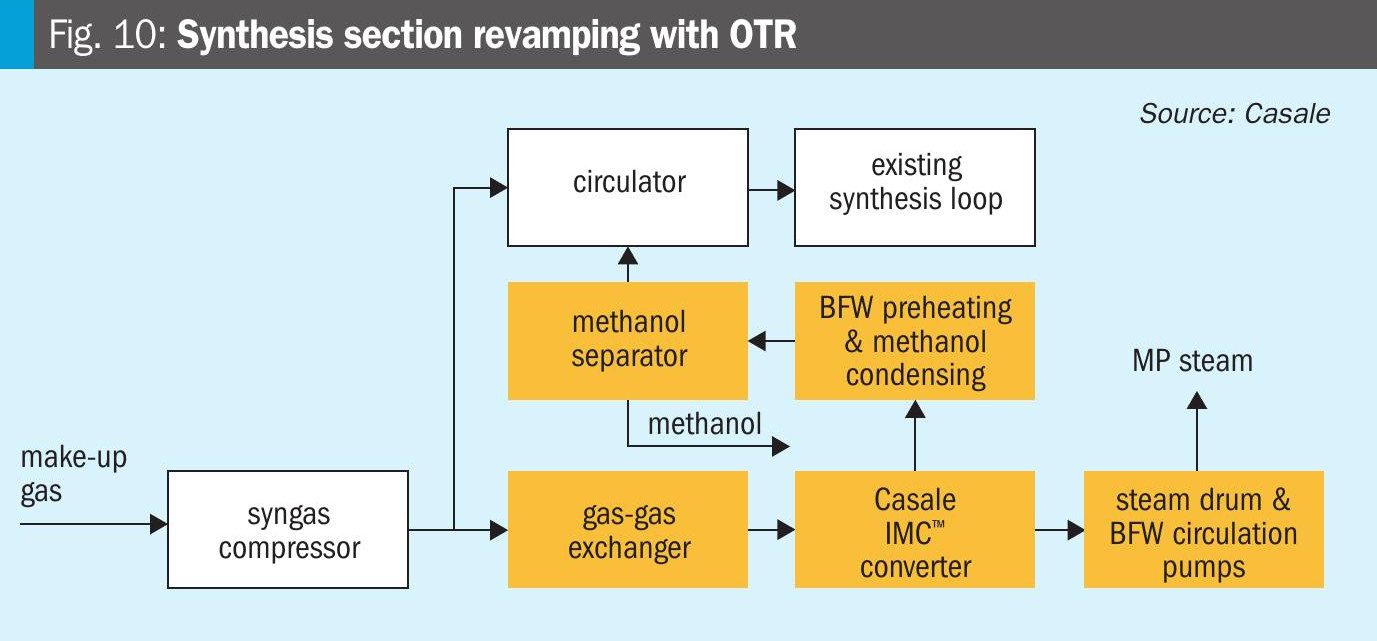
The methanol product obtained in this reactor is separated by condensation. The composition of the gas entering this converter is not optimised and therefore it does not achieve a particularly high conversion efficiency, but it does shift some duty off the synthesis loop, which can be exploited to increase overall production. On account of the gas composition for this specific scheme, the steam-raising configuration is preferred for the IMC converter.
The steam-raising IMC™ reactor in “once-through” mode has also been installed in revamping projects by Casale.
The crude methanol produced in the synthesis loop needs to be purified to reach the contractual grade specification (AA, A, IMPCA, etc.). Final purification is performed in two steps. A topping column separates the lighter compounds from the liquid mixture, while the refining section separates water and higher ends from the pure product, which is sent to storage. For plants of limited capacity (generally lower than 2,000 t/d) only one refining (heavy end column) step is foreseen. For higher capacities, the refining section is divided into two separate columns, one operating under raised pressure (about 7 bar g), the other at atmospheric pressure. This arrangement leads to a significant energy saving compared to the single refining column thanks to the “double effect” concept. The distillation section revamping options should be evaluated to comply with the increased methanol production from the reaction section and/or with the energy saving targets. For that reason, the possibility to increase the methanol production should be followed by any revamping action with the aim to remove the distillation section bottlenecks and increase the relevant nominal capacity.
For moderate capacity increase, the distillation section may already be suitable to process the extra capacity, since typically the original design foresees additional space for future interventions. In case the columns are not suitable for the new load, it is typical to revamp the column internals with high efficiency trays.
For extreme capacity increase or for improving the plant efficiency, Casale proposes the addition of a high-pressure column, where it is not already installed, along with the revamp of the internals of the existing ones (Fig. 11).
A high pressure column generally implies the replacement or the integration of the reboiler of the existing atmospheric refining column with a double effect reboiler/condenser: high pressure vapour condensation is used to supply the heat requirements for the second refining column. This modification introduces a significant energy saving too. The strategy can also be applied when the plant is already equipped with three columns introducing the “triple effect” concept. In addition, when the plant is already equipped with three columns, an alternative option is the new fusel oil recovery column: the column is fed with heavy end column fusel oil and part of the heavy ends column feedstock. Following this solution, the bypass of the refining column is sufficient to restore the original heavy ends column operation, removing the capacity bottleneck.