Nitrogen+Syngas 395 May-Jun 2025
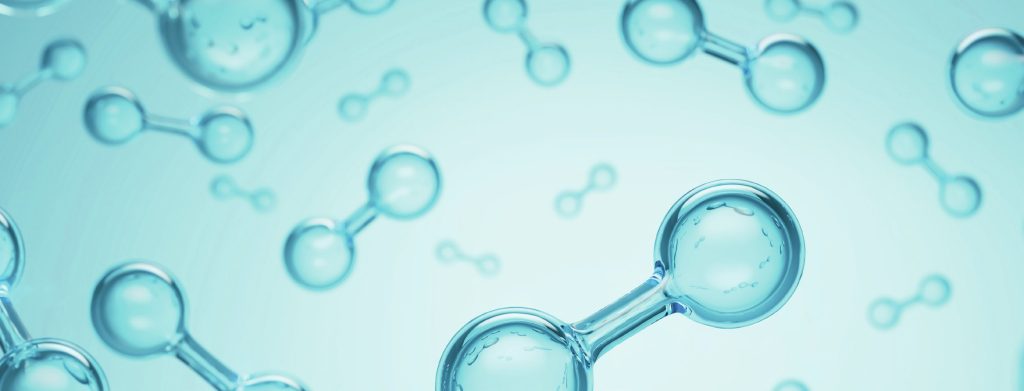
2 May 2025
KPIs for blue hydrogen technology selection
BLUE HYDROGEN
KPIs for blue hydrogen technology selection
Key performance indicators at industrial scale, such as feedstock consumption, carbon emissions, and overall costs are compared to evaluate the performance of several low carbon (blue) hydrogen production technologies. A detailed comparison of SCT-CPO, SMR and ATR technologies is reported considering the key driving capital costs and the related operational expenses to achieve net-zero emission requirements.
Hydrogen is a versatile fuel and chemical compound that can be produced from many energy sources, including coal, oil, natural gas, biomass, renewable energy, and nuclear power. Production can be accomplished through various technological processes, such as reforming, gasification, pyrolysis, electrolysis, and other advanced methods.
Depending on the feedstock and production method, many organisations informally classify hydrogen using a colour-based system1. Although this method is commonly employed, it can cause confusion since there is no universally recognised naming convention, despite the general acceptance of three main colours:
• grey hydrogen, created from fossil fuels, mainly natural gas, without capturing the greenhouse gases generated;
- blue hydrogen, produced from fossil fuels, where the carbon dioxide by-product is removed at source using carbon capture and storage (CCS) technologies;
• green hydrogen, generated by using clean electricity from surplus renewable energy sources, where no carbon is produced.
Although there is a wide range of hydrogen production technologies at different stages of commercial maturity, this study focuses on blue hydrogen technologies that use natural gas as a feedstock. While green hydrogen could become highly competitive in the future, considering factors like access to low-cost feedstock and government policies, in the near-to-medium term, blue hydrogen is likely to provide the majority of the world’s low-carbon hydrogen. This is due to its more mature production processes and the ability to deploy these facilities at a large scale in industrial clusters with CCS. This also meets industrial demand, which accounts for nearly 100% of current demand.
Steam methane reforming (SMR) with CCS in several configurations has been the subject of most blue hydrogen assessment studies to date, as well the most applied in the existing industrial facilities.
Autothermal reforming (ATR) is another worldwide-used technology to produce low-carbon hydrogen.
The Short Contact Time – Catalytic Partial Oxidation (SCT-CPO) is also applied, constituting an additional solution for improving some limitations of the current technologies.
This article provides an overview of three technologies and compares them to identify key performance indicators for selecting the best technology for blue hydrogen production.
Technologies description
Steam methane reforming (SMR)
SMR is currently the most utilised technology for syngas and hydrogen production2. Fig. 1 shows a typical SMR block flow diagram.
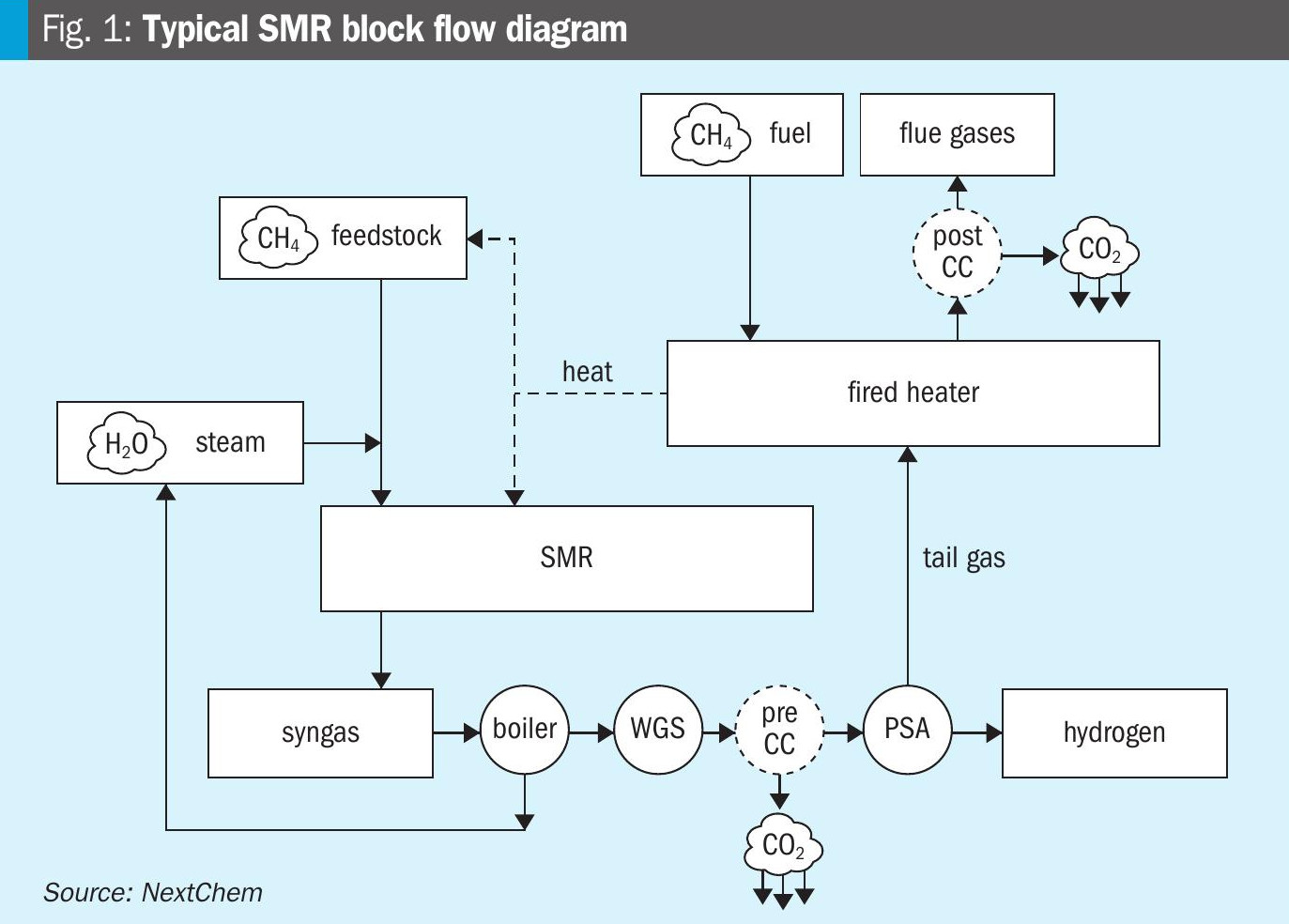
The endothermicity of SMR reactions requires an external heat source, which typically is a dedicated fired heater: reforming reactions take place inside the tubes located in the radiant section, while in the convective section, heat is recovered from the hot product gases for preheating the reactants feeds and for generating superheated steam. The presence of the furnace implies the utilisation of external fuel, with additional carbon dioxide emissions in the flue gases. A variation on this configuration is to use electrically heated reformers (e-SMR), significantly reducing carbon emissions directly produced from the facility.
The reactions are catalysed by Ni-based catalysts, included inside 500-600 tubes for large-scale plants. The inlet temperature is in the range 500-650°C, while gas temperatures at the exit of the tubes are higher than 800°C. The hydrocarbon feedstock is fed into the reforming tubes after sulphur removal, typically through hydrodesulphurisation reactors (HDS), and is mixed with steam at steam/carbon ratios higher than 2.5 v/v, more often higher than 3 v/v. This steam excess is required both for completing the hydrocarbon reforming reactions and for avoiding the occurrence of carbon formation reactions, which lead to pressure drop increase, catalyst deactivation and reaction rates reduction, causing serious heat transfer problems and tube damages.
The syngas produced by the SMR is then upgraded to hydrogen by shifting the CO and H2O into CO2 and H2 through the water gas shift (WGS) reaction. A single high temperature (HTS) or both high and low temperature (LTS) solutions can be foreseen to reduce the CO amount to values below 3 and 0.5 vol-%, respectively.
The WGS effluent is cooled, condensing the produced water, and fed into the carbon capture unit, where CO2 is removed to a level of 0.1 vol-% or less by adsorption in specific solvents, typically amine-based. The captured CO2 is then desorbed in a dedicated stripping tower. When the LTS step is used, the heat produced by the exothermic WGS reaction is used to reboil the CO2 stripper.
When the feedstock does not contain nitrogen, the product hydrogen purity for optimum plant investment is in the range 97-98 vol-%. Higher purities can be achieved at the expense of extra investment and operating costs: pressure swing adsorption (PSA) is used for this purpose. Low-pressure tail gas, containing main impurities, unconverted methane and hydrogen slip is used as fuel for the fired heater to reduce the external fuel request, and associated carbon emissions.
SMR plants are typically sized between 5,000 and 200,000 Nm3/h and are utilised for nearly the 50% of the world’s hydrogen demand. The process is well known and widely applied in the MAIRE group, with the brand NX Reform™. This solution is widely applied at industrial scale to produce hydrogen with very high purity and at lower costs than other technologies. More than 60 hydrogen production units have been executed by KT (Rome) in the last 40 years. Plants have been designed and built for very high plant reliability (>99%) and with a turnaround of up to six years. Furthermore, several optimisations have been executed, from zero export steam solutions to tailored requirements on customer needs with the highest efficiency.
Autothermal reforming (ATR)
The (non-catalytic) partial oxidation of hydrocarbons was the major commercial route for hydrogen production for several decades in the middle of the last century3. It uses a controlled amount of oxygen to limit the oxidation reaction to the carbon monoxide production. Being based on oxidation, the involved reactions are strongly exothermic, producing a huge amount of thermal power to be used and recovered in the downstream steps.
The ATR combines non-catalytic partial oxidation and catalytic steam and CO2 reforming of natural gas in a single reactor. In this process, the hydrocarbon feed and superheated steam are mixed and preheated to about 600°C and then mixed with oxygen. The reagents ignite in a combustion chamber originating a sub-stoichiometric flame. Subsequently, the steam and CO2 reforming reactions occur inside a Ni-based catalytic bed located below the combustion chamber. By a proper adjustment of oxygen to carbon and steam to carbon ratios the partial combustion in the thermal zone supplies the heat for completing the subsequent endothermic reforming reactions. Fig. 2 shows a typical ATR block flow diagram.
Due to this combination, ATR has a very high energy integration, resulting in a thermal efficiency (calculated as enthalpy ratio between reformed gas and feedstock) of around 89%, instead of a typical 80% for tubular steam reforming. Furthermore, due to the absence of tubes, ATR can be operated at higher temperatures than SMR, leading to the minimisation of methane slip and a lower thermodynamic equilibrium approach also in the presence of sulphur catalyst poisoning.
Sometimes, ATR is also utilised as a “secondary reformer” (for lowering the CH4 residue) and it is placed after a primary SMR in some applications. In other applications, a gas-heated reformer (GHR) is added to the process to pre-heat and partially reform the natural gas feedstock before entering the primary ATR reformer. The integration of the GHR is typically preferred in the low carbon hydrogen compact configuration since the heat transfer within the GHR is convective rather than radiative, the required footprint of the GHR is much smaller than a conventional SMR.
Eventually, in hydrogen production by ATR, the following process stream is similar to SMR, with the WGS reactor before the hydrogen is cleaned by carbon capture and purified in the PSA.
ATR plants are typically sized for large capacity (>150,000 Nm3/h). In the MAIRE group portfolio, the ATR is also present with the brand NX AdWin® Hydrogen Suite. This technology leverages an autothermal reformer operating at high pressure (60+ barg), reducing the size with respect to conventional ATR. A robust proprietary reactor, proven reforming catalyst and a combustion zone properly designed are integrated in a well-established syngas production unit. Furthermore, this is combined with a reduction of external heat requirement from the furnace, which is fed with hydrogen only during normal operation.
Carbon dioxide is captured by a dedicated pre-combustion carbon capture unit, based on a specific cold methanol loop (CML). An overall capture rate higher than 98% is achieved with 40% less solvent circulation compared to a MDEA-based plant.
The steam/power production allows the implementation of a self-sufficient system, including the power demand of the air separation unit (ASU) for oxygen production. As a result of these features, hydrogen production cost by using NX AdWin® Hydrogen Suite is reduced by 10% with respect to conventional ATR.
Short contact time – catalytic partial oxidation (SCT-CPO)
The SCT-CPO technology is applied for producing syngas from different gaseous hydrocarbon sources and it constitutes an additional solution for improving some other technologies limitations4,5.
In this technology the oxidation reaction takes place over a catalyst to facilitate the partial oxidation of the hydrocarbon fuel at lower temperatures. The dedicated reactor utilises short contact time – catalytic partial oxidation (SCT-CPO) processes, where reactants and products remain inside the reaction zone for periods between 0.03 – 0.05 s, approximately 1/50 shorter than those of the residence time of the other synthesis gas production reactors. Since 1992 several scientific and technical literature documents and patents have been dedicated to the description of the SCT catalytic partial oxidation phenomena4. The SCT-CPO technology is included in the MAIRE portfolio under the NX CPO™ brand.
The proprietary reactor includes internal refractory layers, allowing it to operate in nearly adiabatic conditions, and it is designed to promote heterogeneous reactions by mixing the gaseous reactants and flowing them on extremely hot catalytic surfaces. Reactant molecules remain confined inside a thin solid−gas interphase zone surrounding the hot catalytic particles for a short contact time at temperatures that can reach 1,200°C. The high-temperature environment and the heterogeneous catalysis favour the formation of partial oxidation reaction products, limiting the contribution of the total oxidation reactions that mainly occur at the beginning of the catalytic bed. Moreover, the very high surface temperatures inhibit catalyst deactivation phenomena related to chemical poison effects.
For these reasons, this chemical process can be carried out in very small reactors, having a very high flexibility towards reactant flow variations. This means that the reactor and the catalyst volumes are reduced by two orders of magnitude with respect to other syngas production technologies, without associating an increase in the technology complexity. This allows the construction of modular pre-built and skid-mounted plant units that can be transported and hooked up to utilisation sites, with a drastic reduction of on-site activities in remote and/or offshore contexts.
Fig. 3 shows a typical SCT-CPO block flow diagram.
Due to the presence of a specific catalyst, the carbon feedstock can be fed to the reactor at temperatures in the range of 300-400°C. These values are considerably lower than the requirements for SMR and ATR, leading to the possibility of preheating the feedstock with a feed-effluent heat exchanger, recovering the power generated by the exothermic reactions. This offers the opportunity to avoid the fired heater, which is a source of additional CO2 emissions. Therefore, a single source of CO2 is present in the process scheme, easily removable with pre-combustion carbon capture facilities.
Also for NX CPO™, the treatments for syngas purification to hydrogen are similar to other technologies, removing gradually CO (through WGS), H2O (through condensation), CO2 (through CC), and CH4 and traces of other impurities (through PSA). A specific characteristic of the technology is the possibility to reutilise the tail gas from the PSA directly as reactor feedstock, after a compression step. This further increases the overall process efficiency, reducing the carbon feedstock consumption per hydrogen produced.
The NX CPO™ technology has been intensively studied and applied during the last few years. Since the very early bench-scale experimentation4,5 and patent publications of the 1990s6,7, the long effort has led to industrial-scale applications up to capacities of 50-70,000 Nm3/h. Further capacity increases are under development.
Technology comparison
Two different analyses are carried out: the first without capturing the produced carbon dioxide, with the aim of comparing the technologies when grey hydrogen is produced. In this way, specific advantages related only to the specific technology can be observed.
In a second analysis, blue hydrogen production is evaluated, focusing on the beneficial integration of all the sub-units available in the process. Pre- and post-combustion amine-based carbon capture units have been used to reach the highest degree of decarbonisation for each technology.
In all the analysed cases, the feedstock is natural gas at grid pressure, therefore a dedicated compressor is used to reach the proper pressure. The hydrodesulphurisation step is also present to remove the sulphur amount in the feedstock.
Oxygen required for ATR and CPO cases is considered both as purchased or produced by a dedicated ASU. In this way, the advantage of decarbonised oxygen availability (i.e. presence of an electrolyser for green hydrogen production, specific industrial site cases) can be easily considered in the comparison
High pressure steam is produced and, when available, excess steam can be valorised. Dedicated demi-water supply and cooling medium are considered as utilities available at the site.
Both high and low-temperature WGS reactors are considered, as well as PSA to reach a hydrogen purity of 99.9 mol-%. The analysed parameters are:
• Methane consumption – calculated sum of carbon feedstock and fired heater fuel gas (when necessary).
- Electricity consumption – used for feedstock compression, tail gas recycling (when present), ASU (when present), and BFW pumping purpose.
- Production cost – calculated considering both capex and opex. Saudi Arabia is considered as a reference country for the price cost estimation.
- Emitted CO2 – final utilisation of captured carbon dioxide is not considered in the analysis. When oxygen is required, decarbonised oxygen is considered.
• Plant surface area – considering all the facilities to reach the required hydrogen purity.
Technology comparison for grey hydrogen production
For grey hydrogen production, three cases are analysed:
• conventional SMR;
• conventional ATR, with purchased oxygen;
• NX CPO™, with purchased oxygen. This is used as a base case for comparison purposes.
Table 1 summarises the main results.
The ATR shows the lowest methane consumption among the cases, but there are no huge differences in electricity consumption when oxygen is purchased.
All the cases produce high-pressure steam, which is used as a reactant and as a heating medium when possible. Excess of steam production is observed and valorised.
The production cost of hydrogen results in 15% higher for SMR and 30% higher for ATR with respect to NX CPO™, considering both capex and 10 years of opex.
In grey hydrogen, with elevated purity, all the carbon available in the feedstock is transformed into carbon dioxide, therefore, without capturing the produced carbon dioxide, the emissions to the atmosphere are intrinsically related to the feedstock consumption.
As previously reported, NX CPO™ is strongly compact and does not need a fired heater resulting in a lower surface area, as shown also by the size comparison between SMR and NX CPO reactors (Fig. 4).
Technology comparison in blue hydrogen production
For blue hydrogen production, five cases are analysed:
• Conventional SMR with pre-combsution carbon capture: Flue gases from fired
heaters are not treated and emitted to the atmosphere.
• Conventional SMR with pre- and post-combustion CC: A dedicated post-combustion carbon capture unit is mandatory for SMR to reach a decarbonisation degree higher than 85%.
• Conventional ATR with purchased oxygen and pre-combsution CC:
- NX CPO™ with oxygen production through a dedicated ASU and pre-combustion CC.
- NX CPO™ with purchased oxygen and pre-combustion CC: This is used as the base case for comparison purposes.
Table 2 summarises the main results.
A reduction of methane consumption, mainly due to the reutilisation of tail gas as feedstock, is observed in blue hydrogen produced by NX CPO™. In this way the overall carbon efficiency of the process increases, leading to extremely low emissions (purge gas to avoid inert gas accumulation).
Differently, an increase in methane consumption is observed in the case of SMR with Pre and Post Combustion CC. The reason is related to the steam balance: post-combustion CC requires a significant amount of low-pressure steam for the solvent regeneration, which can be produced only by increasing the fired heater generated power, and therefore the fuel gas consumption.
The presence of ASU strongly increases electricity consumption (observed for both ATR and CPO). However, ASU installation or oxygen purchase are considered equivalent to the production cost bases used for the study (i.e. electricity and oxygen costs in Saudi Arabia).
As a result of the study, the hydrogen production cost is significantly lower for NX CPO™ than other technologies when integrated with the CC facility. This very competitive price is essentially due to a better energy integration, which leads to low methane consumption, and low capex associated with the technology.
The strong reduction in carbon footprint by using ATR and CPO is conserved also when integrated with carbon capture.
Fig. 5 presents the comparison results regarding the degree of decarbonisation. The NX CPO™ and ATR technologies for blue hydrogen production demonstrate a significant reduction in CO2 emissions, capturing 98-99% of total CO2.
In contrast, pre-combustion carbon capture on SMR captures approximately 60% of CO2 (up to 85% with special configuration). To achieve high levels of CO2 capture (>85%), SMR would require post-combustion carbon capture, which involves very high operational and capital expenditures.
Conclusions
The decarbonising hydrogen production is a complex task and requires a context-specific approach. The different technology solutions allow various degrees of efficiency, carbon capture capabilities, and costs depending on the scale of production and specific operational conditions.
In grey hydrogen production, conventional ATR has the minimum methane consumption, resulting in higher process efficiency and low carbon emission. Therefore, it is generally advised for large-scale hydrogen production. Considering the geographical context used for comparison, NX CPO™ shows the lowest cost for construction and ten years of production, although its limited application in hydrogen production at comparable scales with SMR and ATR.
Despite the specific analysis performed, SMR is the most widely used technology worldwide in the range of 5 to 200 Nm3/h of hydrogen production, which is the typical requirement in the oil and gas and chemical production sectors.
The picture slightly changes when carbon capture is associated to blue hydrogen production. Due to a lower feedstock temperature required for the reaction, NX CPO™ operates without the need for an external furnace, thereby preventing flue gas generation and emission. Furthermore, NX CPO™ can more effectively re-utilise the CO2-free tail gas produced during the hydrogen upgrading, recycling it as additional reactor feedstock and reducing the overall methane consumption.
In the ATR technology, the external furnace is needed only for feedstock preheating because of the autothermal conditions in the reactor. This lets PSA tail gas be used as fuel without extra external fuel, strongly reducing the CO2 amount in the flue gas emissions. Thus, decarbonisation levels over 95% can easily be achieved with ATR and NX CPO™. In contrast, SMR requires high consumptions and costs due to the need for carbon capture post-combustion to exceed 85% decarbonisation.
In conclusion, the technology choice for blue hydrogen production must be guided by a comprehensive evaluation of key performance indicators such as the production capacity and the degree of decarbonisation required (see Fig. 6).
NX CPO™ emerges as a highly competitive technology for small to medium capacities (e.g. up to 50,000 Nm3/h) due to its superior energy integration and reduced methane consumption when associated with carbon capture facilities.
The compact design allows low capital cost and high flexibility, with the lowest CO2 emissions.
For medium capacities (e.g. up to 200,000 Nm3/h), NX Reform™ blue hydrogen, based on SMR, is the most applied technology, with a maximum decarbonisation degree of 85%.
While for large-scale production (e.g. higher than 150,000 Nm3/h), the NX AdWin® Hydrogen Suite, based on ATR, offers a robust solution with optimal performance.
There is not a sole technological solution to cover all variables and requirements. As the industry progresses towards net-zero emissions, the findings of this study underline the importance of tailored solutions in achieving sustainable and economically viable blue hydrogen production.
References