Fertilizer International 526 May-Jun 2025
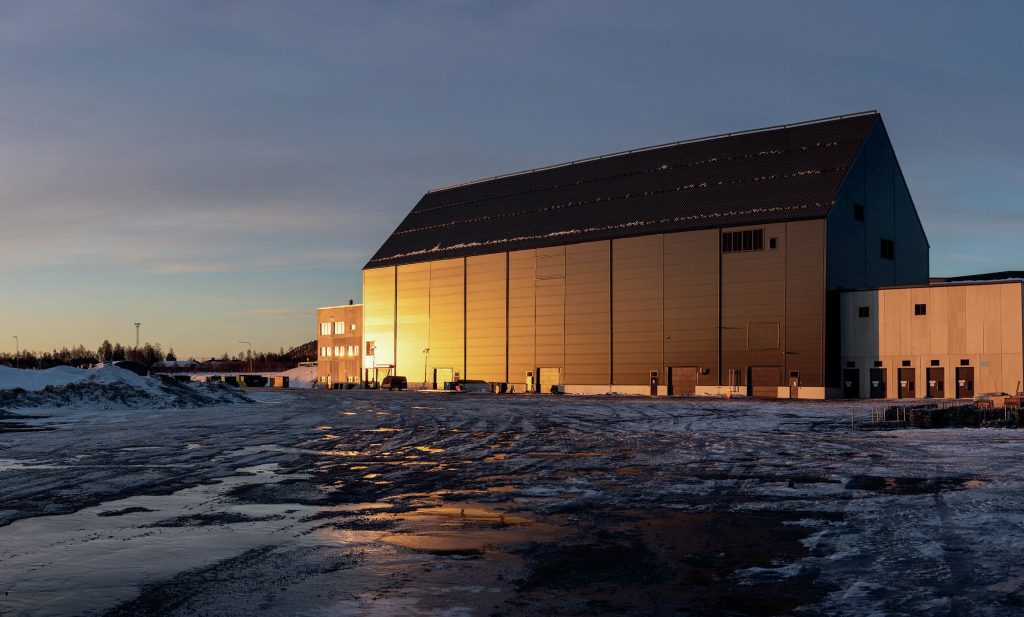
2 May 2025
Cinis Fertilizer – pioneering the circular economy
EUROPEAN POTASH PRODUCERS
Cinis Fertilizer – pioneering the circular economy
In this exclusive interview, Fertilizer International talks with Jakob Liedberg, the CEO of Cinis Fertilizer, a recent entrant to the European potassium sulphate (SOP) market, ahead of the International Fertilizer Association’s Annual Conference in Monaco in mid-May.
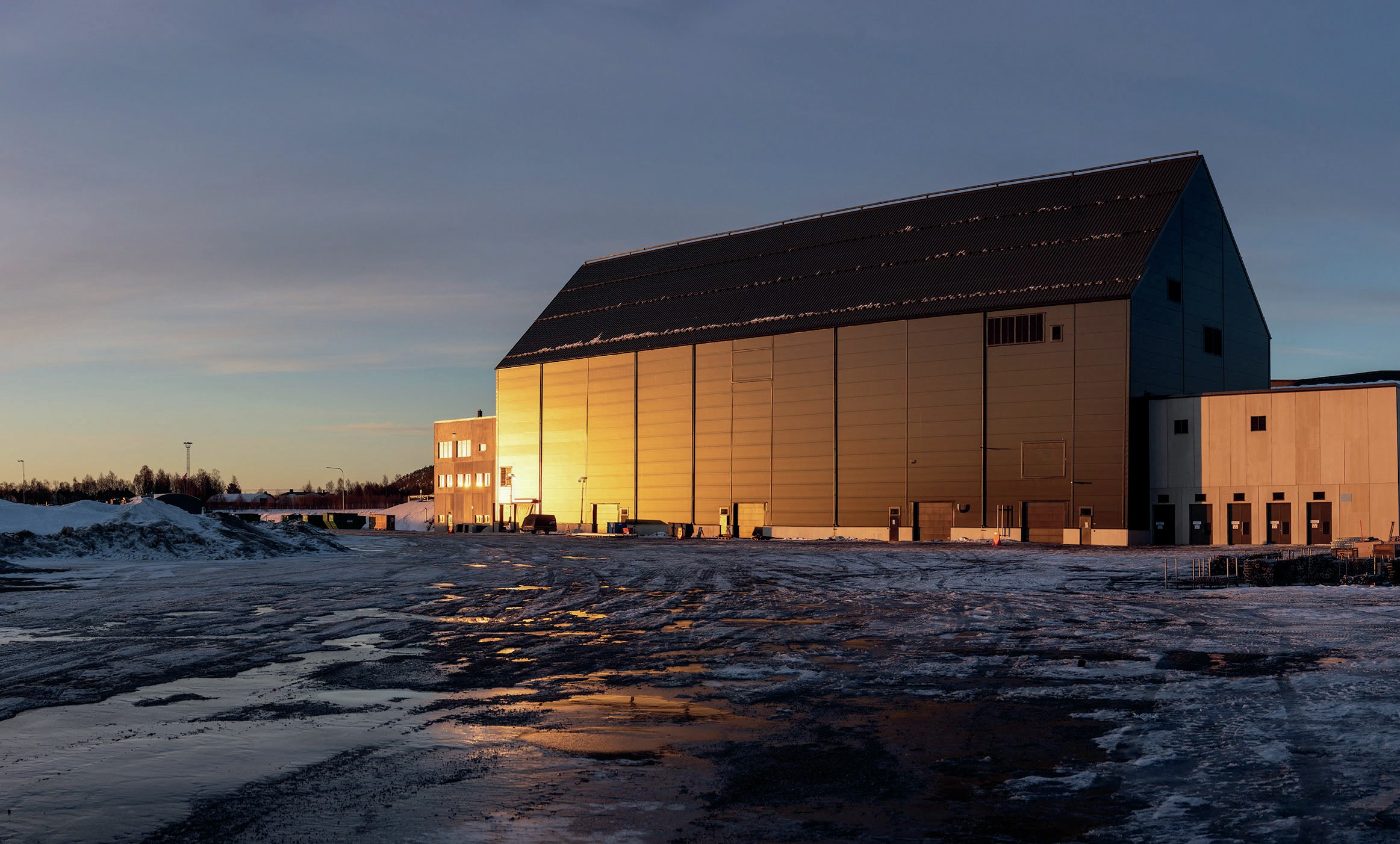
Background
Cinis Fertilizer started production at its inaugural 100,000 t/a capacity potassium sulphate (SOP) plant at Örnsköldsvik, Köpmanholmen, Sweden, in May 2024. The plant can also produce 65,000 t/a of sodium chloride as a co-product. The plant has taken around 15 months to construct following groundbreaking at the site in February 2023.
This Örnsköldsvik plant is powered by fossil-free energy and can upcycle industrial residues – including sodium sulphate (Na2SO4) from electric car battery manufacturing and ashes from pulp mills – to produce SOP using patented technology based on the glaserite process. This first-of-its-kind production method uses half as much energy as conventional SOP production, according to Cinis.
The company quotes an energy consumption of 50,000 MWh for its production process versus 100,000 MWh for conventional manufacture, based on a 100,000 tonnes of SOP production. The result, says Cinis, “is a fertilizer with low carbon footprint, a unique and circular contribution enabling sustainable agriculture”.
The SOP obtained at Örnsköldsvik is sold and marketed by Van Iperen International as GreenSwitch Potassium Sulphate, a pure and fully water-soluble SOP product, with significantly reduced CO2 emissions, approximately 300 kg CO2 per tonne of SOP produced, that is suitable for foliar and fertigation applications.
Cinis has positioned itself as an offtaker of sodium sulphate waste from battery makers. Originally, the company had secured a 200,000 t/a offtake agreement with Northvolt, for example, for the sodium sulphate generated from precursor cathode active material (pCAM) production at the proposed Skellefteå battery manufacturing plant in Sweden. These plans were dashed, however, when Northvolt filed for bankruptcy in March this year and its plans to transform a closed paper mill in Sweden into a new gigafactory collapsed.
More positively, in an agreement with Ragn-Sells Group signed in September last year, Cinis is being paid to handle and upcycle sodium sulphate generated as industrial residue. Receiving payments for waste-derived sodium sulphate underscores the value of the company’s circular business model, according to Cinis.
In the US, Cinis also has a ten-year supply agreement in place with Ascend Elements for a planned SOP plant in Hopkinsville, Kentucky. This commits Ascend Elements to supplying up to 240,000 t/a of sodium sulphate from an under-construction battery materials manufacturing plant in Hopkinsville, starting in 2026.
In February, Cinis Fertilizer signed a cooperation agreement with WA3RM to develop and finance circular economy projects, starting with the planned Hopkinsville SOP production plant in the US. Malmo-headquartered WA3RM helps to fund and bring to market industrial-scale projects that reuse waste materials and energy.
Fertilizer International got together with Jakob Liedberg, Cinis Fertilizer’s CEO, in March to talk about the company’s pioneering approach to fertilizer manufacturing and its commitment to low-carbon production technology, industrial symbiosis and capturing nutrients from waste streams.
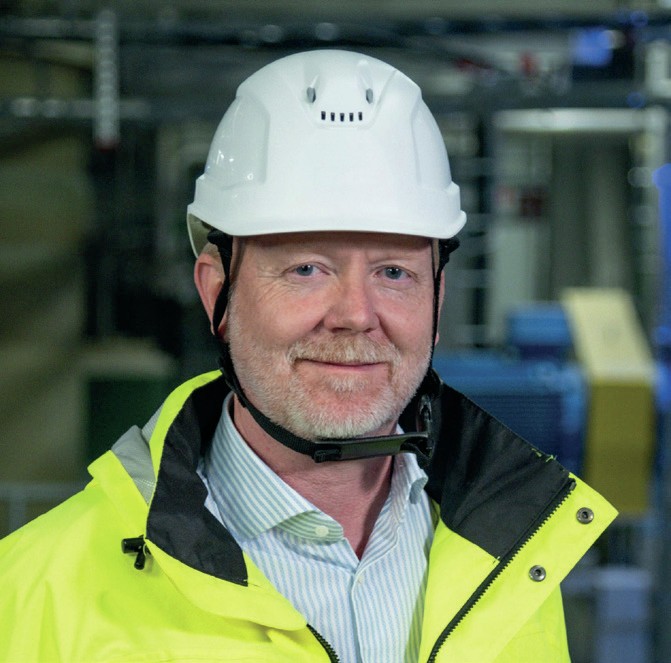
European market game changer
It’s a pleasure speaking, Jakob. Cinis Fertilizer is close to celebrating its first year as a European SOP producer. Could you share with our readers the story of how the company started and take us on the journey from the early days of the business to its market entry last summer?
“In 2010, I started working with the Swedish pulp industry on an environmental project to reduce cadmium emissions into the Baltic. That’s actually where the idea to combine sodium sulphate together with potassium chloride (MOP) to produce potassium sulphate (SOP) first came from – seeing how this industry, at that time, disposed of a lot of sodium sulphate in wastewater.
“The solution to pollution is dilution – that’s how the chemical industry worked in the old days. If it’s an effluent disposed to a drain, you dilute and stay below certain approved levels.
“The moment when it really changed from just a concept to become reality – into something tangible that we could launch as a company – was in 2022. That was when the electric battery industry started emerging in Europe, especially [our business] connecting with [the electric vehicle (EV) battery manufacturer] Northvolt, and with that a much larger sodium sulphate effluent problem from precursor Cathode Active Material (pCAM) production.
“That was the turning point for us, when Cinis really took off, as we could build a company and launch it on the stock market to bring in equity and debt finance. From then on, it went really fast.
“A year after, in February 2023, we had the groundbreaking [to start construction at Örnsköldsvik] and 15 months later this greenfield project was [complete and] ready to start up. Then, three months on from that, we actually delivered the first SOP product. As an engineer, I’ve never actually experienced a faster paced project, to be honest.
“Things did not progress [exactly] as planned. So, today, we don’t rely on [the supply of] sodium sulphate from Northvolt. Right now, the [Örnsköldsvik] plant is producing potassium sulphate based on sodium sulphate primarily sourced [commercially] from industry and waste streams supplied by Ragn-Sells. But the plan is still to phase this out and replace it with sodium sulphate from industrial waste or by-product materials.
“I see a [great] fit for our technology in the chemical industry’s future value chain. Our situation right now is a temporary phase – because [only] we can produce SOP in a context totally disconnected from the oil & gas industry.
Disruptive market entrant
Cinis clearly has a very different, innovative and disruptive business model, compared to a conventional SOP producer. How has the company been able to profitably produce high quality SOP with a low carbon footprint using a novel process from industrial residues?
“This is kind of a funny story. Originally, because the idea came from pulp industry, the first thing that dawned on me was that producing SOP using sodium sulphate and MOP, the glaserite process, must be a new invention.
“But I then realised this process stems from the 1950s and, as with many things, had already have been discovered a long time ago. In the 1980s, I think, there were two commercial plants operating in the world producing SOP via the glaserite route.
“The reason why the glaserite process did not get a foothold previously is because, traditionally, oil & gas by-products needed to find their way into the chemical value chain. [For example,] huge amounts of sulphur are produced when you de-sulphurise oil & gas and, of course, all that sulphur finds its way into sulphuric acid.
“For a 100 years, SOP production via the Mannheim process has been one outlet for this sulphuric acid. That’s why I believe the technology was chosen as the standard way for producing SOP – and also because SOP doesn’t exist naturally in many parts of the world.
“Mannheim production of SOP is a natural choice if you have a lot of energy from cheap oil & gas and you have fossil fuel industry by-products you need to find an outlet for. But the industry is changing and, to fight global warming, we’re going to consume less fossil fuels in the future. So, we need to find ways of designing chemical production plants that do not rely on oil & gas with electricity as the energy input instead.
“We have to rethink how we produce chemicals and how we source input materials to increase circularity – that means using what we wasted yesterday as a resource today. That’s really the whole idea behind Cinis Fertilizer and our plan to utilise waste resources, such as those from the pulp industry that are traditionally sent down the drain.”
A circular economy pioneer
The Örnsköldsvik production plant is a rare example of industrial symbiosis in action. Has it proved difficult to successfully secure the necessary raw materials and sourcing agreements needed to help Cinis turn its circular economy principles into a reality?
“First of all, you’re spot on. Sourcing and offtake agreements [with Van Iperen, K+S, Ragn-Sells, Ascend Elements and others] are actually crucial because without these partnerships with established companies I don’t think our industrial project would exist, to be honest.
“They validated our concept and reduced the project risk for investors. The offtake with Van Iperen, for example, was a really crucial step and a very important agreement. It showed investors, who in fairness don’t know too much about the industry, that there was an outlet for our production and someone ready to put it on the market from day one.
“I’ve known the managing director of Van Iperen for more than 10 years. The offtake agreement means we don’t need to do the sales and marketing ourselves – building a sales force, our own brand and finding customers – Van Iperen do all that for us. Then, of course, K+S is a great partner to have for sourcing raw materials. A giant in the potash industry with lots of experience from production to markets, you name it. These collaborations truly benefit all parties, something we appreciate a lot.
“In the case of Ragn-Sells, we charge gate fees, which is a normal way of operating in the waste recycling business, because we’re actually a solution to a [disposal] problem. There is a value attached to this waste, but you don’t just get rid of it for nothing. [Instead,] it actually comes with a cost and industry is prepared to pay that.
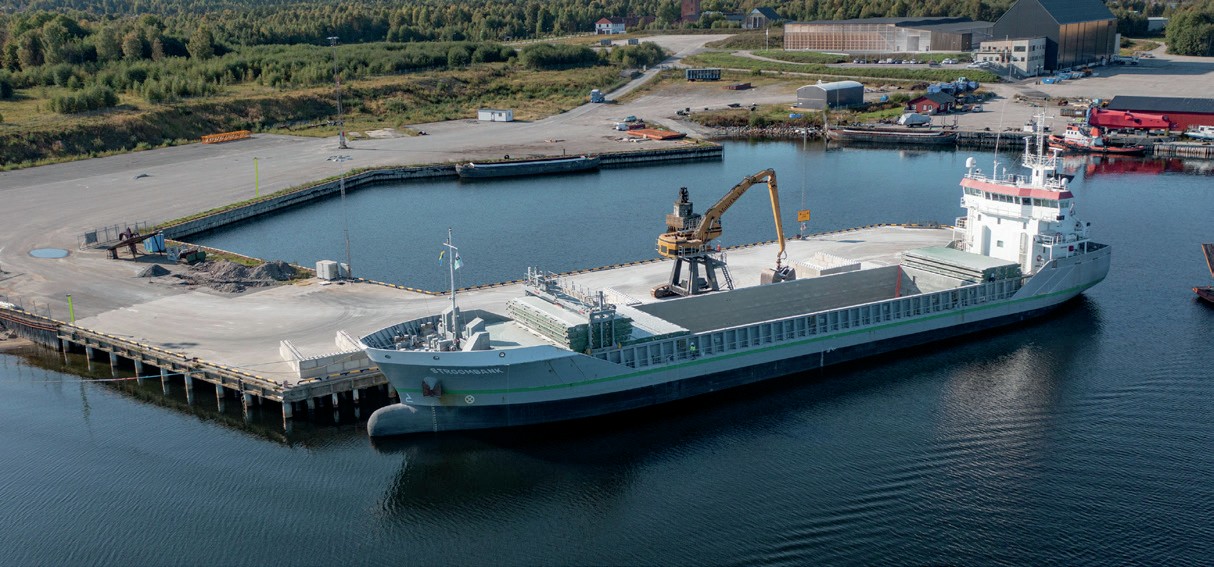
“We like the agreement with Ragn-Sell because it’s in both our interests. They’re a recycling company focused on circularity and we can find solutions for their different waste streams – that’s industrial symbiosis.”
“Yes, it’s a sad story with Northvolt going bankrupt in Sweden at the moment. [Originally,] the sodium sulphate supply agreements we had with them was an important piece of the puzzle to derisk the project. But if you look outside of Sweden, in Europe, Canada, US, Asia, there are lots of other [pCAM] projects still going.
“Right now, for example, we’re planning our next production plant [at Hopkinsville, Kentucky] in the US together with [battery materials manufacturer] Ascend Elements. It’s exactly the same setup [as Northvolt]. We’re working with Ascend to address the same [pCAM] problem – lots of sodium sulphate by-product that needs to find a use somewhere.
“We can also be an enabler – a way to offload an environmental problem that otherwise could be blocking a project. Because if you present a project application with a solution to a problem, then it often gets granted. We’ve actually seen that happen with BASF, a company we’re working with [on their pCAM plant project at Harjavalta in Finland].
“BASF are a chemical industry giant producing more or less everything that you can think of. But a really circular company too, because their whole business model is built on both primary products and by-products.”
A deep partnership with shared values
How important is Van Iperen International to the story of Cinis Fertilizer and the successful start-up of your first SOP plant? Is it true to say there’s very much a shared ethos on sustainability, the circular economy and net zero?
“Absolutely, Van Iperen is a fantastic company and an excellent partner. They’re actively pushing and driving the switch and change to low-carbon footprint products in the fertilizer industry.
“Our SOP offers clients a lower carbon footprint, if you compare it with Mannheim production and the majority of SOP supply in Europe, because our plant runs entirely on fossil-free electricity. We reduce the carbon footprint by roughly [50% to] 300 kilograms of CO2 per tonne of SOP. This helps our [agricultural] end-users reduce their own carbon footprint – which in the end is what it’s all about.
“We have an alignment of interest with Van Iperen. We want to produce as much low-carbon SOP as we can so they can put it on the market. They have already sold SOP we’ve produced – under their GreenSwitch SOP brand name – in more than 25 countries. In the year-to-date, that’s roughly 40,000 tonnes at least.
The first of many? – projects in the pipeline
Cinis has a project to build a 300,000 t/a capacity SOP production plant in Hopkinsville, Kentucky, in the US. Could you update our readers on the company’s expansion plans please?
“Yes, US company Ascend Elements are building a large pCAM/‘black mass’ recycling facility in Hopkinsville Kentucky. We have a supply agreement with them for handling all of their sodium sulphate waste. It’s actually a three times bigger project. So, with the projected amounts coming out of that facility, we can actually produce three times [the amount of SOP] compared to what we do at our plant in Sweden. The rough timeline for the start of the production at Hopkinsville is the end of 2026 or perhaps early 2027.
“Our cooperation with WA3RM, announced a few weeks ago, is one way in which we’re looking at how to finance future projects. WA3RM did a huge 100,000 square metre greenhouse tomato farming project in Sweden [reusing industrial waste heat], supplying around a tenth of the total domestic tomato market.
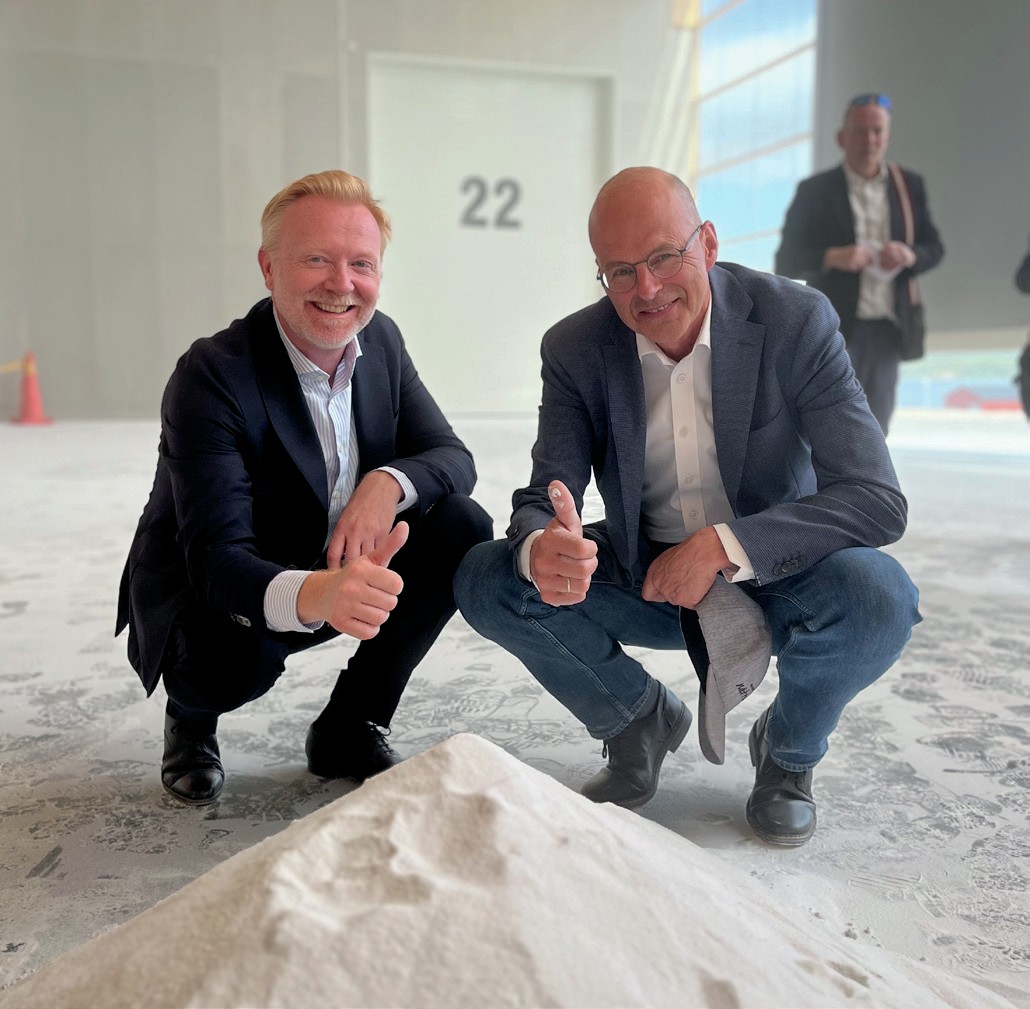
“WA3RM’s founders actually came from the European Spallation Source [an atomic research centre in Lund] with the idea, basically, of reusing waste heat and waste resources to increase circularity on a big scale. They have an interesting funding model – basically off balance sheet financing – that avoids bringing in equity to finance projects. It’s just one way we’re looking at executing and financing new projects in future.
Lessons from inaugural production
Have there been clear lessons for Cinis from commencing and ramping-up production at its inaugural plant – ones that can be applied to the other projects in the pipeline?
“Our technology provider is Evatherm a Swiss engineering company. If you look at this industry, you find a handful of companies that know this business, Veolia, GEA, K-UTEC. But we ended up going with Evatherm and recently set out a new plan to ramp up the Örnsköldsvik plant in 2025 and get it running close to nameplate capacity of 100,000 tonnes SOP output per year.
“We’ve learned a lot. There are some things that you totally cannot plan for or anticipate – for example, bad luck like the power outage in summer of 2024 which set us back quite a bit. But we’ve overcome that and are constantly increasing our output.
“I don’t know any industrial project where the execution goes exactly to plan. So, obviously, like any other project, we’ve had challenges to overcome. We are producing at high capacity now, considering nominal capacity is 100,000 tonnes, and already reaching quite high output levels.
“We’re a totally new company with a plant run by 30 new employees and they’ve done a tremendous job at learning and just operating the SOP plant. I could not be more pleased with that.”