Sulphur 418 May-Jun 2025
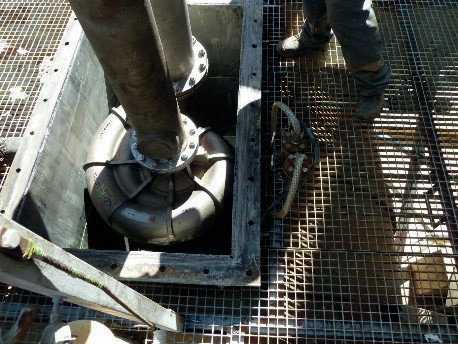
1 May 2025
A sulphuric acid pump for high-temperature applications
SULPHURIC ACID PUMPS
A sulphuric acid pump for high-temperature applications
The GVRN sulphuric acid pump has been established in the market for many years. Rheinhütte Pumpen has further developed this special pump so it can also be used in high-temperature applications such as in heat recovery systems.
Sulphuric acid is one of the most important basic chemicals in numerous global industries. More than 200 million tons are produced worldwide every year. However, production causes enormous amounts of CO2, which pollutes the environment, and valuable resources, such as the waste heat generated in the process, are wasted. Heat recovery systems (HRS), which utilise the highly exothermic processes in the production of sulphuric acid, provide a remedy. These systems can be integrated into sulphuric acid plants and adapted to the respective requirements of the plant. The aim is to recover waste heat in the form of high and medium pressure steam. Users can use this process steam for other processes or to generate electricity. In a typical process cycle for sulphuric acid production, around 60% of the total energy can be used and 35 to 40% is available as low-level heat in the acid cooler system. The HRS comes into play with this weak heat in order to utilise it – which would otherwise end up in the atmosphere or in the cooling water system. This means that users can utilise almost all of the waste heat by using a heat recovery system. The challenge for pump manufacturers in this application lies in the highly aggressive and extreme temperature of the acid as well as the size and efficiency (>80 to 85%) of the pumps.
In 2013, Rheinhütte Pumpen started with HRS prototypes for a sulphuric acid plant of a European fertilizer manufacturer. Existing pumps from another manufacturer were to be replaced. Vertical pumps were required that could pump 99.5% sulphuric acid at 224°C. The GVRN pump was selected, which had already proven itself in sulphuric acid plants for decades. The only difference to the previous projects was the extremely high temperature of the sulphuric acid. However, the special material previously used in sulphuric acid proved to be resistant even at these temperatures.
In addition to the specific choice of materials, other design features are also crucial in this application. One key factor is the sealing of the pump. Single-acting, gas-lubricated mechanical seals in cartridge design with a throttle on the tank side are the optimum choice for vertical HRS pumps. The throttle reduces the sealing gas consumption by creating a gas cushion. This protects the seal and minimises the leakage of the container atmosphere. The gas also keeps unwanted atmospheric oxygen or humidity away from the gas seal. Alternatively, a stuffing box packing can be used in vertical pumps that operate at lower temperatures. Both sealing variants were already tried and tested sealing variants of the GVRN.
There was a need to optimise the hydraulics and design in order to avoid crevice corrosion, for example. Due to the highly corrosive properties of the medium, screw connections were avoided wherever possible. Screw connections that are located in the medium are fitted with cap nuts and additional O-rings. The flanges are cast onto the pipes instead of bolted to prevent crevice corrosion. The pumps also have a double volute, which greatly reduces the radial loads, resulting in less stress on the shaft and rolling and plain bearings. In order to minimise partial load recirculation (reduction of NPSHr), the suction covers have been fitted with swirl breakers.
In order to cover a wide performance range, the high-temperature version of this series has been developed in several sizes. Five sizes are already available and more will be released this year.
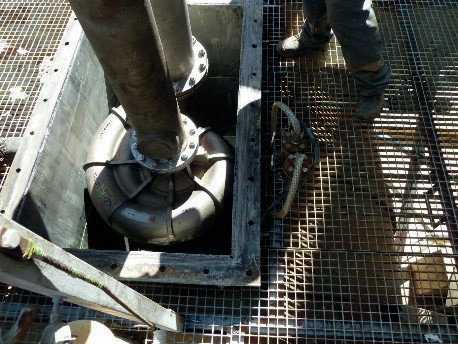