Fertilizer International 525 Mar-Apr 2025
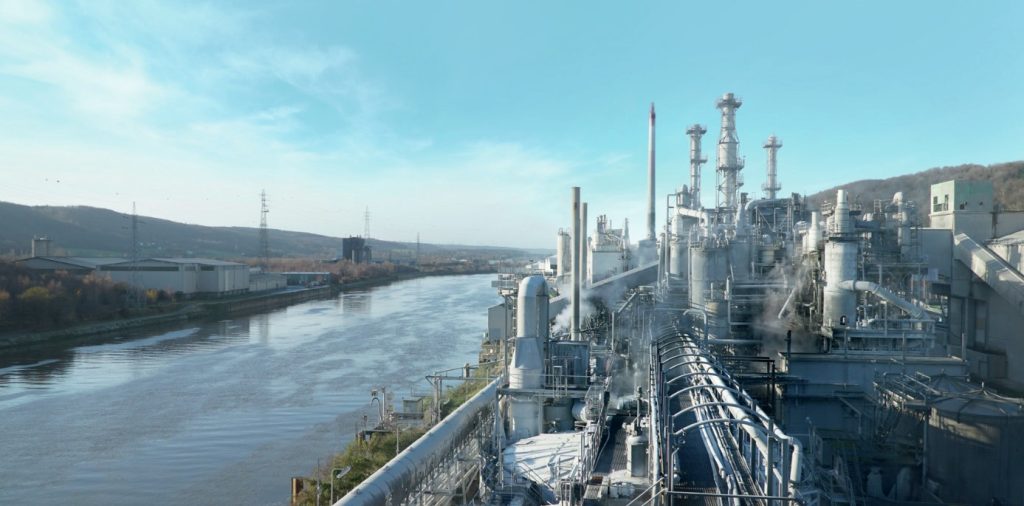
18 March 2025
Optimising phosphoric acid supply chains
PHOSPHATE TECHNOLOGY
Optimising phosphoric acid supply chains
The dicalcium phosphate (DCP) generated by chemical beneficiation offers distinct advantages as a phosphoric acid feedstock. Prayon’s Marc Sonveaux outlines how chemical beneficiation can transform current industry supply chains – and provide phosphate producers with an opportunity to reduce waste generation and improve phosphoric acid purity, while maintaining global competitiveness.
Phosphoric acid production – a global perspective
Phosphoric acid is a vital industrial chemical. Its production from naturally-occurring phosphate rock – mined in various regions across the globe – typically follows one of two pathways:
• Integrated production: the phosphate rock is processed into phosphoric acid in a production complex located near the mining site.
• Non-integrated production: phosphate rock is sold on the merchant market and delivered to a different location or country where its conversion to phosphoric acid then occurs.
Prayon’s well-known non-integrated phosphate complex at Engis in Belgium (see photo) is a good example of this supply chain model. It consumes phosphate rock feedstock imported from different locations and then converts this into phosphoric acid. Specific to this plant – thanks to Prayon’s CPP phosphoric acid process – is the generation of a high-quality gypsum co-product usable in plaster production. Crucially, achieving this virtuous combination (a sophisticated, efficient process that provides a clean, marketable co-product) relies on the quality of the phosphate rock feedstock.
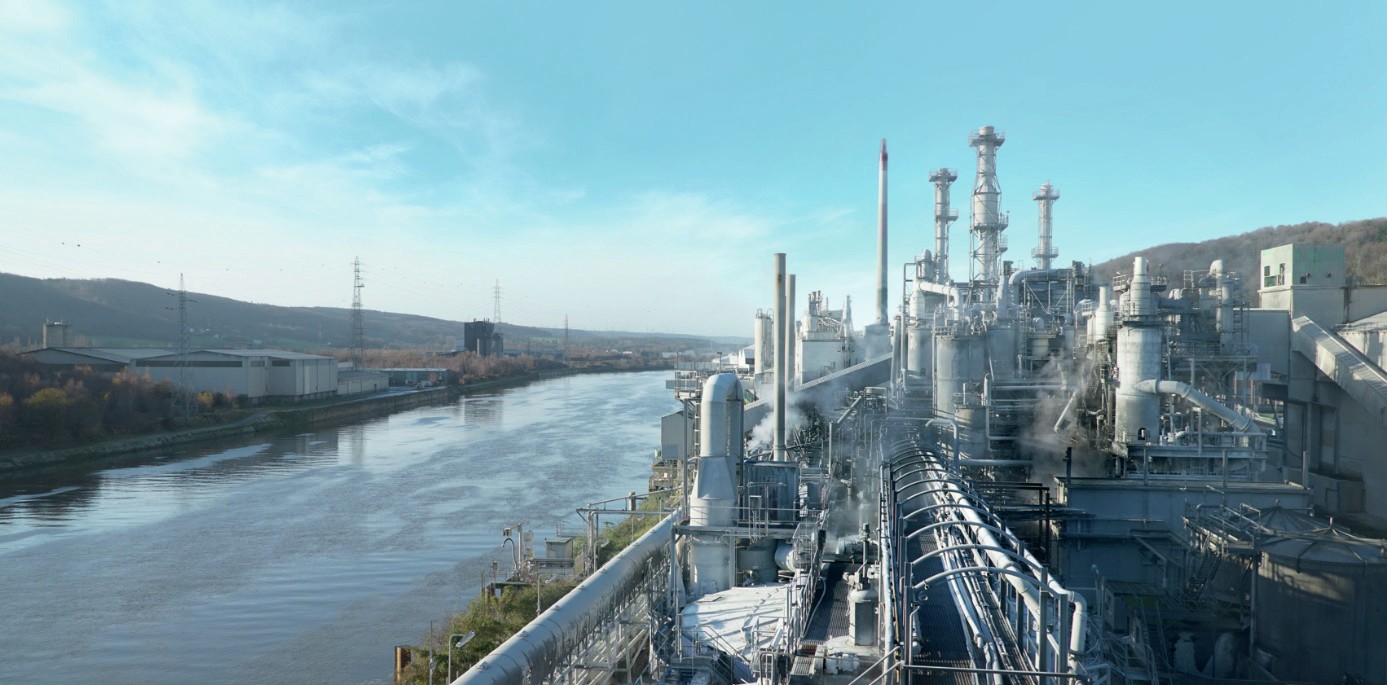
Let’s examine another emerging case of non-integrated production – this time from the United States. Historically, Florida has been a major producer of high-grade phosphate rock. However, as the quality of US domestic reserves has gradually declined, the state’s producers have increasingly looked for alternative rock sources as part of their buying strategy. This has resulted in increasing phosphate rock imports from South America where vast deposits exist, in Peru or Brazil, for example.
These non-domestic phosphate feedstocks are usually beneficiated close to the mine and are then transported to the US as rock concentrates. These typically have a 30-32% P2O5 content.
Imported rock – processing challenges
As a natural resource, phosphate rock inevitably contains various unwanted ‘gangue’ elements as well the desired and economically valuable P2O5 content. These impurities introduce the following complications and drawbacks during phosphoric acid production:
• Calcium (Ca): High calcium content leads to the generation of more phosphogypsum, a by-product that poses significant disposal challenges.
• Silicates (SiO2): These dilute P2O5 concentration, increasing per tonne P2O5 transportation costs and potentially affecting process efficiency.
• Heavy metals (Cd, Pb, As, etc.): These are elements of concern, due to their environmental and human risks, and partition/accumulate in either the phosphogypsum by-product or the main phosphoric acid product.
• Magnesium (Mg), aluminium (Al), and iron (Fe): These so-called minor elements are deleterious to phosphoric acid production and operational efficiency due to their negative effects on viscosity (Mg), yield (Fe) and potentially crystallisation, filtration and acid concentration.
• Organic matter: Its presence causes foaming issues and affects the purity of phosphoric acid and gypsum.
• Radionuclides (U, Th, etc.): The presence of radionuclides can limit the potential applications of phosphogypsum by making it unsuitable for use in the construction industry.
Phosphate rock handling and transport logistics are other factors that can be problematic for the supply chain. Imported phosphate rock typically requires beneficiation to generate a phosphate rock concentrate that meets the necessary quality standards for phosphoric acid production (P2O5 content of around 30%). This beneficiation process requires substantial investment in utilities while the use of chemical reagents add to costs.
Dreaming of the ideal phosphate source
For a phosphoric acid plant to operate sustainably at its maximum efficiency, what would the ideal phosphate rock feedstock look like? Here are some suggestions:
• Highest possible P2O5 content: Consumption of better quality rock – with a higher P2O5 concentration – will lower transportation costs and increase production efficiency, while reducing phosphate rock consumption and the usage of utilities.
• Low Ca/P ratio: Minimising calcium content, relative to P2O5, helps reduce both sulphuric acid consumption and gypsum generation.
• Low impurities/less gangue: Lower levels of unwanted elements improves both process efficiency and phosphogypsum quality, while reducing waste generation and process reagent/chemicals consumptions.
• Low radioactive content: Using a rock feedstock as free as possible from radionuclides allows the safe and versatile use of the phosphogypsum by-product in a variety of different end-uses.
• Optimal particle size: The phosphate rock concentrate should be fine enough for rapid and effective sulphuric acid digestion while avoiding excessive dust content.
• Cost-effective production: The phosphoric acid process step should limit or reduce overall phosphate fertilizer production costs.
Thankfully, finding such a perfect phosphate feedstock is neither a dream or a matter of luck – it is available now thanks to innovative chemical beneficiation technologies. These represent a major scientific advance in the beneficiation process.
Shift to global DCP-based supply chains?
Chemical beneficiation is one highly promising solution for overcoming the challenges of phosphate rock impurities – specifically when this produces a dicalcium phosphate (DCP) feedstock for the phosphoric acid process. Valuably, the chemical synthesis of DCP from lower-grade phosphate rock effectively removes most impurities, generating DCP as a superior alternative feedstock for phosphoric acid plants.
Prayon has developed two proprietary technologies for DCP synthesis:
• The GetMoreP process – based on sulphuric acid digestion of phosphate rock
• The Ecophos process – based on hydrochloric acid digestion (with the option to recycle HCl).
Prayon has developed both these technical solutions to maximise the benefits of using DCP as a phosphoric acid plant feedstock. This now makes it possible to implement efficient and cost-effective global supply chains based on DCP – via the following steps:
Firstly, at the phosphate rock mining site prior to transport to phosphoric acid plants:
• Extraction, crushing and grinding: Mined phosphate rock is reduced to between 0.5-1mm in size.
• Acid dissolution: Ground phosphate rock is dissolved in either dilute sulphuric acid (GetMoreP process) or hydrochloric acid (Ecophos process). The P2O5 enters solution while insoluble impurities are separated out.
• DCP precipitation: Calcium carbonate or lime is added to precipitate P2O5 as purified DCP.
Then, on arrival at the phosphoric acid plant:
• Feedstock substitution: Conventional phosphate rock feedstock is replaced with DCP to improve overall process efficiency.
Table 1 compares typical phosphate rock quality with that of a DCP feedstock generated by chemical beneficiation.
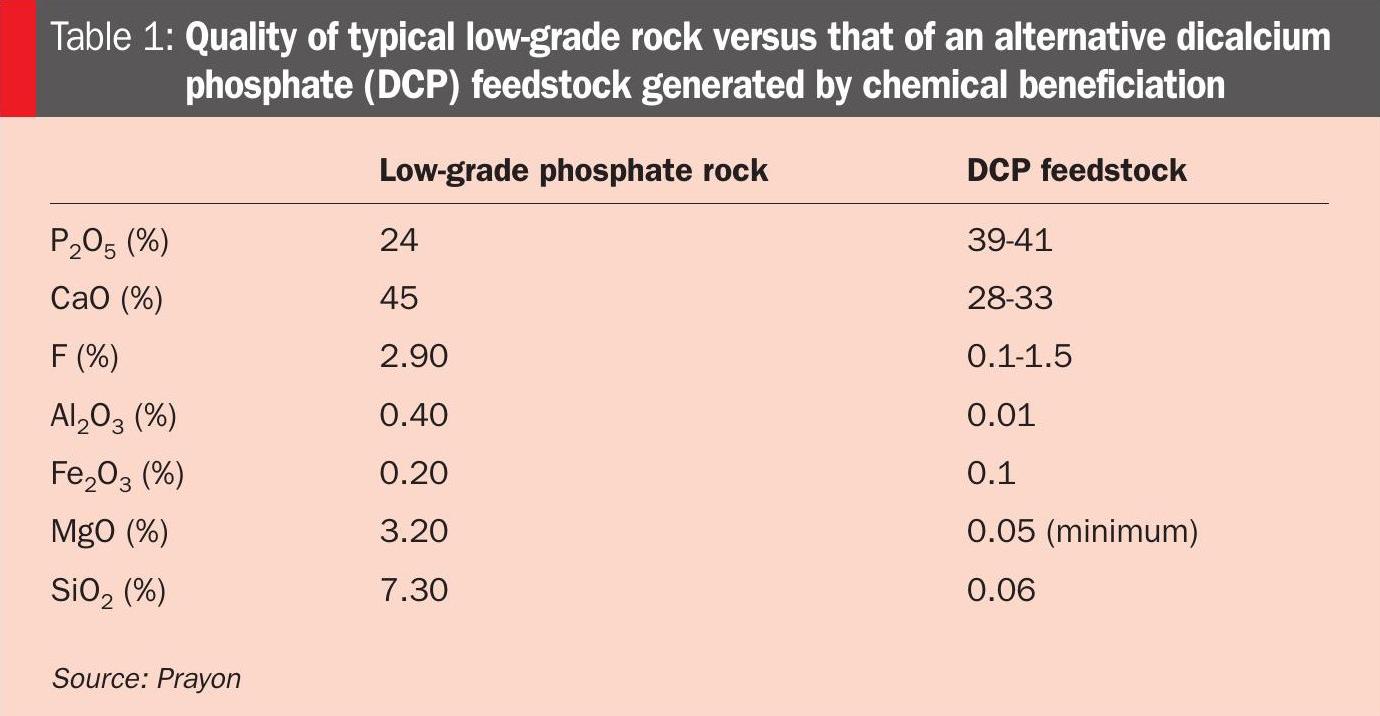
DCP feedstocks – advantages and challenges
While the use of DCP feedstock offers significant advantages, a number of challenges should also be addressed to maximise the profitability of this chemical beneficiation approach.
In terms of DCP’s advantages – versus low-grade phosphate rock – at the mine and during transportation:
• It reduces or eliminates the need for traditional beneficiation.
• Removes most impurities at the mining stage, reducing contamination risks in subsequent production stages.
• The lower grinding requirement saves on energy costs.
• Waste acid sources can be used in its production.
• Lower levels of impurities and higher DCP grade (38–45% P2O5 ) reduce transports costs per tonne of P2O5.
DCP also offers additional advantages at the phosphoric acid plant:
• Lower calcium-to-phosphate ratio: Reduces gypsum generation.
• Cleaner process: Produces purer phosphoric acid and cleaner gypsum.
• No more impure phosphogypsum: Generates clean gypsum instead.
• Non-radioactive gypsum by-product: Suitable for use in cement, plaster and plasterboard industries.
• Increases plant operating capacity: Lower sulphuric acid consumption and 50% less gypsum generation, combined with a higher phosphoric acid concentration, all result in higher plant capacity.
The DCP route also improves the overall global P2O5 yield of the process – from mining all the way through to phosphoric acid production (Figure 1).
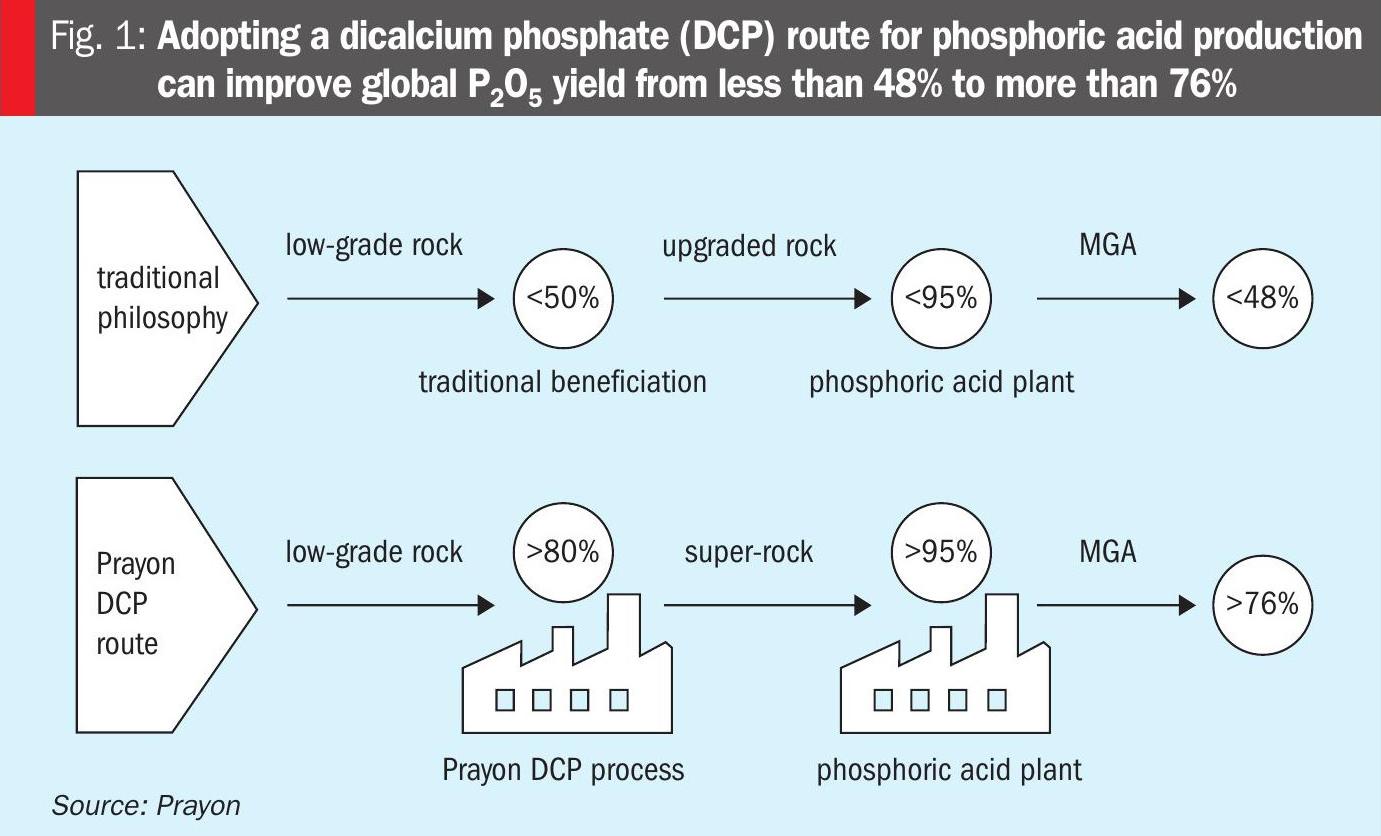
The main challenges of substituting DCP for low-grade phosphate rock are:
• It requires capital investment in chemical beneficiation plant.
• It involves additional utilities usage and chemicals consumption at the mining site.
• Impurities removed by chemical beneficiation require proper handling and disposal or options for re-use.
These points need to be clearly addressed during the plant feasibility phase.
Case-by-case considerations
Each individual phosphate chemical beneficiation project needs to be carefully investigated by assessing the following variables:
• Raw material costs.
• Project-specific phosphate rock characteristics (types and levels of impurities, reactivity, etc.).
• Sourcing and availability of the acid required for chemical beneficiation.
• Access to water, electricity, chemical reagents and other utilities.
• Options for storing or commercialising by-products.
• Geographic location and space constraints for setting up beneficiation plants.
“Chemical beneficiation provides phosphate producers with an opportunity to enhance sustainability, reduce waste generation, and improve phosphoric acid purity, while maintaining global competitiveness.”
Prayon, through its in-house expert team and partnerships with leading engineering contractors, can design, validate and implement tailormade project solutions. The company’s project services cover laboratory-scale validation, pilot and semi-industrial testing, economic feasibility studies, full-scale plant design, start-up support, and performance guarantees.
Conclusions
To secure the future of phosphoric acid production, the phosphate industry needs to address and overcome mounting challenges – including declining phosphate ore quality, rising beneficiation costs, and the need to improve its environmental footprint.
Additionally, import dependency for phosphate rock feedstocks is on the rise, both globally and more specifically in the US. Also, at a time when phosphate rock quality is in decline while fertilizer demand is growing, the cost and sustainability of traditional beneficiation methods are becoming less viable, in Prayon’s view.
The DCP-based chemical beneficiation approach presented in this article offers a forward-thinking alternative, offering both environmental and economic advantages, although admittedly requiring upfront investment. This innovative method provides phosphate producers with an opportunity to enhance their long-term sustainability, reduce waste generation, and improve phosphoric acid purity, while maintaining global competitiveness.
In Prayon’s view, embracing innovation by adopting new processing techniques – in response to regulatory pressures and rising global phosphate demand – will be crucial for the future resilience of the phosphate industry.
CRU Phosphates+Potash Expoconference 2025
Kevin De Bois of Prayon Technologies will be speaking on the use of innovative leaching technologies to address key phosphoric acid production challenges at the conference in Orlando on Wednesday 2 April at 09:00-09:30.