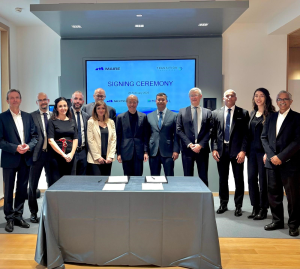
Press Release: NEXTCHEM (MAIRE) AWARDED A LICENSING CONTRACT
NEXTCHEM (MAIRE) AWARDED A LICENSING CONTRACT BY TRANSITION INDUSTRIES FOR A 2.1 MILLION TONS PER YEAR ULTRA-LOW CARBON METHANOL PLANT IN MEXICO BASED ON ITS PROPRIETARY NX ADWINMETHANOL® ZERO TECHNOLOGY NEXTCHEM’s proprietary NX AdWinMethanol® Zero offers an innovative process combining cutting-edge solutions to minimize carbon emissions, thanks to its autothermal reforming (ATR) technology The plant […]