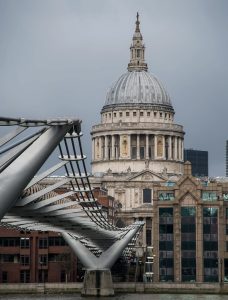
IMTOF 2023
The International Methanol Technology Operators Forum (IMTOF) met at the Leonardo Royal St Paul’s hotel in London from June 11th-14th.
The International Methanol Technology Operators Forum (IMTOF) met at the Leonardo Royal St Paul’s hotel in London from June 11th-14th.
Although the nitric acid industry has an extensive history dating back centuries, nitric acid production continues to be a dynamic process with bespoke system solutions necessary per plant rather than a one size fits all. Kate Cardonne of Johnson Matthey discusses strategies to balance the cost and performance in nitric acid production.
Horisont Energi has the aspiration to develop the most carbon and energy efficient blue ammonia plant in the world, an environmentally friendly plant with a focus on sustainable solutions. This article describes the main features of the Barents Blue Ammonia project, such as 99% carbon capture rate target, a high degree of modularisation, winterisation, infrastructure for ammonia and CO2 management and the provision for future expansion.
The world’s transition toward the use of hydrogen and ammonia as clean energy and fuel sources will depend upon production technologies that are affordable, scalable, and meet net zero carbon targets. 8 Rivers recently introduced8 RH2 , a groundbreaking solution that offers world-leading efficiency in hydrogen production and captures over 99% of CO2 emissions. Maulik Shelat of 8 Rivers provides an overview of the technology with a comparison to other low-carbon hydrogen production technologies.
A round-up of current and proposed projects involving non-nitrogen synthesis gas derivatives, including methanol, hydrogen, synthetic/substitute natural gas (SNG) and gas- and coal-toliquids (GTL/CTL) plants.
Paz Muñoz and Carmen Perez of Stamicarbon discuss the strategic selection of future-proof technology for nitric acid plants. To produce nitric acid in a feasible and sustainable way, manufacturers must carefully choose the right technology and consider the capex and opex involved in the production process to ensure long-term profitability.
While demand for ammonia remains – for now at least – strongly tied to fertilizer and farming, over the three decades that I’ve edited this publication, methanol’s story has been a very different one, with a succession of major new slices of demand coming every few years from new applications that flare up and then mature or even drop away again. For a while in the 1990s it was MTBE, the oxygenated fuel additive that had a brief flourish in the US before being shut down by leaking fuel tanks leaching into ground water. Then there was dimethyl ether (DME) as a blendstock for LPG, and methanol itself directly blended into gasoline in China to keep up with soaring vehicle fuel demand. More recently, methanol to olefins (MTO) has added almost another 25% of demand over and above existing chemical and fuel uses. But as the world cracks down on coal production and use, China’s attempt to use methanol as a way of using domestic coal to replace imported oil seems to have passed its high water mark and begun to recede.
Hydrocarbon-based production of ammonia carries an unavoidable carbon footprint. But one of the best methods for mitigating that footprint is already here: ultra-low carbon-intensity ammonia production, also known as “blue” ammonia. With blue ammonia production, a typical ammonia plant can sequester or repurpose game-changing volumes of carbon dioxide that would otherwise end up in the atmosphere. To help foster an optimal understanding of the benefits, Ameet Kakoti and Per Juul Dahl of Topsoe A/S provide an overview of the technologies that can help any ammonia operation achieve and maintain sustainable operations – sooner rather than later.
A new book by leading industry expert Kish Shah looks at all aspects of ammonium nitrate production.